www.industryemea.com
09
'24
Written on Modified on
ENERGY-EFFICIENT SURFACE PROTECTION FROM DÜRR FOR THE NEW REAR CENTER TANK OF THE AIRBUS A321XLR
Premium AEROTEC Augsburg has commissioned Dürr for its largest individual project to date.
www.durr.com
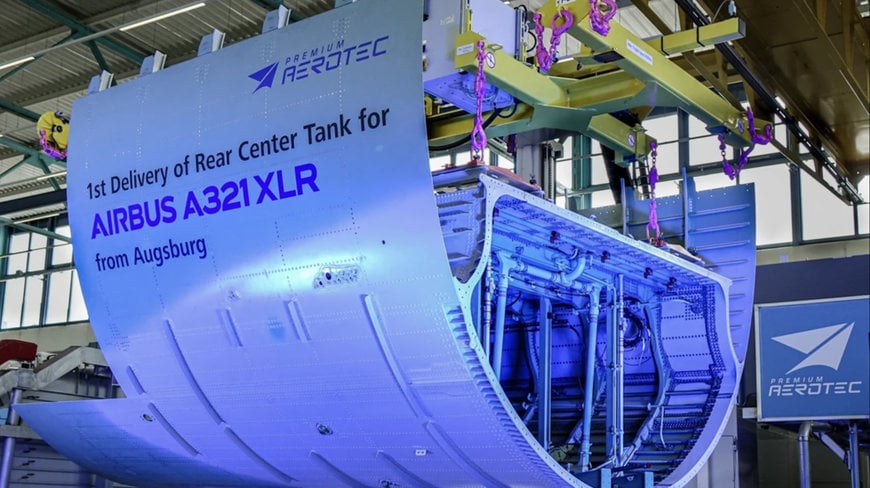
The paint shop currently being built as a turnkey system for the Airbus division Premium AEROTEC is the largest individual project to date for the mechanical and plant engineering company, which it is undertaking for the Airbus Group. The system will be used to coat the extra tank responsible for the high range of the new Airbus A321XLR. For the first time, an all-electric exhaust purification system will also be integrated into one of Premium AEROTEC’s paint shops at the Augsburg site, helping to reduce CO2 emissions.
The fuel tank integrated into the fuselage of the Airbus A321XLR is the key component in transforming the former short- and medium-haul planes into the new XLR (eXtra Long Range) long-haul version. Known as the rear center tank (RCT), its extended capacity of 13,000 adds up to 8,700 kilometers to the aircraft's range. The rear center tank is produced exclusively at the Augsburg site.
High requirements for surface protection and tightness
The turnkey project covers the entire process, from preparation to sealing to actual painting. The new paint shop consists of sealing, cleaning, and painting booths. It also includes surface and leak testing. The requirements regarding corrosion and diffusion are high. The tank surface needs to withstand the extreme conditions on the underside of aircraft without corroding.
Special air ducting system lowers energy consumption
To meet the high requirement for surface protection, painting booths need constant temperatures and humidity. Conditioning requires a lot of energy, especially for paints that are applied manually. The use of recirculated air is not permitted, so the booths are operated with supply and exhaust air. “To make the process more energy efficient for Airbus, we are implementing a component-specific air ducting system that greatly reduces the amount of air required, but still satisfies the safety requirements and standards. The less air that needs to be conditioned, the lower the energy consumption,” explains Marc Furmannek, Key Account Manager at Dürr. Additionally, energy recovery systems are used that recycle 65 percent of the energy contained in the exhaust air, repurposing it for conditioning the fresh air and further minimizing energy consumption.
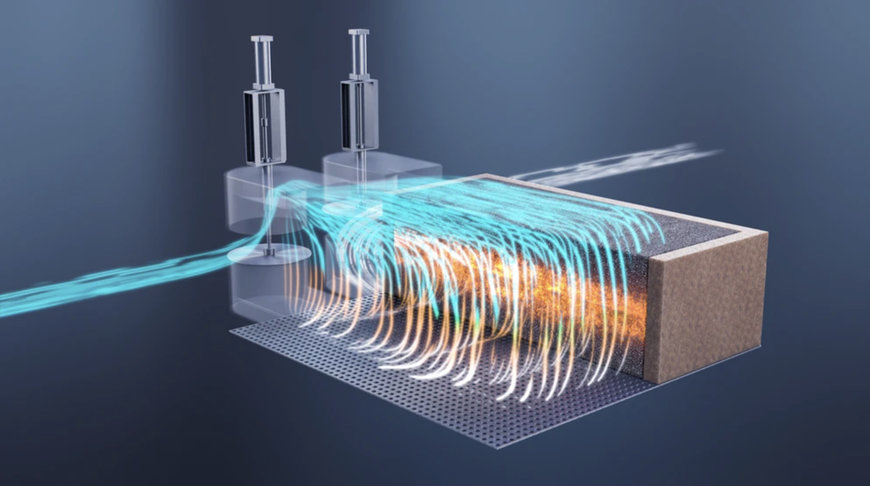
Pollutant removal without additional CO2
For sustainability reasons, Premium AEROTEC opted for an all-electric exhaust air purification system in the form of Oxi.X RV. This system uses regenerative thermal oxidation (RTO) with a flameless operating mode and a unique design. The advantage is that the combustion process for purifying the exhaust air takes place entirely within the heat exchanger material. This means there is no open flame, resulting in especially low nitrogen oxide emissions. Since the entire process is electrified, it can be operated with zero emissions, meaning without additional CO2, using green electricity.
Increasing economic efficiency
The exhaust air streams produced contain very low solvent concentrations. However, since the volume of exhaust air is high, a Sorpt.X CD is placed upstream of the Oxi.X RV to concentrate the exhaust air streams. This reduces the volume, thereby increasing the solvent concentration – by up to forty times the original pollutant concentration. This technical effect means that the downstream Oxi.X RV can be smaller and needs no additional heating energy during solvent operation, positively affecting the cost-benefit ratio of the exhaust air purification.
www.durr.com