www.industryemea.com
25
'24
Written on Modified on
New NSK high-load-capacity tapered roller bearings selected for wind turbines
A leading European manufacturer of wind turbines will use NSK high-load-capacity tapered roller bearings in the gearboxes of its 15 MW class offshore wind turbines.
www.nskeurope.com
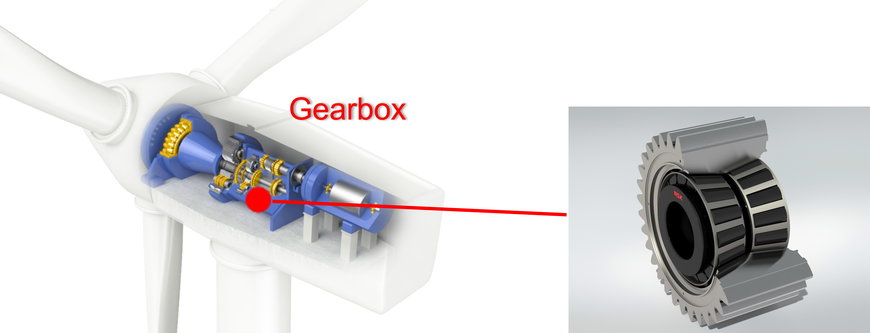
The gearbox of a wind turbine and the new NSK high-load tapered roller bearing
The decision to specify the next-generation NSK roller bearings hinged on several key factors. First and foremost, the bearings offer an increase in load capacity of approximately 25% over the conventional product by optimising the roller crowning shape (a slight arc shape that avoids stress concentration at the roller ends). The new bearings also deliver longer bearing life and lighter weight, making them perfect for reducing the construction and maintenance costs of large wind turbines.
The arrival of NSK’s bearing is timely: in 2023 the EU committed to 111 GW of offshore renewable energy by 2030 with 26 member states signing the European Wind Charter.
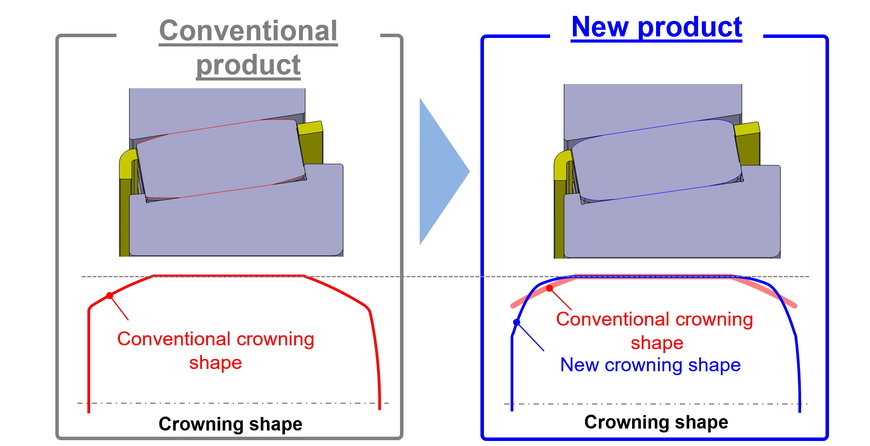
NSK’s optimised roller crowning shape
By adopting the high-load-capacity tapered roller bearing, manufacturers in this sector can overcome engineering challenges specific to wind turbines. For instance, the optimised shape of the bearing’s roller crown helps to withstand the demanding operating conditions that wind turbine gearboxes endure. NSK leveraged its numerical simulation expertise to derive the shape and equalise the contact surface pressure between the rollers and the inner and outer rings. This capability prevents excessive surface pressure at the roller ends, even under high loads, facilitating 25% more load capacity and more than double the service life of the conventional product.
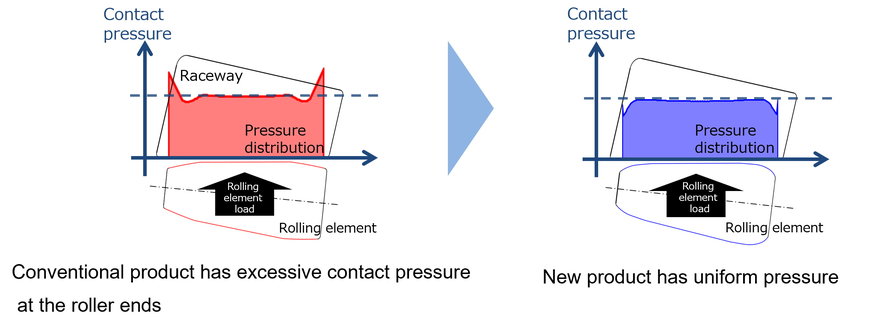
The new NSK bearings offer uniform contact pressure at the roller ends
With the conventional bearing, excessive contact pressure at the roller ends is unavoidable, typically prompting the selection of larger bearings to handle the high loads. In contrast, pressure is uniform with the new roller bearing, negating the need for upsizing and allowing a weight reduction of more than 30% under the same usage conditions.
As a final point of note, NSK’s expertise in production engineering saw the development of a new high-productivity processing technique to create the product’s intricate crowning shape.