Toplus IQ clamping chuck wins the "MM Award" for innovation at AMB 2016
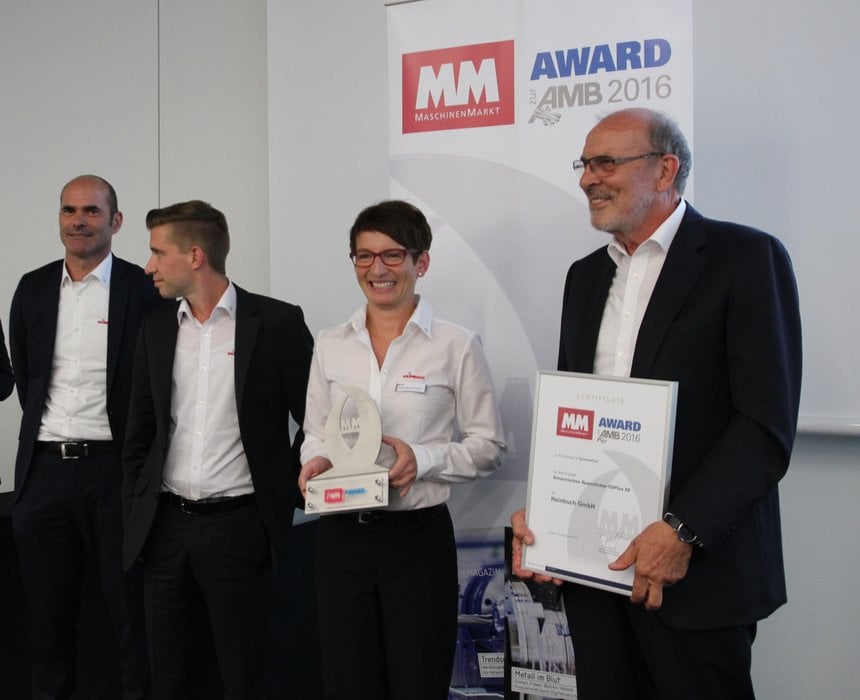
A happy and visibly proud Gerhard Rall holds the award in his hands [from left to right: Attillio Mandarello, Research & Development Manager at Hainbuch, Sebastian Ivenz, Research & Development Engineer at Hainbuch, Anke Reichenecker, Marketing Manager at Hainbuch and Gerhard Rall, Hainbuch CEO.
After receiving the »100 places for Industry 4.0« award last May, from the Baden-Württemberg Industry 4.0 Alliance, for two manufacturing/networking solutions, Hainbuch, has now scored a second success in 2016. At the AMB exhibition, the newly-developed intelligent Toplus IQ clamping chuck won the MM Award for innovation. A large number of AMB exhibitors were in the competition for the innovation prize. In the clamping device category, an 8-member jury had the task of selecting a winner from three finalists, and Hainbuch's chuck emerged victorious. The jury praised the pioneering spirit and the exceptional engineering performance of the family-run company from Marbach. The chuck scored good ratings in all the decisive criteria, including degree of technical innovation, usefulness for industry, environment and society, and economic efficiency. "Innovation is when the customer says »Wow«. And it seems like we got that reaction from the jurors", said CEO Gerhard Rall smiling joyfully after the award. "In the past, not to put too fine a point on it, it was all about iron and steel, but now mechatronics and digitalization play a very important role in product development", explained Rall.
A chuck with exceptional capabilities
With its sophisticated integrated sensor technology, it permanently measures the actual clamping force applied to the workpiece. Using contactless transmission of both data and energy, measurement results are sent directly to the machine´s control system for processing. The control system performs a comparison with the target values and then outputs messages or makes adjustments as required. In-line checking of the dimensions of each workpiece when it is clamped can even be performed directly using an integrated system of measurement sensors. The temperature near to the workpiece is also monitored to allow temperature compensation for example.
Data produces big pay-offs
Using the data harvested by the control system, it is possible to perform long-term monitoring, so-called »Condition Monitoring«. Condition monitoring has two objectives: safety and machine efficiency. Monitoring the status of the machine is a mandatory prerequisite for need-oriented and status-oriented preventive maintenance and servicing. Modern condition monitoring systems however put very tough requirements on the sensor systems, data capture and automated measurement data processing, as well as system specific knowledge. However they also have the greatest cost savings potential, because the expected working life of critical machine parts can be exploited to the maximum while any required maintenance interventions can simultaneously be planned to mesh in with production schedules. This makes it possible to prevent unnecessary downtime which in turn increases machine availability and reduces production shortfalls. It is good for the bottom line because the chuck can detect reject parts. For example if a workpiece breaks, it is discarded and the value-adding process is interrupted.
This improves quality and reduces personnel costs. As a result, employees can focus more on proactive tasks. Permanent monitoring reduces the risk of workpiece loss and the resulting damage to man and machine. And that is a very significant advantage.
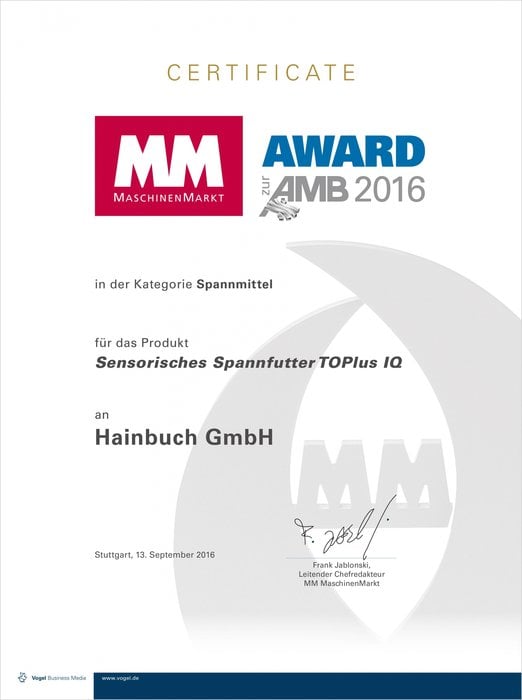
The Toplus IQ chuck scored high ratings in all categories