www.industryemea.com
10
'24
Written on Modified on
ABB to help South African paper producer upgrade operations and accelerate digitalization
ABB will provide its latest ABB Ability System 800xA distributed control system (DCS) for the mill’s Paper Machine 3 (PM3).
global.abb
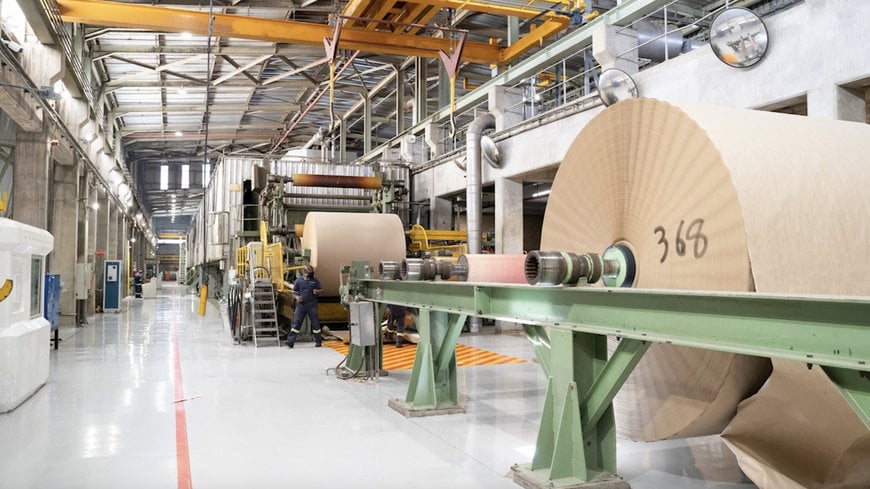
Control system upgrades made by ABB will enable Neopak to raise its annual production outputs to around 85,000 tons. Image Neopak
Neopak, a leading manufacturer of containerboard and paper products, has renewed its partnership with global technology company ABB to upgrade the existing automation system at its Rosslyn Paper Mill in Pretoria, South Africa. The mill produces a variety of paper grades, including high-performance recycled liner and fluting, paper bags, core board, and plasterboard – essential materials for local industry applications such as building hardware, converters, and corrugators for packaging.
ABB will provide its latest ABB Ability™ System® 800xA distributed control system (DCS) for the mill’s Paper Machine 3 (PM3). The existing system, which includes the ABB Quality Control System (QCS), a current ABB DCS, and variable speed drives, will be upgraded to leverage new technological advancements and digital integrations. This upgrade will pave the way for Neopak to achieve optimal efficiency, productivity, and consistency through smart manufacturing.
Since its construction between 2007 and 2009, Neopak’s PM3 has been operational for over 15 years, with recent process adjustments boosting production to approximately 85,000 tons per annum. With ABB's upgrade, Neopak expects to significantly enhance production efficiency and product quality, enabling the mill to meet rising market demands for essential materials while upholding the highest standards of quality and sustainability.
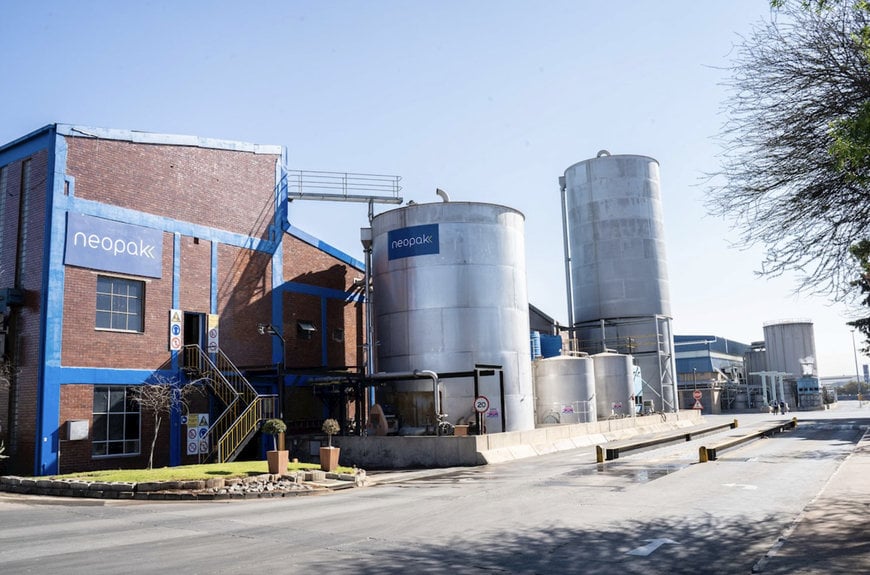
Neopak's Rosslyn Paper Mill in Pretoria produces a wide range of paper grades for the South African market. Image Neopak
Looking ahead, Neopak's future digital operations will emphasize advanced process control (APC), cyber security, and increased accuracy and efficiency across the entire machine and process. ABB has been tasked with defining a strategic digital roadmap for Neopak, facilitating a phased implementation of industry-leading digital solutions tailored for the pulp and paper sector, including enhanced cyber security and advanced process control (APC). Designed for peak performance, the ABB Ability System 800xA DCS will empower Neopak to adopt sophisticated control strategies and automation techniques, ensuring long-term operational efficiency.
System 800xA integrates with various process components, streamlining operations and optimizing production schedules. This, along with the critical next stages of Neopak’s digital transformation journey set to begin work in 2025, will result in increased efficiency and throughput for the manufacturer, alongside significant improvements in yield and paper quality. Additionally, the APC capabilities enable more precise management of the paper machine, leading to reduced waste. The system also fosters streamlined operations through a centralized platform, simplifying process monitoring and control for operators. This empowers them to make informed decisions and respond quickly to process variations.
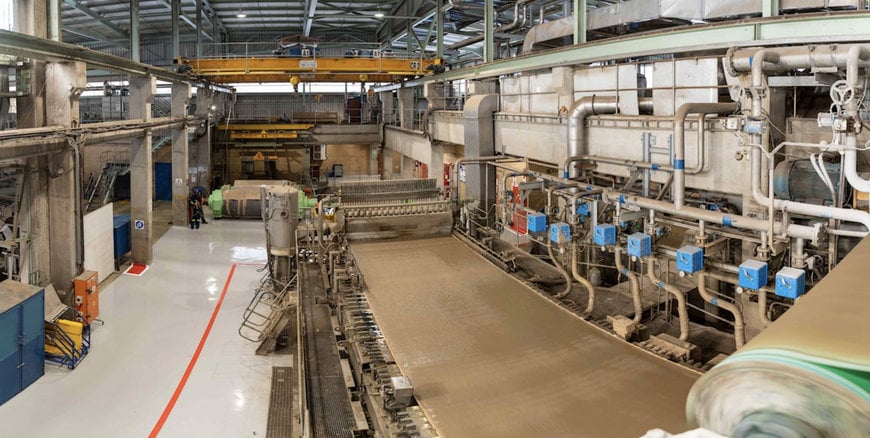
PM3 was commissioned in 2009 and will now reach new heights in efficiency and quality to meet market demands. Image Neopak
The upgraded process controls and automation strategies will position Neopak for long-term success, while also granting them the flexibility to seamlessly integrate ABB's digital solutions for future optimization.
The project commissioning is expected to be completed in Q3 2025.
Neopak, a leading manufacturer of containerboard and paper products, has renewed its partnership with global technology company ABB to upgrade the existing automation system at its Rosslyn Paper Mill in Pretoria, South Africa. The mill produces a variety of paper grades, including high-performance recycled liner and fluting, paper bags, core board, and plasterboard – essential materials for local industry applications such as building hardware, converters, and corrugators for packaging.
ABB will provide its latest ABB Ability™ System® 800xA distributed control system (DCS) for the mill’s Paper Machine 3 (PM3). The existing system, which includes the ABB Quality Control System (QCS), a current ABB DCS, and variable speed drives, will be upgraded to leverage new technological advancements and digital integrations. This upgrade will pave the way for Neopak to achieve optimal efficiency, productivity, and consistency through smart manufacturing.
Since its construction between 2007 and 2009, Neopak’s PM3 has been operational for over 15 years, with recent process adjustments boosting production to approximately 85,000 tons per annum. With ABB's upgrade, Neopak expects to significantly enhance production efficiency and product quality, enabling the mill to meet rising market demands for essential materials while upholding the highest standards of quality and sustainability.
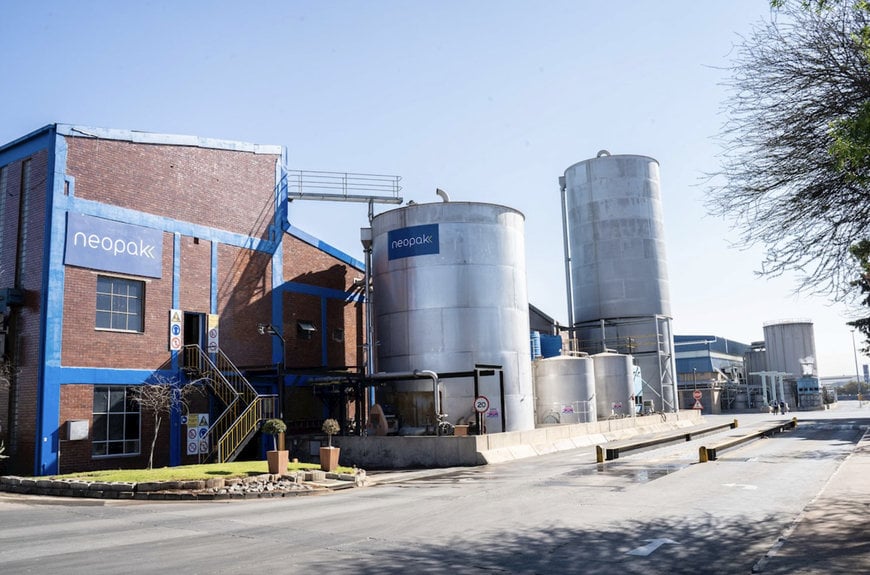
Neopak's Rosslyn Paper Mill in Pretoria produces a wide range of paper grades for the South African market. Image Neopak
Looking ahead, Neopak's future digital operations will emphasize advanced process control (APC), cyber security, and increased accuracy and efficiency across the entire machine and process. ABB has been tasked with defining a strategic digital roadmap for Neopak, facilitating a phased implementation of industry-leading digital solutions tailored for the pulp and paper sector, including enhanced cyber security and advanced process control (APC). Designed for peak performance, the ABB Ability System 800xA DCS will empower Neopak to adopt sophisticated control strategies and automation techniques, ensuring long-term operational efficiency.
System 800xA integrates with various process components, streamlining operations and optimizing production schedules. This, along with the critical next stages of Neopak’s digital transformation journey set to begin work in 2025, will result in increased efficiency and throughput for the manufacturer, alongside significant improvements in yield and paper quality. Additionally, the APC capabilities enable more precise management of the paper machine, leading to reduced waste. The system also fosters streamlined operations through a centralized platform, simplifying process monitoring and control for operators. This empowers them to make informed decisions and respond quickly to process variations.
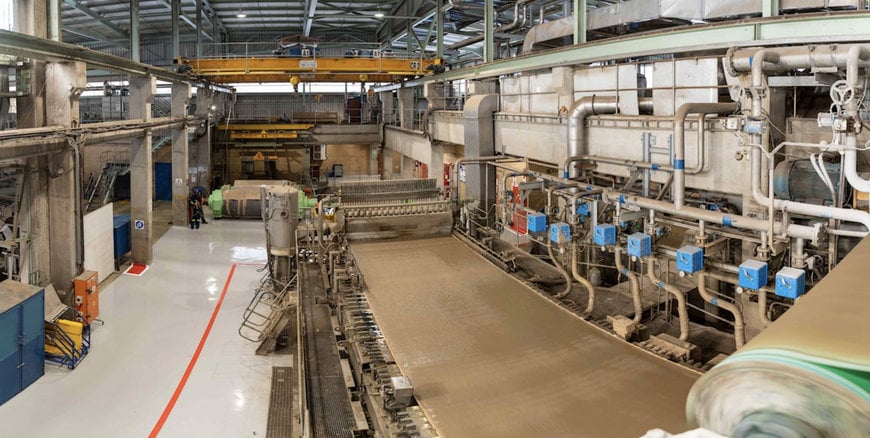
PM3 was commissioned in 2009 and will now reach new heights in efficiency and quality to meet market demands. Image Neopak
The upgraded process controls and automation strategies will position Neopak for long-term success, while also granting them the flexibility to seamlessly integrate ABB's digital solutions for future optimization.
The project commissioning is expected to be completed in Q3 2025.
new.abb.com