www.industryemea.com
16
'25
Written on Modified on
Insulation Resistance – the case for real time condition monitoring
Specifically designed to address the demands of the Oil & Gas sector, Viper Innovations' V-LIM is an accurate and precise sensor which monitors electrical cable integrity.
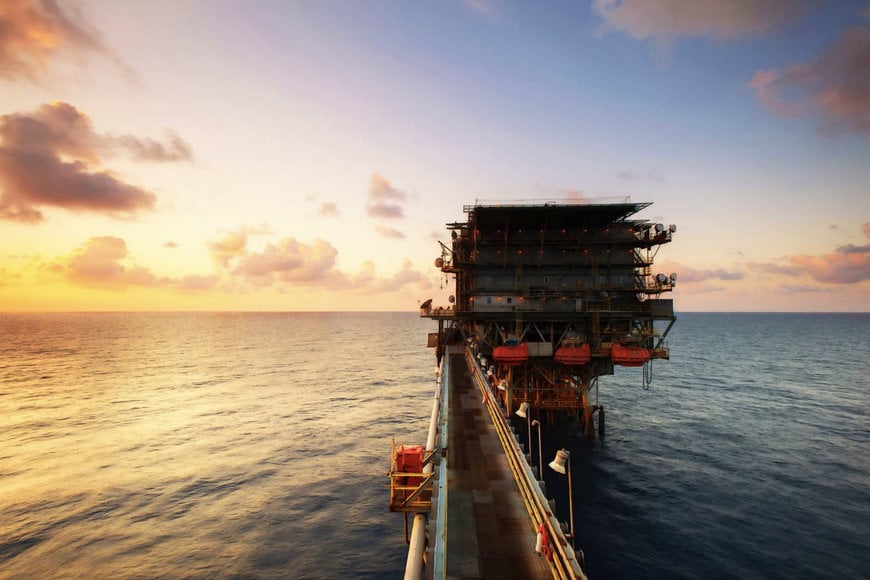
Condition monitoring of mechanical equipment used in offshore and subsea operations is both a regulatory and operational requirement. Mechanical failure can be catastrophic, leading to production loss and safety risks. Although the same can be said of electrical control system failure caused by low insulation resistance (IR), the standards that do exist requiring IR monitoring do not require the same level of reporting, leaving operators in the dark. As well as taking years for replacement umbilicals to be supplied, these cables can cost thousands of US dollars per metre.
“IR is typically monitored using a Line Isolation Monitor (LIM) or an Insulation Monitoring Device (IMD) on the umbilical cable running from topside to subsea control equipment, which are a requirement for safety reasons,” explains Houston-based President of Viper Innovations Inc., Jamie Carrig.
“However, the legacy LIMs in the field typically have a limited measurement range, which means not only do operators have limited visibility of the systems condition, but it’s often too late to act by the time the warning comes. This can lead to operational issues due to equipment having to be shut down. Or, in worst-case scenarios, replacing a piece of subsea hardware.”
Working blind for 99% of an asset’s life
One of the hardest elements of the subsea electrical system to replace is the umbilical, yet the device monitoring its health only starts providing insights during the last 1% of its life. The standard response to this kind of subsea electrical systems failure is replacing the umbilical, which can potentially take years once the new equipment is ordered and replaced. During this time, the subsea assets are unproductive, costing tens of millions of dollars in lost production.
“With legacy LIMs installed to meet the regulatory requirements and nothing more and designed to operate when equipment is approaching failure, most operators are running blind for 99% of the electrical system’s life,” continues Jamie. “You get a snapshot of the IR when a channel is about to fail, with little data about what led to the IR falling below safety requirements.”
In contrast, ongoing, detailed monitoring is commonplace in other areas of production. For example, pipeline pressures are continuously monitored so immediate action can be taken in the event of a catastrophic depressurisation that indicates an integrity breach. Or the pattern associated with a gradual build-up of pressure could indicate internal hydrocarbon deposits are at the level when a cleaning pig is needed. A different pressure data pattern might show a localised deformation constricting flow that needs a physical inspection and intervention.
“Ongoing IR monitoring and the historic data provides similar insights,” says Jamie. “For example, significant IR drops early on in an asset’s life could indicate issues with installation or product quality, which if remediated quickly can extend the systems life. This is a vital operational insight and can only come from ongoing monitoring. Preventive action taken later becomes more costly and is sometimes not viable.”

What is healthy IR?
Jamie notes that there are multiple factors that contribute to determining if you have good IR, which include safety risk, operational risk, age, historical trends and dependency. The safety threshold for good IR is going to be lower than the operation risk threshold, especially when you have historical information.
Jamie highlights that this is where LIMs again provide vital insight: “If you have gone from 100MOhms to 10MOhms in a matter of weeks, your trend will indicate that you don’t have much time to act and you are about to lose power. Depending on levels of redundancy in the system this can become a major issue leading to loss of production.
“However, if you have moved from 100MOhms to 10MOhms in a matter of years, that will tell you a different story. So 10MOhms mean different things in both these scenarios. The absolute readings are important but so are the trends.” An indication of emerging operational risk can come way before 10MOhms, but in most systems this is not seen.
An added complication is that many legacy systems only have alarms that go back to the control system, from the LIM to an office onshore/offshore, so the subsea operations team responsible for maintaining production of the field does not always see any data trends.
“We are working with several operators who wants live data from 50+ electrical channels currently managed by 5 to 10 different individuals to be shared with the whole team in real time,” Jamie adds.
“I am certainly seeing a trend where customers are trying to gain visibility and insights on their electrical systems, especially with plans to add more subsea infrastructure which increases the dependency on aging equipment.”
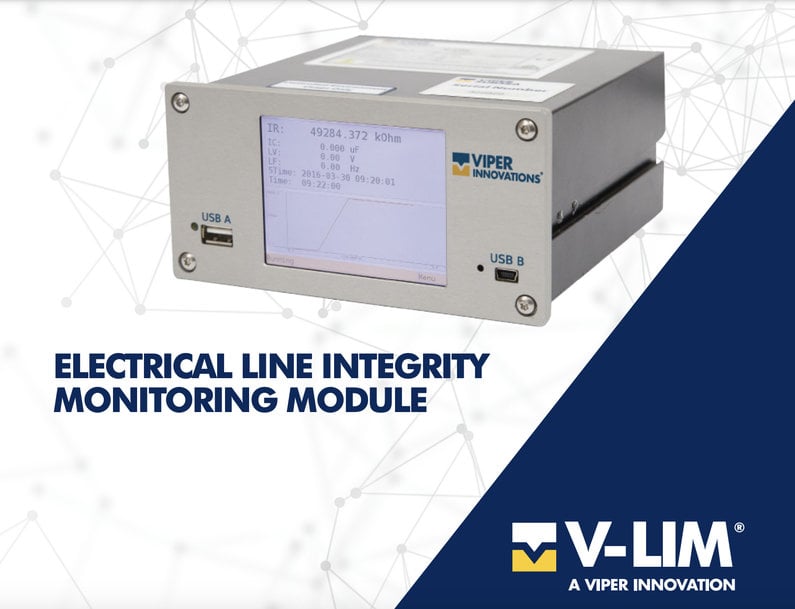
The role of LIMs for condition monitoring and preventative maintenance
The industry wants safe and uninterrupted production, so the solutions to managing the risks associated with low IR are a combination of factors: education, looking at the challenge as an opportunity, and regulation to change behaviours.
Jamie again highlights the mechanical system monitoring comparison: “You wouldn’t run a platform’s mechanical plant today without ongoing condition monitoring that drives preventative maintenance. This makes good business sense as asset management costs are generally lower because there are fewer, if any, expensive failures – you’ve taken action to address the issue before it becomes a problem. So why are vital elements of the electrical system operated without ongoing monitoring in the same way?”
There is a compelling business case for investing in a LIM for ongoing condition monitoring as well as safety. The IR data tells a story about the specific installation that informs the operator about when and how to take action, empowering operators to work proactively rather than reactively.
Historically, LIMs started as a safety measure driven by regulations. Now they offer safety plus intelligent monitoring with increased visibility and trending capabilities. The latest generation of LIMs are straightforward to retrofit, meaning it is a relatively easy step to protect hundreds of millions of dollars of production.
Jamie concludes: “In a world of AI and digital twins, real time data that can be used not just to see what is happening, but also model and predict the future is now the standard. There are many benefits of being able to track a subsea electrical system’s health from first oil, rather than as the system approaches failure, and we look forward to continuing to work with our customers to mitigate risks and the extend the life of their systems.”
Learn more about V-LIM
www.viperinnovations.com