From friction to function: How to approach noise and vibration in bearings
Here, Chris Johnson, managing director of bearing specialist, SMB Bearings, explores the causes of noise and vibration and shares strategies to ensure optimal ball bearing performance in critical applications.
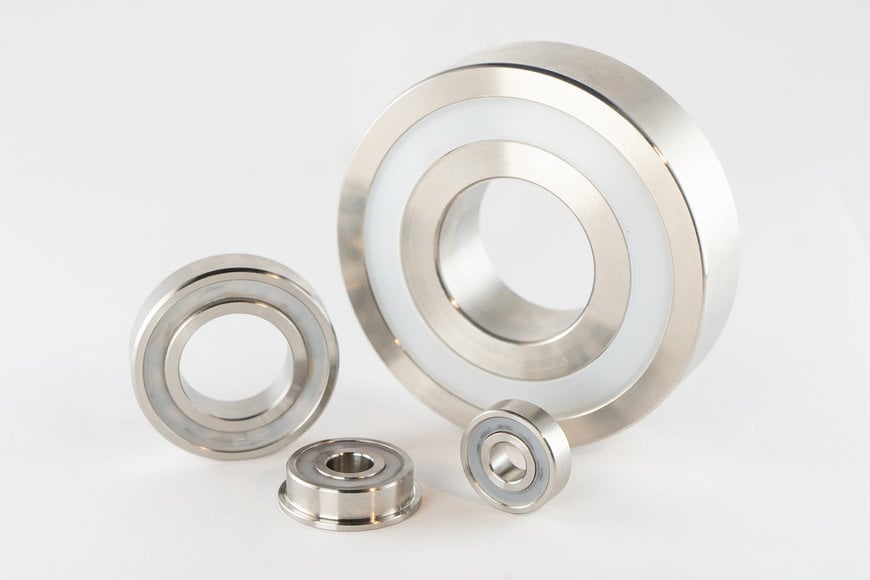
Noise and vibration in ball bearings threaten precision and safety in critical systems, costing manufacturers billions annually in maintenance and lost productivity. As demand from medical, aerospace and industrial sectors drives the USD 120.98 billion global bearings market towards a compound annual growth rate (CAGR) of 9.5 per cent by 2030, tackling these challenges has never been more urgent.
According to the report, An Overview of Bearing Vibration Analysis, from Schaeffler UK Limited, increased vibration levels in bearings can have detrimental effects on machinery performance. The report reveals that excessive vibration is a leading cause of premature bearing failure, with up to 30 per cent of failures linked to poor vibration management. This can lead to significant equipment damage and downtime.
Contamination is one of the most common causes of bearing noise and vibration, as even microscopic particles like dust or moisture can infiltrate a bearing and disrupt the smooth motion of its rolling elements. This disruption creates irregularities that amplify vibrations and operational noise. Poor lubrication might worsen these issues, as insufficient or inappropriate lubrication can increase friction, heat generation and wear in the bearing.
Misalignment of the bearing, either during installation or operation, also contributes to vibration, as uneven loads cause stress on the bearing components. Additional factors like material defects, surface roughness or excessive preload can further degrade performance — particularly in applications requiring silent operation. Across all sectors, whether medical, aerospace or industrial, these challenges demand a consistent approach to mitigation.
The consequences of noise and vibration are especially pronounced in industries and applications where precision and reliability are essential. Take medical imaging systems such as magnetic resonance imaging (MRI) and computed tomography (CT) scanners, for instance. Even minor vibrations can distort the images and potentially compromise the accuracy of medical diagnoses. For instance, a slight vibration in an MRI scanner could blur the imaging, leading to an unclear or delayed diagnosis.
Bearings in these applications must also operate silently and in non-magnetic environments because noise interferes with sensitive diagnostic equipment and magnetic materials can disrupt the strong magnetic fields generated by MRI machines.
This necessitates the use of advanced materials, like ceramics, which are non-magnetic, lightweight and resistant to wear. These properties ensure smooth, quiet operation and prevent interference with the imaging process, making them ideal for precision medical applications.
In the aerospace sector, bearings are subjected to extreme loads and speeds, which makes vibration control essential for safety and performance. Jet engine bearings, for example, must endure significant thermal and mechanical stress. Let’s say the engine is running at approximately 10,000 rotations per minute (RPM), with the turbine reaching temperatures of up to 1,200 degrees Celsius. At the same time, the jet engine’s components are expected to support consistent balance and minimise vibration to ensure the engine performs efficiently.
Avionics systems also rely on ultra-quiet bearings to avoid disrupting the accuracy of sensitive navigation and control instruments. Despite the varied applications, the same underlying principles apply, reducing vibration, managing heat and ensuring alignment are non-negotiable.
Implementing targeted solutions
To tackle noise and vibration, bearings need proper lubrication, precise alignment, advanced materials like ceramics, and designs resistant to contamination.
For an effective barrier against contamination, shielded or sealed bearings are an excellent choice; delivering an extended lifespan and maintaining consistent performance. For applications like food processing equipment, stainless steel bearings with rubber contact seals are commonly used to resist moisture and particulate ingress.
Proper lubrication also plays a vital role in damping noise and reducing wear. Advanced greases, designed for low noise applications, can be formulated to meet the specific demands of high-speed, high-temperature or chemically challenging environments. Surgical robots, for instance, often use specialised lubricants that ensure both silent operation and biocompatibility.
Next, precision in mounting and alignment is equally important. Misaligned bearings not only generate excessive noise but also suffer from uneven stress distribution, which accelerates wear. Precision mounting fixtures and alignment tools can help ensure that shafts and housing are perfectly aligned, reducing vibration and improving operational longevity.
Preventive maintenance
The role of bearing design in noise and vibration control extends beyond material choice. In applications like CNC machines, where precision is critical, vibration-dampening housings can minimise the transmission of noise to surrounding structures. Bearings with non-contact seals eliminate rubbing, further reducing noise in high-speed machinery.
In mining conveyors or heavy industrial equipment, split bearings simplify maintenance while reducing the risk of misalignment, ensuring consistent performance in demanding environments.
Proactively diagnosing noise and vibration issues is another key element of an effective maintenance strategy. Tools such as accelerometers and laser vibrometers allow engineers to detect anomalies in bearing performance, enabling timely interventions. Ultrasonic detection devices, which identify high-frequency sound waves generated by faulty bearings, are particularly effective for diagnosing early-stage contamination.
In applications where precision and reliability are paramount, addressing the challenges of noise and vibration in ball bearings is a technical necessity. These issues stem from various mechanical factors, such as contamination, poor lubrication, misalignment and material defects, all of which are entirely manageable with the right combination of preventative measures, advanced materials and proactive maintenance strategies.
By employing precision shielded or sealed bearings, choosing application-specific lubricants and ensuring precise alignment during installation, engineers can significantly reduce noise and vibration while extending the lifespan of their equipment.
Whether in a medical imaging system, a jet engine or a CNC machine, the stakes are high and the margins for error are slim. The impact of bearing noise and vibration may go far beyond inconvenience but with targeted interventions, these challenges can be transformed into opportunities for improved efficiency and performance.
www.smbbearings.com