www.industryemea.com
21
'24
Written on Modified on
binder Connector presents PBC 15 female field-wirable and male panel mount
The electrical connector compass that guides you in choosing the perfect circular connector.
www.binder-connector.com
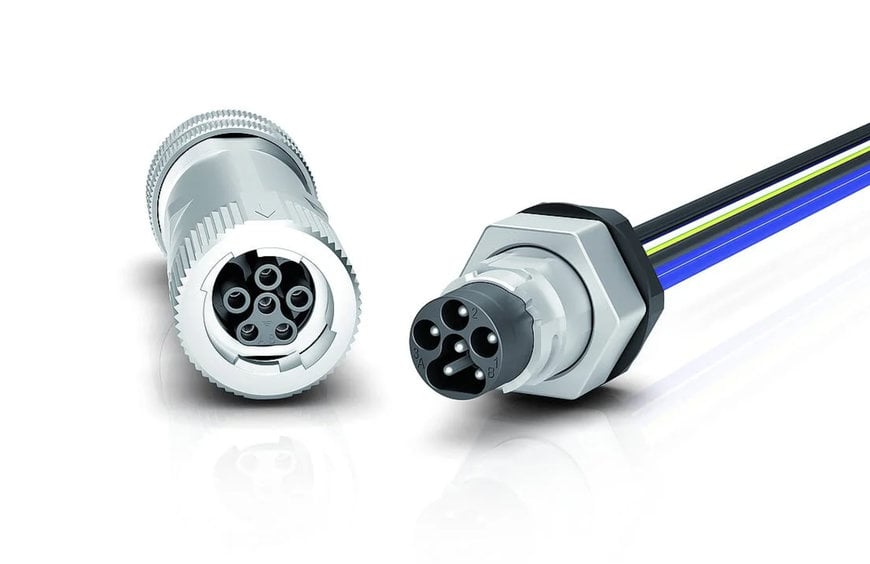
Electrical connectors are essential components in a wide range of electronic and electrical systems, enabling the transfer of power and signals between different devices. By providing a reliable means of joining circuits, they enable communication and functionality across applications ranging from consumer electronics to industrial machinery.
Among the many types of electrical connectors, circular connectors stand out for their robust design and user-friendly features. These connectors, including options like the 12-pin configuration, are specifically designed to deliver secure and efficient connections in space-constrained environments while offering protection against environmental factors such as moisture and dust.
The adaptability of electrical connectors makes them indispensable for applications requiring reliable and durable connections. Circular electrical connectors are available in various designs and pin configurations, tailored to accommodate diverse power and data transmission requirements. Thanks to their ability to maintain electrical integrity even in challenging conditions, they are a preferred choice for professionals seeking optimal performance and reliability in their systems.
Types of circular electrical connectors
Understanding the different types of circular connectors is crucial for selecting the right solution for your specific application, as each type serves distinct purposes based on installation requirements. Circular connectors can be categorized into different types including panel-mounted connectors, overmould cable connectors, and field-wirable connectors, each designed for specific environments and functionalities. The binder portfolio also encompasses other connector types and special components including solenoid valve connectors, cable splitters, twin distributors, distributor blocks, lead-through for control cabinets, adapters, led lights, and raw cable. For simplicity of this text, we focus on the main connector types, along with their strengths:
Panel-Mount Connectors
These connectors are specifically designed for mounting onto the housing of equipment or devices, making them well-suited for applications where the connector remains stationary. Common applications include machinery, control panels, and equipment enclosures. Use Case: Ideal for permanent installations where the connector is an integral part of a fixed device.
Field-Wireable Connectors
These connectors are designed for on-site assembly and repair, enabling re-wiring directly in the field without the need for specialised tools. They provide flexibility in applications that require frequent wiring modifications or replacements. Use Case: Ideal for maintenance-intensive environments such as industrial automation or machinery, where quick and efficient connector replacement is essential.
Overmoulded Cable Connectors
These connectors are fully encapsulated in a protective moulding, offering superior strain relief and excellent protection against environmental factors. Known for their durability, they withstand harsh conditions and deliver reliable, consistent performance over time. Another advantage is that they are ready for immediate use and can be connected directly without the need for complex assembly. Use Case: Suitable for heavy-duty industrial applications or environments subject to frequent mechanical stress.
- Connecting cordsets (cable-to-cable connector): Designed to connect two cable ends, these connectors allow for quick extension or joining of cables. They provide flexibility in wiring systems that may need to be adapted or extended over time. Use Case: Applications requiring cable extensions or connections across long distances.
- Single ended cordsets: With a connector on one end and open wires on the other, single-ended cordsets simplify direct device connections to power or control systems. Their pre-configured design ensures quick installation and reliable performance, making them ideal for industrial and automation applications. Use Case: Ideal for direct device connections where quick and dependable wiring is required.
Key characteristic in choosing the right circular electrical connector
Selecting the appropriate circular electrical connector is crucial for ensuring the optimal performance and reliability of a project. Given the diverse nature of application requirements, it is essential to choose a connector that meets the specific needs of the intended application.
The following section offers a structured, step-by-step guide to help identify and assess the key characteristics to consider when selecting a circular connector.
1. Connector Type
When selecting a circular electrical connector, the first step is to identify the appropriate connector type. As mentioned earlier, it is crucial to choose a connector type that aligns with the specific requirements of the intended application, ensuring optimal functionality and reliability.
2. Number of Contacts
The number of contacts in a connector indicates how many circuits it can support. It is essential to ensure that the connector has an adequate number of contacts to handle both the power and data signals required by your application.
Selecting the appropriate circular electrical connector is crucial for ensuring the optimal performance and reliability of a project. Given the diverse nature of application requirements, it is essential to choose a connector that meets the specific needs of the intended application.
The following section offers a structured, step-by-step guide to help identify and assess the key characteristics to consider when selecting a circular connector.
1. Connector Type
When selecting a circular electrical connector, the first step is to identify the appropriate connector type. As mentioned earlier, it is crucial to choose a connector type that aligns with the specific requirements of the intended application, ensuring optimal functionality and reliability.
2. Number of Contacts
The number of contacts in a connector indicates how many circuits it can support. It is essential to ensure that the connector has an adequate number of contacts to handle both the power and data signals required by your application.
- Low-Contact Connectors (2 to 4 contacts) are suitable for simple applications that only require power transmission or basic signal flow, such as in lighting, basic sensors, or low-power motor control. However, they can still transmit high data volumes, which can occurs via Ethernet protocols rather than purely digital signals.
- Medium-Contact Connectors (5 to 12 contacts) are common in industrial environments where both power and data need to be transferred, such as in automation systems, sensors, or industrial machinery. These provide more flexibility for signal and power segregation.
- High-Contact Connectors (13+ contacts) are used in complex systems like communication networks, multi-channel data acquisition, or high-performance computing systems. They enable transmission of a large volume of data and power through a single interface, supporting advanced control, monitoring, and communication protocols.
- Important: The number of contacts also impacts the voltage and current that can be transmitted through the connector. A higher number of contacts results in smaller distances between the pins, allowing only lower voltages to be safely transmitted to avoid the risk of short circuits. Therefore, it is not always straightforward to classify connectors solely based on the number of contacts as either simple or complex. Factors such as transmission protocols, current and voltage requirements, and specific application conditions also play a crucial role.
3. Gender (Pin/Socket)
Connectors consist of two components: a male element (pin) and a female element (socket). These can either be permanently installed or attached to the end of a cable. In practice, pins and sockets are always used together once the connection is established, making it challenging to classify their usage by application. However, there are certain tendencies: device connectors (panel mounts or flange parts) often feature a socket, while cables typically use a plug. Once the device is connected, both plug and socket are integral to the connection, e.g., a plug in the device and a socket on the cable.
Connectors consist of two components: a male element (pin) and a female element (socket). These can either be permanently installed or attached to the end of a cable. In practice, pins and sockets are always used together once the connection is established, making it challenging to classify their usage by application. However, there are certain tendencies: device connectors (panel mounts or flange parts) often feature a socket, while cables typically use a plug. Once the device is connected, both plug and socket are integral to the connection, e.g., a plug in the device and a socket on the cable.
- Male connectors typically have exposed pins, which can allow for easier contact during mating and faster signal transmission. Male connectors are often used in stationary or fixed components such as control panels, where they will not be exposed to damage from frequent handling.
- The sockets of female connectors offer protection for the internal contacts, reducing the risk of electrical shorts or accidental contact. In applications where accidental exposure to live parts could pose a risk such as high-voltage systems or areas where connectors might be touched), female connectors are safer because their sockets shield the live pins.
4. Locking Type
The locking mechanism ensures a secure connection between the pin and socket. Available locking types include threaded locking, Bayonet locking, Push-Pull locking, Snap-In locking.
Threaded locking mechanisms, such as M12, M8, M16, and M9, are screw-type mechanisms that utilise threading to connect male and female components. They are particularly well-suited to applications where the connector is subjected to constant vibrations, including in industrial automation, transportation, and machinery. The threaded engagement prevents accidental disconnection and provides a robust mechanical bond between components, preventing the connector from loosening even under mechanical stress.
The locking mechanism ensures a secure connection between the pin and socket. Available locking types include threaded locking, Bayonet locking, Push-Pull locking, Snap-In locking.
Threaded locking mechanisms, such as M12, M8, M16, and M9, are screw-type mechanisms that utilise threading to connect male and female components. They are particularly well-suited to applications where the connector is subjected to constant vibrations, including in industrial automation, transportation, and machinery. The threaded engagement prevents accidental disconnection and provides a robust mechanical bond between components, preventing the connector from loosening even under mechanical stress.
- Bayonet locking connectors feature a quick-connect mechanism, whereby a quarter-turn is used to engage or disengage the locking system. This allows for rapid mating and un-mating, rendering them ideal for applications where time-efficient assembly or frequent reconnections are required. In a manner similar to threaded connectors, bayonet locks offer robust vibration resistance; however, they may not be as resilient as threaded types in high-stress environments.
- Push-Pull locking is a mechanism that enables the mating of connectors with a simple push and subsequent locking into place via an internal latching mechanism. To disengage, the user pulls back on the connector housing to release the latch. The system is designed to be extremely user-friendly, making it ideal for applications that require frequent connections and disconnections or quick installation in tight spaces. It is one of the quickest mechanisms to engage, reducing installation time.
- The snap-in locking mechanism employs a spring-loaded apparatus that secures the connector when the male and female components are engaged. Once connected, the mechanism locks the components in place until disengaged manually. Similar to push-pull systems, snap-in connectors require no tools, making them suitable for quick installations. The lightweight and compact nature of snap-in connectors makes them ideal for applications with space constraints. They are widely used in medical devices, test and measurement instruments, and industrial electronics due to their simplicity and efficiency.
5. Current Rating
The current rating (measured in amps per circuit) specifies the maximum current that can safely pass through the connector. It is important to ensure that the selected connector meets the power requirements of your application. This rating can be influenced by various factors, including contact material, thermal management, contact resistance, the number of contacts, and environmental conditions.
6. Rated Voltage
The rated voltage indicates the maximum voltage that a connector can safely withstand. This is one of the most critical specifications to consider when selecting a connector, as it determines the electrical insulation and breakdown voltage the connector can handle without failure.
Voltage ratings can be specified for AC (Alternating Current) or DC (Direct Current) systems. Our product range spans from 24V to 6000V. It is essential to ensure that the connector's rated voltage aligns with the voltage requirements of your application.
7. Environmental and Temperature Range
It is essential to assess the IP rating (Ingress Protection) of the connector, which indicates its level of protection against dust and water, along with its ability to withstand temperature and other environmental factors. For connectors used in extreme conditions, such as high temperatures or heavy vibrations, ensure that the connector has an appropriate IP rating and environmental sealing features.
In harsh environments, such as medical or food processing applications, it is particularly important to select connectors with robust and hygienically safe seals to prevent breakage, contamination, or exposure to harmful substances.
8. Shielded Options (EMC)
If electromagnetic interference is a concern, opt for shielded connectors to protect both internal signals and external devices from electromagnetic disturbances. This is particularly important for data transmission in sensitive environments.
9. Wire Size / Wire Gauge
Ensure that the connector is compatible with the wire size or gauge that aligns with the current rating, especially when operating close to the maximum capacity for the connector type. This is a crucial consideration when selecting a circular electrical connector, as it directly impacts the connector's ability to handle current, voltage, and overall performance in the application.
The current rating (measured in amps per circuit) specifies the maximum current that can safely pass through the connector. It is important to ensure that the selected connector meets the power requirements of your application. This rating can be influenced by various factors, including contact material, thermal management, contact resistance, the number of contacts, and environmental conditions.
6. Rated Voltage
The rated voltage indicates the maximum voltage that a connector can safely withstand. This is one of the most critical specifications to consider when selecting a connector, as it determines the electrical insulation and breakdown voltage the connector can handle without failure.
Voltage ratings can be specified for AC (Alternating Current) or DC (Direct Current) systems. Our product range spans from 24V to 6000V. It is essential to ensure that the connector's rated voltage aligns with the voltage requirements of your application.
7. Environmental and Temperature Range
It is essential to assess the IP rating (Ingress Protection) of the connector, which indicates its level of protection against dust and water, along with its ability to withstand temperature and other environmental factors. For connectors used in extreme conditions, such as high temperatures or heavy vibrations, ensure that the connector has an appropriate IP rating and environmental sealing features.
In harsh environments, such as medical or food processing applications, it is particularly important to select connectors with robust and hygienically safe seals to prevent breakage, contamination, or exposure to harmful substances.
8. Shielded Options (EMC)
If electromagnetic interference is a concern, opt for shielded connectors to protect both internal signals and external devices from electromagnetic disturbances. This is particularly important for data transmission in sensitive environments.
9. Wire Size / Wire Gauge
Ensure that the connector is compatible with the wire size or gauge that aligns with the current rating, especially when operating close to the maximum capacity for the connector type. This is a crucial consideration when selecting a circular electrical connector, as it directly impacts the connector's ability to handle current, voltage, and overall performance in the application.
- Choosing the correct wire size is vital to prevent issues such as overheating, voltage drops, and other inefficiencies that could jeopardise both safety and functionality. Wire sizes are typically measured using the standard American Wire Gauge (AWG) system.
- Smaller gauge numbers indicate thicker wires capable of carrying more current. This usually applies to power connectors used in industrial machinery that require lower gauge (thicker) wires, such as 10 AWG or 16 AWG.
- Larger gauge numbers represent thinner wires that are suited for lower current applications. For signal transmission or data lines, such as in sensors, telecommunications, or medical devices, higher gauge (thinner) wires like 24 AWG or 26 AWG are often used.
10. Coding
Connectors utilise coding to ensure proper alignment and prevent mismating. It is essential that the pin and socket elements are correctly aligned before locking them into place. Proper coding is especially important in applications where mismating could lead to system failures. In this setup, the arrangement of pins and sockets is designed with a coding system that allows only specific configurations to be connected, ensuring correct mating every time.
11. Termination Type
Consider the termination method that best fits your application:
Connectors utilise coding to ensure proper alignment and prevent mismating. It is essential that the pin and socket elements are correctly aligned before locking them into place. Proper coding is especially important in applications where mismating could lead to system failures. In this setup, the arrangement of pins and sockets is designed with a coding system that allows only specific configurations to be connected, ensuring correct mating every time.
11. Termination Type
Consider the termination method that best fits your application:
- Solder: Electrical wires are connected to the pins or sockets of the connector by melting solder, resulting in a durable and reliable electrical bond. This method, however, is labour-intensive and requires specialised tools.
- Screw clamp: Wires are secured to the connector by inserting them into a clamp and fastening a screw. This approach facilitates straightforward installation and removal, making it ideal for applications requiring frequent disconnections.
- Crimping: A metal connector is mechanically crimped onto the wire, ensuring a reliable connection that is quick to install. This method is widely employed in mass production due to its efficiency and cost-effectiveness.
- IDC: Wires are inserted into the connector, where a metal blade penetrates the insulation and establishes contact with the conductor. This technique enables rapid and efficient assembly without the need to strip the wire insulation.
- Molded on cable: The connector is permanently affixed to the end of the cable during the manufacturing process. This provides a robust and error-free solution while offering enhanced protection against environmental factors.
- Wire Clamp: Wires are inserted into a spring mechanism that securely holds the wire through spring pressure. This method provides a vibration-resistant connection, enables tool-free installation, and is ideal for applications requiring reliability and ease of use.
Each termination type provides a different way to join wires or cables with the connector.
12. Space Constraints
The size and weight of the connector should be suitable for the available space. Additionally, the engagement force must be taken into account, as it affects how easily the connector can be mated or unmated, particularly in confined or hard-to-reach areas. For applications with limited space, angled connectors may provide better accessibility than straight connectors.
13. Housing and Terminal Materials
Select the connector housing material based on the specific environmental and application requirements. Common options include:
12. Space Constraints
The size and weight of the connector should be suitable for the available space. Additionally, the engagement force must be taken into account, as it affects how easily the connector can be mated or unmated, particularly in confined or hard-to-reach areas. For applications with limited space, angled connectors may provide better accessibility than straight connectors.
13. Housing and Terminal Materials
Select the connector housing material based on the specific environmental and application requirements. Common options include:
- Stainless steel: Suitable for heavy-duty applications, offering excellent strength and resistance to corrosion.
- Plastic (nylon): Lightweight and durable, making it ideal for standard applications.
- Metal: Provides enhanced robustness and durability, particularly in industrial settings.
14. Approvals and Certifications
Certain industries mandate specific certifications or approvals for connectors to ensure compliance with regulatory and safety standards, such as:
Certain industries mandate specific certifications or approvals for connectors to ensure compliance with regulatory and safety standards, such as:
- UL Rating: Required for the U.S. market, ensuring safety (regarding the flammability of the materials used) and performance.
- Ecolab or FDA Compliance: Essential for medical or food industry applications, meeting hygiene and material safety standards.