www.industryemea.com
06
'25
Written on Modified on
Industrial AI: the bottom-up revolution
High initial costs, implementation complexity, and lengthy return on investment remain: these misconceptions remain the primary barriers to artificial intelligence adoption in manufacturing.
emea.mitsubishielectric.com
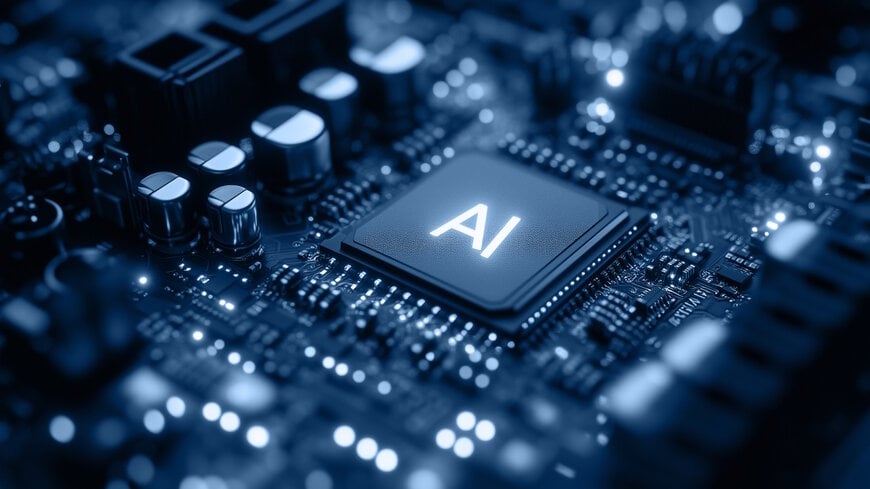
Image Caption: AI on a component level
[Source: Mitsubishi Electric Europe]
Intelligence at the component level
A significant proportion of manufacturing facility failures can be predicted through data analysis from individual components. Advanced yet effort-free analytics at the servo drive level enable self-monitoring and diagnosis of potential issues in surrounding machine parts. Frequency inverters utilize AI algorithms to diagnose the root causes of failures, while industrial robots enhance their paths in real-time, significantly boosting efficiency and improving quality.
A crucial element of this approach is the ability to respond instantly to equipment anomalies or predict them in advance. Intelligent components analyse data in real-time, enabling rapid parameter adjustment or machine shutdown before serious failures occur.
“Based on feedback from vast amounts of manufacturing facilities of all sizes we know that components equipped with AI-driven intelligence greatly reduce unplanned downtime. Such analytics happens automatically and does not require any knowledge in data science”, explains Piotr Siwek, Digital Director EMEA at Mitsubishi Electric Factory Automation.
From intelligent components to smart factory
The scalability of this approach to AI implementation significantly reduces deployment costs compared to comprehensive cloud solutions. After implementing intelligence on the component level, whole production lines can benefit from data analysis by integrating PLC control systems with AI algorithms. As factories face increasing demands for data analytics, edge-level solutions can be deployed while keeping all the factory data in-house.
A significant proportion of manufacturing facility failures can be predicted through data analysis from individual components. Advanced yet effort-free analytics at the servo drive level enable self-monitoring and diagnosis of potential issues in surrounding machine parts. Frequency inverters utilize AI algorithms to diagnose the root causes of failures, while industrial robots enhance their paths in real-time, significantly boosting efficiency and improving quality.
A crucial element of this approach is the ability to respond instantly to equipment anomalies or predict them in advance. Intelligent components analyse data in real-time, enabling rapid parameter adjustment or machine shutdown before serious failures occur.
“Based on feedback from vast amounts of manufacturing facilities of all sizes we know that components equipped with AI-driven intelligence greatly reduce unplanned downtime. Such analytics happens automatically and does not require any knowledge in data science”, explains Piotr Siwek, Digital Director EMEA at Mitsubishi Electric Factory Automation.
From intelligent components to smart factory
The scalability of this approach to AI implementation significantly reduces deployment costs compared to comprehensive cloud solutions. After implementing intelligence on the component level, whole production lines can benefit from data analysis by integrating PLC control systems with AI algorithms. As factories face increasing demands for data analytics, edge-level solutions can be deployed while keeping all the factory data in-house.
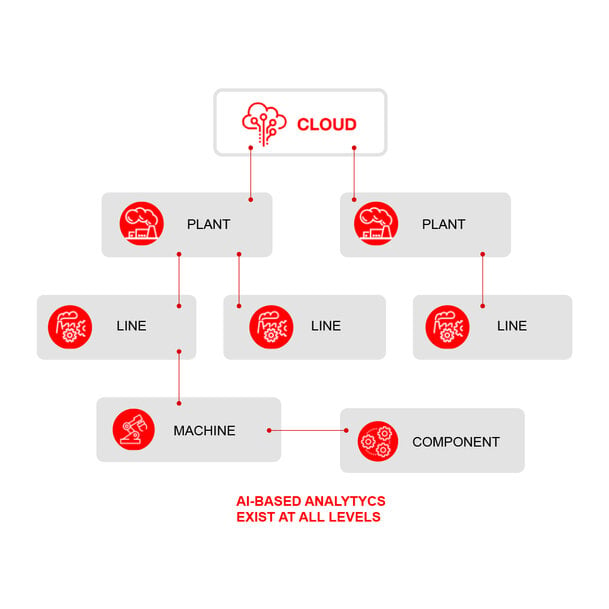
Image Caption: Levels of AI in a factory
[Source: Mitsubishi Electric Europe]
A significant advantage of this approach is enhanced data security. Local processing minimises the risk of cyber-attacks and data breaches, which is particularly crucial for manufacturing facilities working with sensitive data or technologies.
"The key to success is starting with small, measurable projects. In one European factory, we began with AI implementation in welding applications. Edge-level data analytics performed with MaiLab achieved nearly 100% accuracy of failure predictions. The quality results encouraged the client to expand the project across the entire production line", adds Siwek.
When cloud makes sense
Industry experts predict the growing importance of hybrid AI solutions, combining component-level analytics with selective cloud utilisation. Cloud solutions excel in cases requiring historical data analysis across multiple facilities or supply chain optimisation.
The cloud offers unparalleled capabilities in advanced big data analytics and machine learning on large datasets. It is particularly valuable for global organisations needing to compare and optimise processes across multiple locations simultaneously.
"The future belongs to hybrid solutions. Our bottom-up strategy allows clients to build solid digital foundations and consciously choose which processes require cloud support", summarises Siwek.
The future is scalable
The evolutionary approach to industrial AI implementation, beginning at the component level, presents a practical alternative to comprehensive cloud deployments. It enables the gradual development of digital competencies, reduces investment risk, and ensures quick returns. As both organisations and their analytical needs grow, the system can be expanded with additional layers, including selective cloud utilisation where it brings the most value.
www.mitsubishielectric.com
"The key to success is starting with small, measurable projects. In one European factory, we began with AI implementation in welding applications. Edge-level data analytics performed with MaiLab achieved nearly 100% accuracy of failure predictions. The quality results encouraged the client to expand the project across the entire production line", adds Siwek.
When cloud makes sense
Industry experts predict the growing importance of hybrid AI solutions, combining component-level analytics with selective cloud utilisation. Cloud solutions excel in cases requiring historical data analysis across multiple facilities or supply chain optimisation.
The cloud offers unparalleled capabilities in advanced big data analytics and machine learning on large datasets. It is particularly valuable for global organisations needing to compare and optimise processes across multiple locations simultaneously.
"The future belongs to hybrid solutions. Our bottom-up strategy allows clients to build solid digital foundations and consciously choose which processes require cloud support", summarises Siwek.
The future is scalable
The evolutionary approach to industrial AI implementation, beginning at the component level, presents a practical alternative to comprehensive cloud deployments. It enables the gradual development of digital competencies, reduces investment risk, and ensures quick returns. As both organisations and their analytical needs grow, the system can be expanded with additional layers, including selective cloud utilisation where it brings the most value.
www.mitsubishielectric.com