Bosch Rexroth Showcases Digitalized Fluid Technology at Hannover Messe 2025
Bosch Rexroth presents cutting-edge fluid technology innovations at the “Fluid Power 4.0” showcase, highlighting digital product twins, energy monitoring, and sustainability at Hannover Messe, Hall 5, Booth D44, from March 31 to April 4.
www.boschrexroth.com
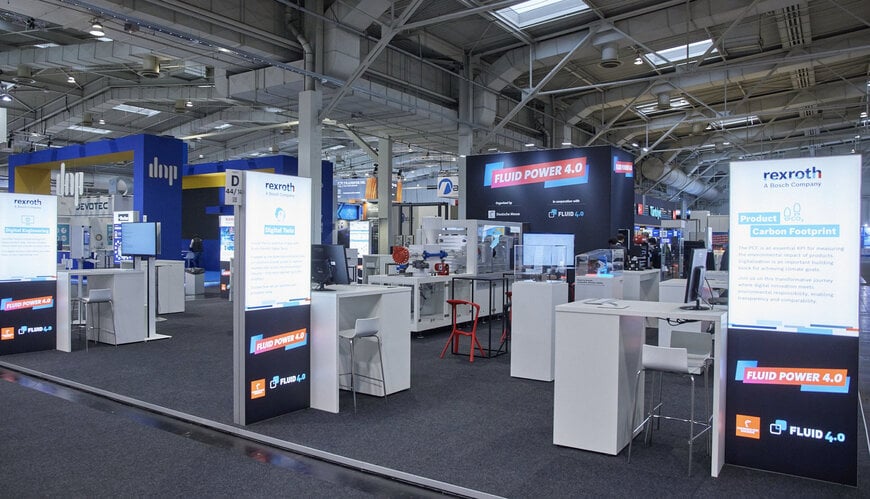
In the Fluid 4.0 research project, an industry consortium is driving forward the strengthening and further development of the administration shell as a digital twin in a cross-industry data space. The project is funded by the European Union and the Federal Ministry for Economic Affairs and Climate Action (BMWK). Building on the existing infrastructure, companies and institutions from industry and science are digitalizing practical use cases with Bosch Rexroth as coordinator. As part of the “Fluid Power 4.0” special presentation at the Hannover Messe, 16 partner companies, including Bosch Rexroth, and scientific institutions will provide insights into the digitalized and sustainable fluid technology of the future in Hall 5, Booth D44.
The work assignment of the Fluid 4.0 research project includes the development of a higher-level system instance for machine-readable data provision and cross-industry data exchange. To this end, eleven partner companies, five scientific institutions and 14 associated partners are developing partial models of the administration shells for system management. Data-based business models can be established on the basis of suitable interaction concepts and automated workflows. The initiative also provides a data room for the cross-industry exchange of information on fluid technology products and systems. The data room creates the prerequisites for data-based business models and enables an improvement in product life cycle management (PLM).
The development and implementation of four use cases for industry-relevant demonstrators is planned by mid-2026: for the control development of stationary and mobile machines, energy monitoring and the optimization of fluid technology systems, cross-industry CO2 balancing in the use phase and for a concept for the circular economy in fluid technology. The demonstrators can be used by interested parties as open test environments to test the cross-industry exchange of information on the product life cycle of fluid technology products and systems.
As part of the “Fluid Power 4.0” special presentation at the Hannover Messe, 16 partner companies and scientific institutions are presenting their development work under the leadership of the VDMA. Bosch Rexroth will be demonstrating the interaction of components and systems from different manufacturers on an injection molding machine at its booth and will be presenting the following topics:
Digital Engineering
Digital product twins accompany components throughout their entire life cycle. Machine manufacturers already use them during the planning and engineering of machines, for example to significantly reduce the time required for design or commissioning. As part of the special presentation, Bosch Rexroth will be demonstrating how digital data from hydraulic products can support and accelerate the design process.
Bosch Rexroth plans to provide all products with digital product twins in the future. The basis for this is the industry-neutral standard of the asset administration shell, which ensures cross-manufacturer interoperability and enables end-to-end value chains. Bosch Rexroth has already integrated the asset administration shell into its series products and now has over 300 million digital product twins in the field. In the new product catalog for industrial hydraulics, interested parties will find native 3D CAD models for all CAD systems and EPLAN electric data for many products in the Rexroth portfolio.
This reduces the time required to search for and insert the 3D models of the products into the respective engineering environment by up to 66 %. For factory automation products, the digital product twins also provide simulation models for virtual commissioning and service information, as well as documentation, certifications, manufacturing and order data, in particular the CO2 footprint and, in future, the digital product passport.
Digital Product Twin
Open, manufacturer-independent standards and interfaces such as the administration shell as a standardized digital twin or the graphical specification language BPMN 2.0 (Business Process Model and Notation) simplify the technical connection and orchestration of brownfield and greenfield projects. At the same time, they create greater data and process transparency across the entire life cycle of a machine or system. With the Asset Orchestration Platform software solution, machine manufacturers also simplify virtual and real commissioning and reduce downtimes. The interaction of components and systems from various project partners will be demonstrated in an injection molding machine at the trade fair stand. Visitors to the trade fair will learn, for example, how production can be converted easily and without programming effort.
Injection molding machine application example
Using the injection molding machine as an example, Bosch Rexroth will also be presenting its energy monitoring and management. The company will show how access to energy data can be simplified and how standardization contributes to greater transparency in energy data. New hardware solutions, such as an innovative sensor that allows the oil status to be determined precisely, optimize the use of resources and can be integrated into a proactive maintenance strategy.
Product Carbon Footprint (PCF)
The product carbon footprint comprises the total greenhouse gas emissions caused by a product in the various phases of its life cycle. In the future, the calculation of real CO2 emissions in the use phase of hydraulic products and the inclusion of the characteristic values in the product catalog will take place. There are also plans to define new standards in this area. This will enable machine manufacturers to add up the PCF values of all products and provide their customers with the PCF of the entire machine.
Circular Economy
The aim of the circular economy is to use existing materials and resources as long and efficiently as possible, for example by repairing or recycling them. In future, new data models will help companies to implement a circular economy strategy along the entire product life cycle - from development to disposal. In addition, use cases are to be identified that enable specific business models and can be implemented as examples. At the trade fair stand, visitors will learn how digital data can be used to increase the sustainability of machines and systems.
The Fluid 4.0 research project will be presented at the Hannover Messe in the large special presentation “Fluid Power 4.0” in Hall 5, Booth D44. From 31 March to 4 April, the Motion & Drives Stage in Hall 5, Booth D32 will also feature presentations on the topic of digitalized fluid technology as well as a VIP Hydraulics Live Talk with keynotes and a panel discussion on 2 April from 10:00 to 12:30.
www.boschrexroth.com