www.industryemea.com
12
'25
Written on Modified on
Laser cutting and welding in one HIWIN and LASERVORM realize real heavyweights
LASERVORM delivered a seven-ton tandem laser machine for cutting and welding in a gantry system, featuring HIWIN drive technology—despite its extraordinary dimensions.
www.hiwin.com
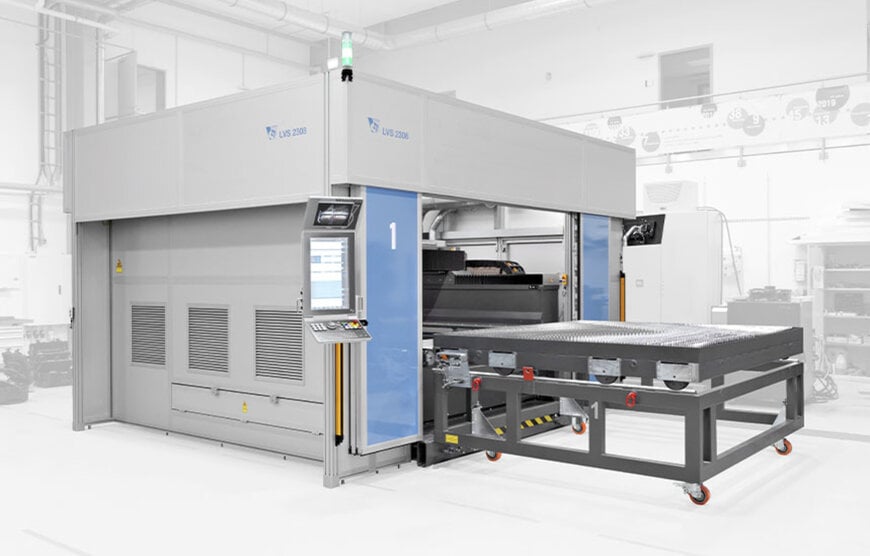
Laser machine construction, laser job order production and laser machine servicing specializing in the processes of laser welding, laser hardening and laser deposition welding – a wide range of services offered by the medium-sized family company LASERVORM GmbH from Altmittweida in Saxony. “In our in-house contract manufacturing, we process everything from single pieces to large series,” says Thomas Kimme, Managing Director of LASERVORM GmbH. ‘Thanks to our expertise, it makes sense to design and manufacture machines in this range ourselves.’ The recently realized, customer-specific special solution is used by a company that manufactures components for renewable energies.
“We have completely redesigned the XYZ system, which is very compact for its tasks,” reports David Müller, design engineer at LASERVORM GmbH. ”The combination of laser welding and laser cutting in one machine is not an everyday occurrence. After all, the two processes have quite different requirements.”
The biggest challenge was combining the two processes in a single machine and in a working area of two by two meters. The solution: a combined laser welding and cutting system in a gantry design with a pallet changing system. Chain drives with cams and outriggers ensure that the pallet tables are moved alternately from the outside into the machine and back.
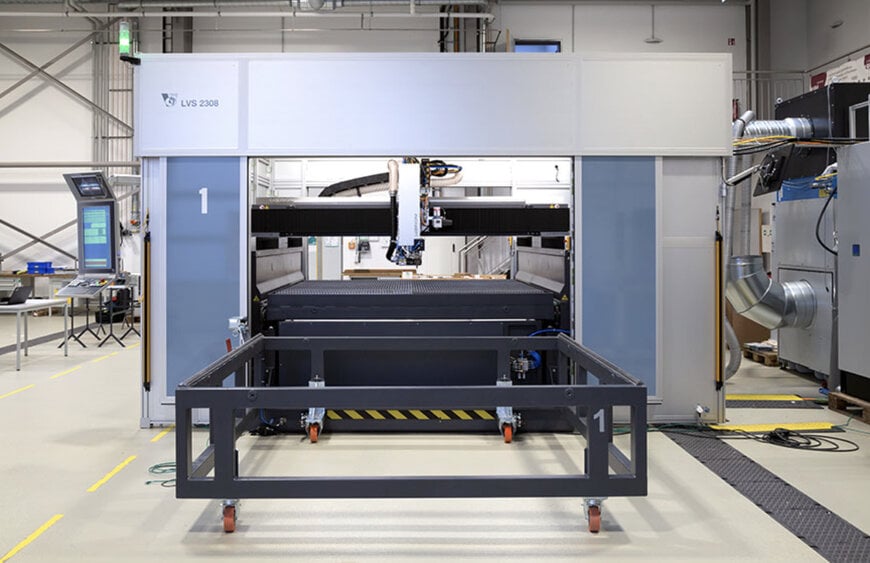
HIWIN as the number one point of contact
The gantry system is made up of an X-axis, two parallel synchronized Y-axes and a Z-axis. The portal beam in steel construction is manufactured in a complex and rigid sheet metal construction to ensure the high dynamic response that is essential for this application.
Guides and linear motors from HIWIN GmbH are used in the X and Y axes. The Z-axis is also equipped with linear guideways and a ballscrew from the Offenburg-based motion technology specialist. “For more than 20 years, HIWIN has been our partner of choice when it comes to guides,” says Thomas Kimme.
HIWIN linear guides from the HG, QHH and WEW series were installed. “The ball guide HG is the first choice for rail pairs, as we find them in this application,” reports the responsible HIWIN field representative. “With our SynchMotion™ technology, our HG series becomes the QH linear guide.” The technology allows for higher processing speeds, longer relubrication intervals, and improved synchronous performance with lower operating noise. Three blocks are mounted on each of the Y-axes to optimally distribute the emerging mass and the enormous tensile forces of the drives on the guide. HIWIN WEW guides are used for the pallet retractions and to close the machine doors completely. “The extremely wide ball guide enables the highest moment loads, especially in the Mx direction, thanks to its rail width and low overall height,” says the HIWIN sales representative, explaining the use of the series installed.
Linear motors from the LMFA series are installed in the parallel Y-axes to maintain high acceleration and precision. “We decided on an individual axis design for individual linear motor components,” explains David Müller. “We use water-cooled linear motors, but we use them with convection cooling. We can achieve the required peak forces at this point with the powerful LMFA motors.” The built-in direct drives also achieve significantly better precision compared to a purely mechanical component, which is why LASERVORM decided to use synchronous linear motors here. “The sizing of the motors was done in close coordination with the application engineers from HIWIN. We rely on the expertise of HIWIN here,” says David Müller, looking back on the smooth project phase.
Among other things, the installation site of the portal machine, with temperature differences of up to 20°C, had to be taken into account during the design. LASERVORM and HIWIN have therefore integrated a length compensation system, which should be considered in the event of thermal expansion. “We are working here with a typical fixed/supported bearing method,” explains the HIWIN field representative. “We are very grateful for the consistently competent exchange with HIWIN,” acknowledges LASERVORM designer David Müller. ‘And the short delivery times, along with the top-notch service, are a major advantage that HIWIN offers as a supplier,’ adds LASERVORM's Managing Director Thomas Kimme. ”We have experienced this differently in our company history. In special machine construction, such services are of absolute importance.”
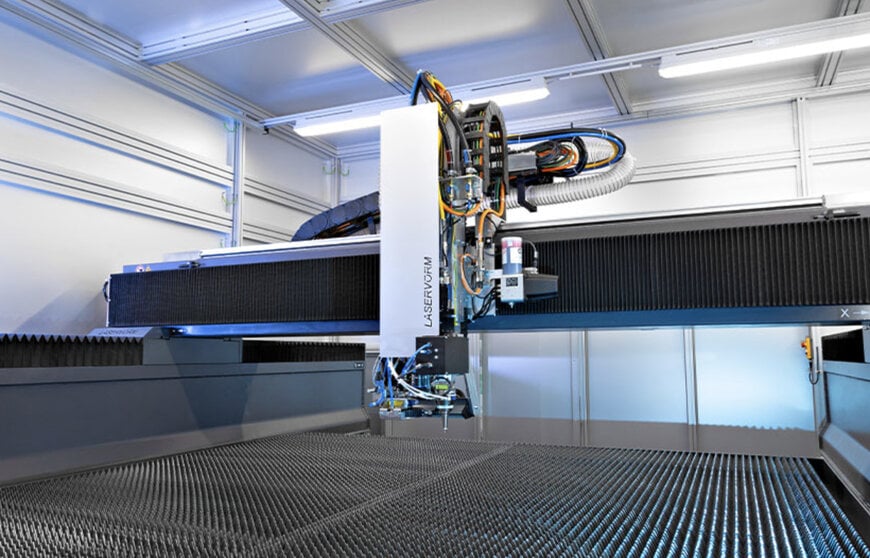
Special machines from A to Z
Always prepared for special cases, the laser machine manufacturer is also continuously expanding its expertise in laser and optical concepts. “Combining laser welding and laser cutting was challenging, especially in an optical design,” says designer Müller.
“We configured and designed laser components that we bought in-house.” This resulted in two different laser optics with different focal point positions for the portal machine. An additional focus adjustment along the Z-axis (focus shifter) makes the focal point of the optics variable. A beam switch developed in-house switches the laser light between the two beam paths.
A specially developed LASERVORM spinscan technique is used for the welding optics: it enables two-dimensional deflection of the beam and simultaneous power modulation, which, for example, can bridge large gaps during the joining process. “The built-in combination of spinscan and focusshifter offers outstanding technological freedom for welding applications,” says David Müller. It opens up a lot of possibilities for demanding joining processes with small contact surfaces and high gap dimensions, and contributes significantly to a uniform and stable connection.
Miniature guides from HIWIN are also used in the beam switch: “With our MG series, some of which are no larger than a paperclip, we have installed our miniature guide here to position the switch precisely and with high repetition accuracy,” adds HIWIN's sales representative to David Müller's explanations. In addition, LASERVORM also develops and programs the control software for its systems itself: “We use a central control system to ensure that our systems work together in sync. Just like a good orchestra,” says Thomas Kimme, adding to the laser specialist's expertise.
In addition to the very successful stroke/length ratio of this machine – especially the Y-axis (2120/3000) – and the compatibility of the two processes, laser cutting and welding, the integrated large-volume extraction system is also worthy of mention. “Here, the requirements for the purity of the filtered exhaust gases, which are contaminated with particles hazardous to health, are particularly high,” reports David Müller. ”We now have an extraction capacity of 10,000 cubic meters per hour here. That's quite something.”
A real heavyweight in a new dimension, that LASERVORM GmbH has set up here together with the drive technology specialist HIWIN. Both companies have been in business for over 30 years and can look back on a long and successful cooperation. “This was certainly not the last major project that we have realized together,” says Thomas Kimme with a wink.
www.hiwin.com