www.industryemea.com
20
'20
Written on Modified on
Instant High-Precision Measurement System Slashes Final Inspection Failures and Pays for Itself in Months
Based in Glenrothes, Scotland, Euro Precision is a medium-sized precision engineering company that over recent years has experienced a period of substantial growth. As a leading subcontract engineering company, manufacturing critical precision components and assemblies to exacting quality standards, Euro Precision now has customers in a range of industry sectors, including aerospace, medical, oil & gas and automotive.
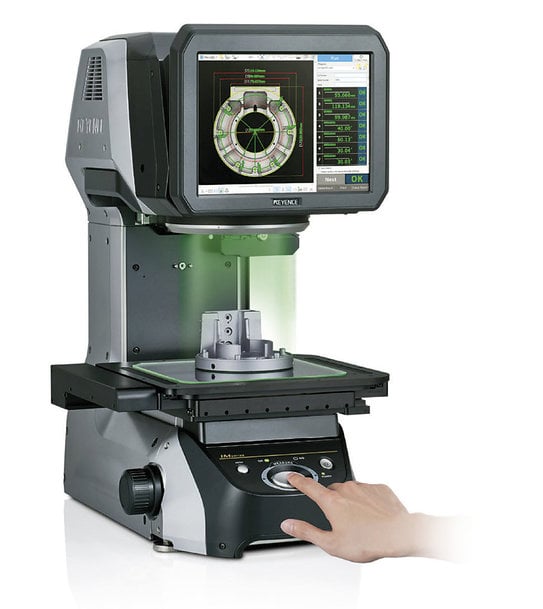
Most of the company’s products are made in medium-sized batches and repeat batches and recently it was tasked with producing a large number of components for a tier 1 German automotive manufacturer and for the Joint Strike Fighter (JSF) project. Orders such as these have helped to boost Euro Precision’s reputation over the last couple of years, as has the company’s ability to offer a one-stop-shop service for most of its clients and produce parts from start to finish. This includes assembly, testing, coating/painting and distributing via a trusted long-term supply chain.

Over the same period, Euro Precision has worked hard at reducing any technical issues that might be affecting its levels of efficiency and productivity. It has achieved this through a programme of continued growth and putting investment back into the business as well as promoting continuous improvement across the organisation and moving towards a lean manufacturing environment. In particular, the company has been eager to minimise the number of failures that might occur in large batches by taking action against faults at final inspection that at one point were sitting at 9.2%.
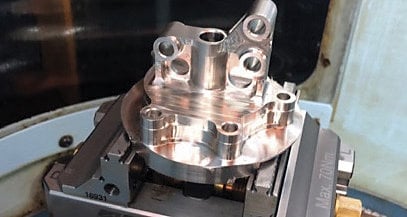
The solution
To achieve these goals, Euro Precision created a team of specialists that looked at the issues, with the task of clearly identifying any problems and coming up with corrective actions. As a result, the company invested heavily in highly advanced equipment such as CNC milling centres, a CNC Mitutoyo co-ordinate measuring machine (CMM), a laser marker and an IM-7500 Image Dimension Measurement System from Keyence. Within a short timeframe, final inspection failures were slashed to just 0.8%.
Key to this success were the two pieces of measurement equipment that were installed. The CMM provided the ability to write complex offline programs straight from the CAD model before a job began, which reduced inspection times while increasing the accuracy of an inspection.
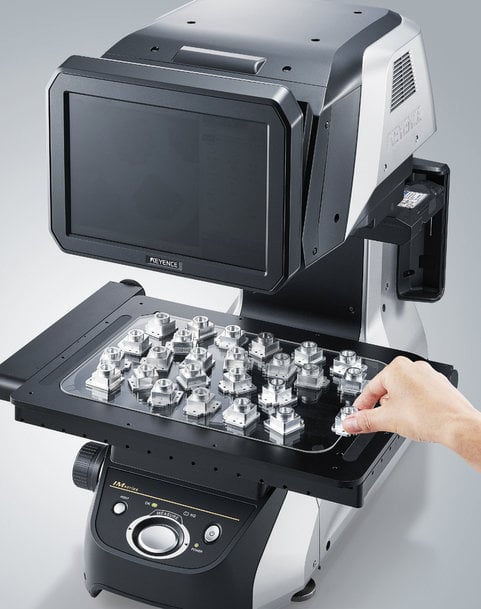
The IM-7500 Image Dimension Measurement System – Keyence’s latest addition to its Instant Measurement System series – enabled Euro Precision to check parts much quicker and with significantly greater accuracy. This has saved the company a substantial amount of money by cutting inspection times while improving the quality levels on all components. Time savings have also been achieved through the machine being straightforward to operate and program, enabling inspectors to check a higher volume of projects within much shorter timescales.
Features of the IM-7500 include an automatic measurement function that enables all settings to be completed with one click, the ability to record all measurement results and create reports automatically, and an intuitive interface that involves simply placing the part on the measurement stage and pressing the ‘Measure’ button. Significantly, no measurement expertise is needed to operate the IM-7500, with measurement points automatically identified, consistent values delivered through automatic focal adjustment, and different parts identified and measured without having to change profiles.
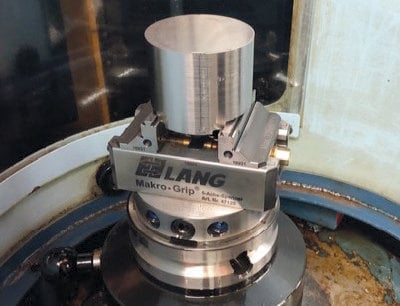
Mark Ramsay, Production Manager at Euro Precision, explains: “The Keyence IM-7500 machine has proved to be excellent for our operators because it is easy to use, extremely precise and can check parts very quickly. For these reasons we have been able to program the machine to minimise the risk of batch failures by checking more parts at a much faster pace and much more accurately.”
Mr Ramsay adds: “Selecting Keyence equipment was a new venture for us but as soon as we had the demonstration and tested a few of our parts on the IM-7500 it was a no brainer for us, we had to have that machine! The unit has more than paid for itself in just 10 months and if we could have many more of these around the workplace we would do so in a heartbeat.”
https://www.keyence.co.uk/EUROPRECISION
www.keyence.co.uk