www.industryemea.com
17
'12
Written on Modified on
Fine machining for huge windmill blades
The German machine builder, heinicke Maschinen- & Metallbau GmbH, is market leader for drilling and trimming machines to process rotor blades for wind power industry. They have chosen REDEX SRP planetary reducers because they offer better stiffness and a superior quality of service, while offering very competitive costs level.
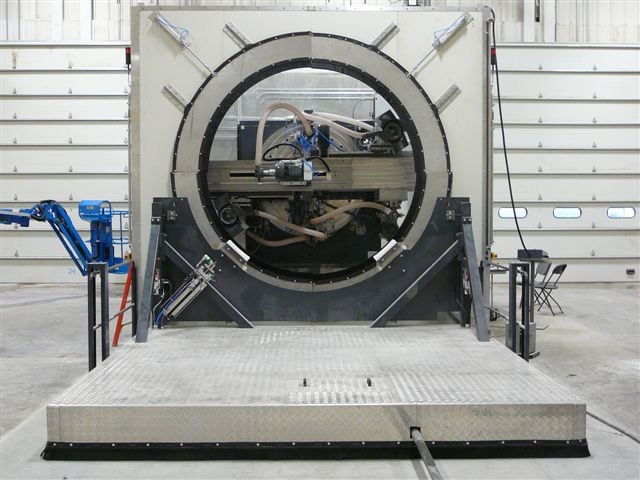
heinicke developed a machine in the 90´s named HBBA (which stands for heinicke Bohr- und Besäum-Anlage – heinicke Drilling and Trimming machine for the purpose of sawing, milling and drilling rotor blades for wind power industry.
The HBBA allows the rotor blades to be safely fixed onto the hub of the wind turbine (usually in composite material).
This solution makes difference through its flexibility, reliability, precision, and efficiency.
“We don’t really have competitors because no one is able to offer the same quality and efficiency”, explains Mr. Umlauf. “We have an enjoyable market position: more than 120 of our HBBAs are currently in operation worldwide”.
heinicke is therefore the market leader in this sector.
Rotor blade roots up to 4.3 m diameter
“Each HBBA is made according to the specific requirements and needs of our customers. For the new off-shore 6MW windmills, we have developed the HBBA 4300, which is already in successful operation at a Chinese rotor blades manufacturer. This machine is able to process rotor blade roots with a diameter of up to 4,300 mm. “
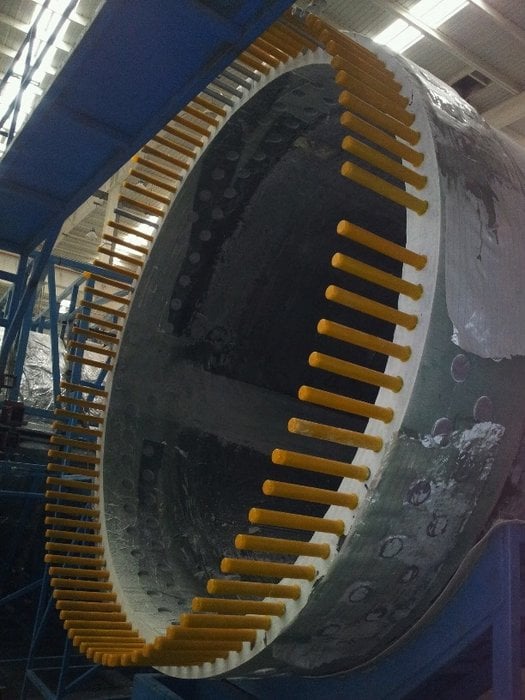
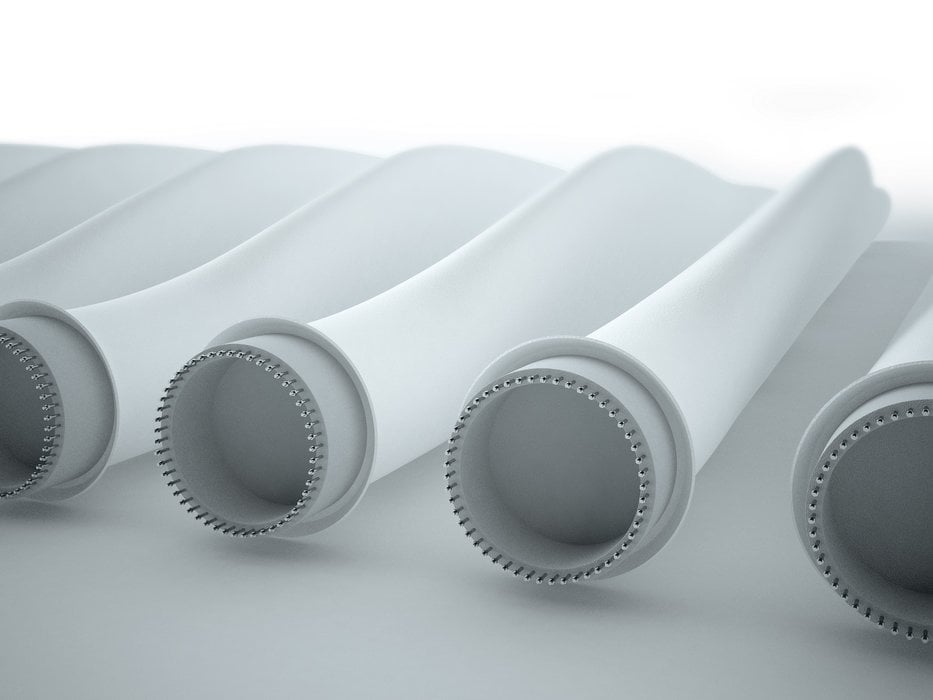
HBBA is a fully-automatic machine
A complete cycle for an onshore rotor blade lasts less than 3 hours, which means that more than two complete rotor sets can be manufactured per day.
A positioning device feeds the blade into the HBBA, and then the sawing unit performs the first step (pre-machining). At its root, the blade is shortened to exactly the planned length (trimmed). The circular saw works at a speed of 275 mm per minute and reaches a surface tolerance of max. 0.7 mm.
The shaping unit does the second step (finishing). The rotor blade which has been cut to the right length is then shaped in this step, in order to achieve an even surface. The speed is 950 mm per minute; the surface tolerance is reduced to max. 0.1 mm.
Finally, comes the drilling; the HBBA fulfills both different drilling cycles in axial and radial directions at the same time. In the axial direction (lengthways), holes are drilled for the coupling lengthways bolts with a diameter of up to 50 mm. In the radial direction (crossways), holes are drilled for the crossways bolts with a diameter of up to 90 mm.
SRP, by REDEX
This accurate movement relies on a crown and pinion drive system equipped with two REDEX SRP planetary reducers, electrically preloaded in order to offer a 100% backlash free solution.
Quality, accuracy, stiffness
“Quality is a key value for heinicke Maschinen- & Metallbau GmbH; the first HBBA prototype from the 90’s is still in operation. Most of our HBBAs have to run cleanly and without any problem in permanent 24-hour operation. In this context, we need maximum quality for each component”, adds Mr Umlauf.
“We wanted to try the SRP not only because it was an affordable technology for such an accurate axis drive system, but also because we realized that the equipment was fulfilling all our quality requirements while offering a better stiffness and higher torque. Stiffness is a key point for us because of the 6 tons which are moved by the drive. Two SRPs are mounted on the crown to cancel crown and pinion natural backlash, and their accuracy is excellent. (0,008 º) ”
Service
“Service is also a key factor. First of all, the lead time offered by REDEX was much shorter and we got all the engineering support we needed locally in Germany”. For instance, a most accurate service on sizing issues obviously helps to optimize the cost/performance ratio.
“We’re involved in market new development: it is becoming more international, and the number of windmill blade manufacturers is growing. In addition, the performance levels of wind turbines are continually increasing. The cost and service levels offered by REDEX are a key advantage for new markets”.
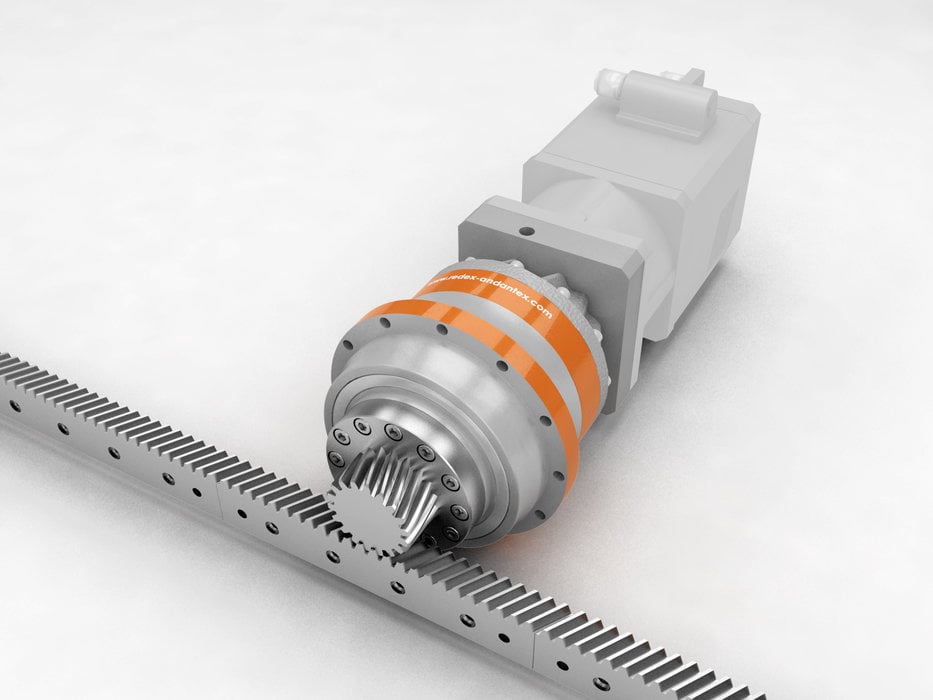
SRP is a whole range of planetary gearheads perfectly suited for the design of axis drive on the most demanding machines. It features high technology, including an exclusive output oversized tapered bearings assembly which offers superior compound stiffness.
A ready-to-use universal range of motor interface (flange and shaft adapter) enables full versatility.