www.industryemea.com
08
'20
Written on Modified on
Ramping Up Supply Chain Automation
Five Tips for Avoiding the Common Pitfalls.
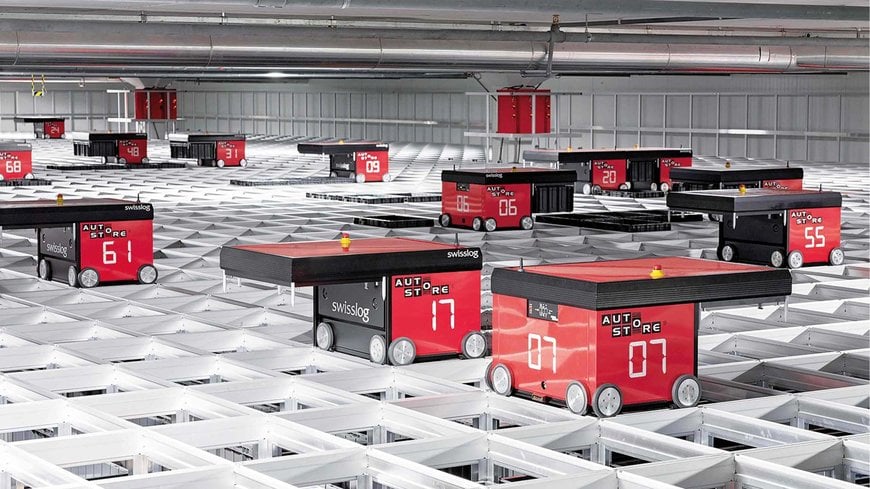
It’s natural to think that the “Go Live” of a new automation system marks the end of the implementation process. But that’s not necessarily the case. The companies that experience the most benefit from their automation are the ones that have a solid Ramp-Up plan in place long before the Go Live event occurs.
Go Live is generally considered the day when the automation completes its testing and the company begins fulfilling orders with the automation, even if it’s just a few orders a day. Ramp Up is the period following Go Live where the automation goes from a few orders to the designed production volumes.
The first couple of weeks after the Go Live, when employees are still being trained and the system is ramping up to the production volumes used to justify the capital expenditure is an important, but often overlooked, extension of the implementation process. Just as failing to properly break in the engine on a new car can lead to mechanical problems later in the vehicle’s life, not paying enough attention to the Ramp-up phase of an automation system can compromise the ability to achieve the projected ROI.
Based on Swisslog’s experience with more than 170 AutoStore implementations, as well as other material handling technology implementations, here are five tips for a smooth and effective system Ramp-up.
1- Integrate Ramp-up Into Your Installation Plan
The most effective Ramp-up plans are those that are fully integrated into the installation plan. Don’t fall into the trap of considering installation complete at startup. Include Ramp-up in your installation roadmap and timeline as a phase of the project and do not show the project as complete until the Ramp-up is complete and the system is operating at production volume. Conditioning stakeholders from the beginning that the Ramp-up is a continuation of the installation reduces the pressure to shorten or skip the process.
2-Follow the Plan
Even with good plans in place, it’s easy to get impatient and rush the Ramp-up process. After all, your organization has made a significant investment and spent long hours planning and managing the installation with your integration partner. Your organization wants to see a return on that investment as quickly as possible and may pressure the operations team to take short cuts and “get product out.” This can result in workarounds, bad habits, and confusion among staff who have been trained one way and then told to operate another. Stay disciplined and include contingencies in your plan to meet organizational objectives without jeopardizing the Ramp-up plan.
For example, if the hypothetical “end-of-month push” lands in the middle of your Ramp-Up schedule, allow time in your detailed plan to focus on meeting end-of-month goals, with the intent of getting back to the Ramp-Up the following week. This will alleviate the confusion and ensure everyone understands the need for the short-term pivot in the Ramp-Up process.
3- Pay Attention to Personnel
Another challenge some organizations face is not paying enough attention to hiring and training staff to support the Ramp-up plan. While the business drivers behind automation often include reduced staffing levels, most automation today is designed to work with humans, not just as a replacement. Failing to ensure the proper personnel are in place and ensuring they have received the necessary training makes it extremely difficult to execute on your plan and can reduce and delay the benefits of the best automation systems.
4- Prepare for Success
One challenge some organizations don’t plan for is early success. It’s a little unusual to think of success as a challenge, but when the plan goes well in the first few weeks, the risk that the operations team will think they have everything figured out and forego the remainder of the Ramp-up plan increases.
The best Ramp-up plans account for different scenarios, including a “happy path” and a “non-happy path.” When the plan is following the “happy” path, it takes extra diligence to stay the course and complete the plan. This will ensure any non-happy path scenarios or operational gaps do not show up for the first time during a critical period, such as peak season or end of the month.
5- Choose the Right Integrator
With the Go-Live event, responsibility shifts from the automation system integrator to the automation user. But that doesn’t mean the integrator shouldn’t play an important role in the Ramp-up plan. An experienced integrator will work with you to develop your Ramp-up plan, be responsive to issues that arise during the process, and remain committed to your success throughout the Ramp-up process.
It's always a big day when an automation system goes live. But, it’s important to remember that there is one more critical phase before your project can be considered complete: a well-planned and fully executed Ramp-up process.
www.swisslog.com