www.industryemea.com
13
'21
Written on Modified on
LUXURY AUTOMOTIVE AND LIFESTYLE PRODUCT DESIGNER CALLUM INSTALLS MAKERBOT METHOD X 3D PRINTER TO PRODUCE PROTOTYPES, TOOLING AND END-USE PARTS – STARTING WITH ITS ASTON MARTIN CALLUM VANQUISH 25 BY R-REFORGED
Engineering design company, founded by iconic automotive designer Ian Callum CBE*, will use the METHOD X 3D printer to meet the growing demand for customization from premium automotive and lifestyle brands.
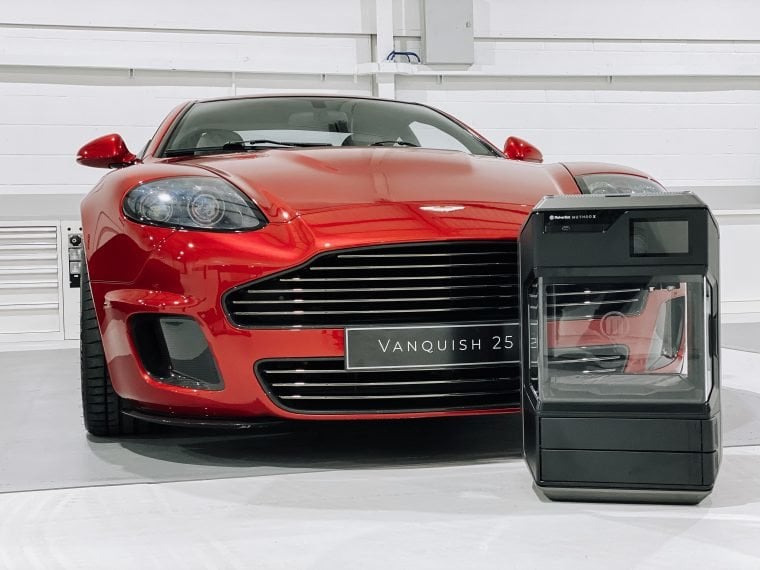
The Aston Martin CALLUM Vanquish 25 by R-Reforged will be the first in a series of bespoke and limited-edition supercars to be designed and produced using METHOD X, with other projects already in the pipeline.
MakerBot, a global leader in 3D printing and subsidiary of Stratasys Ltd. (Nasdaq: SSYS), today announced that leading automotive and lifestyle product design and engineering firm, CALLUM, has installed a METHOD X 3D printer to produce functional prototypes, tooling, and production parts across a number of luxury vehicles and lifestyle brands, including the limited edition Aston Martin CALLUM Vanquish 25 by R-Reforged.
CALLUM was founded in 2019 by renowned automotive designer Ian Callum CBE, who is responsible for some of the industry’s most recognizable and iconic car designs, including the original Aston Martin Vanquish, the Ford Puma, and 2019’s ‘World Car of the Year award winner’, the Jaguar I-PACE. True to Callum’s personal philosophy of taking inspiration from nature, art and music, the company’s mission is to design bespoke and limited-edition high-end automotive, travel and lifestyle products that combine cutting-edge design with real-world functionality. To achieve this, CALLUM has embraced a blend of the latest production techniques alongside traditional craftsmanship, including creating its own leather trim shop, which is housed in its 2,800 square metre Warwick-based facility in the UK.
From the onset, the company has been using additive manufacturing to reproduce design concepts into tactile and representative models for internal review and proof of concept. With the advanced capabilities offered by METHOD X, it is now looking to extend its application use of the technology into three key new areas. This includes fully functional prototypes for rigorous testing and simulation; tooling for limited edition componentry and gauges; and customizable, low volume production parts for final use in the vehicles and other design projects it is working on.
Adam Donfrancesco, Technical Director, CALLUM, commented: “The CALLUM engineering team has craved more additive manufacturing capabilities as the first projects enter production and METHOD X will be swiftly enrolled to support this. Having put the 3D printer through its paces, the level of part accuracy and the diversity of engineering-grade materials available is second to none versus other industrial desktop printers we’ve tested. Not only does this technology enable us to enhance our prototyping capabilities for true functional testing, but we can now also optimize the production of tools and end-use parts where 3D printing previously fell short in terms of strength, surface finish and dimensional accuracy.”
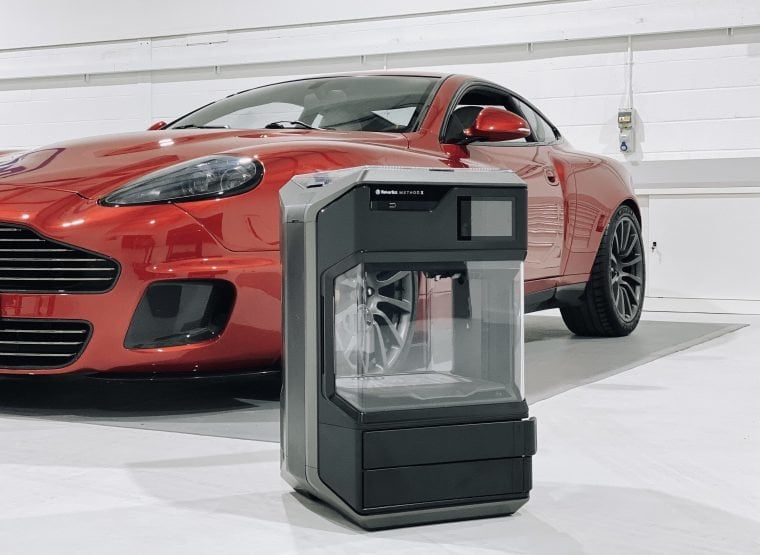
He continued: “Having direct access to industrial-grade 3D printing capability will significantly reduce both the time and cost of our design and production process. Until now, our engineers have had to rely on our basic in-house capability alongside outsourcing, a process which can take several weeks. METHOD X completely changes the game, enabling the team to print parts on demand in a matter of hours. This will not only eliminate the need for external vendors, resulting in considerable cost savings, but it will also help to accelerate production times for our vehicles by allowing us to reiterate design ideas very rapidly and take more design risks with fewer consequences.”
The company’s first public project is the Aston Martin CALLUM Vanquish 25 by R-Reforged. This reimagining of the 2000s classic will feature over 350 engineering, material and design changes, transforming the much-loved car into a more practical and relevant GT. Just 25 limited-edition vehicles will be built in Warwick and will feature several 3D-printed end-use parts, such as brake ducts, all of which will be produced using METHOD X.
Ian Callum, Design Director, CALLUM, said: “I firmly believe that you can’t determine the quality of a design on a screen or photograph. You want to be able to see and touch something in 3D and additive manufacturing enables designers to do that quickly and cost-effectively. It’s a technology that hugely excites me.
“MakerBot’s METHOD X 3D printer is our first true step into industrial-grade additive manufacturing, and we are excited to push the boundaries of automotive design and production with this technology,” he continued. “For specialist engineering and design companies such as CALLUM, versatile machines such as METHOD X offer a way to enhance craftsmanship and find new, efficient means to solve design, manufacture and production challenges. As the world looks for more personalization and bespoke products, CALLUM is now better placed to support its designers and, ultimately, its customers.”
The combination of METHOD X’s most prominent features – the enclosed heated chamber, advanced industrial-grade materials and dissolvable SR-30 support material – ensures exceptional surface finish, dimensional accuracy and precision for complex, durable parts.
Nadav Goshen, CEO of MakerBot, commented: “METHOD X’s heated enclosure and rapidly expanding materials portfolio continue to open up industrial-grade production to a much wider range of applications than ever before. Over the past couple of years, we have driven material innovation on the METHOD platform, and we are excited that the team at CALLUM will put its advanced capabilities to the test in some of the most demanding applications yet, and help accelerate the development of some truly next-generation vehicles.”
www.makerbot.com