www.industryemea.com
25
'21
Written on Modified on
Can you turn an old, listed building into a gym?
To withstand the high noise, high energy cardio activities, vibration control specialist Mason UK helped a popular fitness brand transform a Grade II listed warehouse in Covent Garden, into a fully-fledged gym equipment showroom.
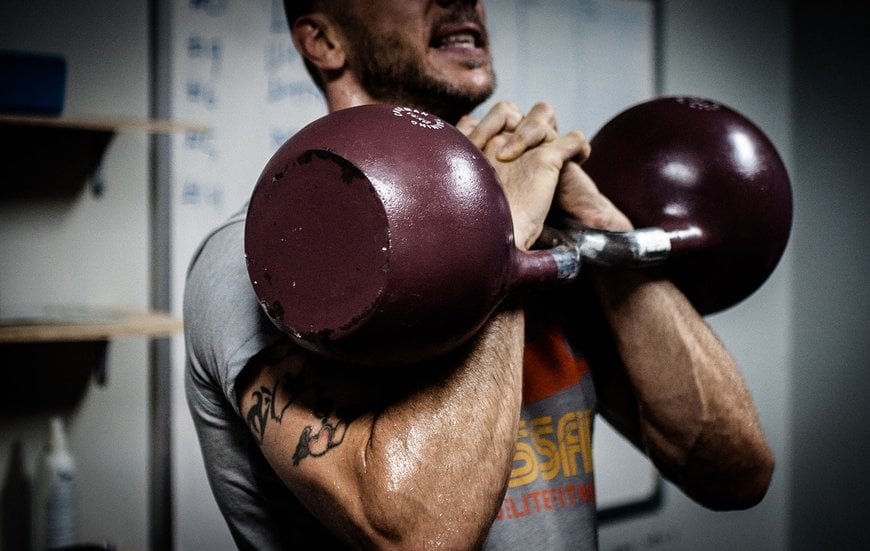
The building in question — a former Victorian seed warehouse — was never designed to be a gym equipment showroom or hold fitness classes. Today, however, customers use the building to try out attend classes and try out equipment before purchasing their at-home gym equipment. These taster sessions include high noise levels from audio equipment and high impact cardio activities such as running, jumping, and spinning frantically.
Without intervention, the noise levels and energy created by these cardio activities, would enter the building structure, disturbing other building users and adjoining properties to the Grade II listed facility. As advised by the acoustic consultant, the answer to brand’s problem was installing floating floors supporting box in box structures.
Floating floors use slabs of concrete supported by springs or rubber isolators. Should you drop a weight on a floating floor, the shuddering is not dissipated to the rest of the building, much like throwing a dumbbell on your bed wouldn’t create a loud impact — but throwing it on the floor certainly would. The secondary concrete layer also acts like concrete double glazing to attenuate audible noise.
The showroom is set in a tourist destination close to Covent Garden Piazza. The planning and commissioning for the project needed to ensure noise and vibration produced by the building did not disturb local businesses and residents. Similarly, the structural integrity of this building had to stand up against the impact associated with continuous high-energy gym classes.
Mason UK has a wealth of experience in acoustic engineering and vibration control. The company was introduced to the project by the principal contractor Knight Harwood and commissioned to undertake the design and installation of the floating floors for the three studios and a plant room on three different levels of the building.
Pedalling flooring expertise
Floating floors cannot be generic and must be tuned to suit the building and application which can easily be done with the Mason UK system. The ground floor studios posed the first structural challenge. The limited weight capacity of the existing structure, combined with the need for 200mm concrete floating floors with a sub 4Hz natural frequency, meant the spaces required an unusually large number of springs to distribute the weight of the floating floor more evenly, plus springs on this level had to be coordinated with the locations of existing structural beams.
While more springs do distribute the weight of the slab more evenly, the spring selection needed to be considered to maintain the acoustic properties of the new floors without increasing the frequency of the floors. Striking the correct balance was critical, which Mason UK achieved.
At certain locations in the studios, springs could not be located directly onto certain steel beams in the structural slab, further complicating the design. In these instances, additional steel spread plates were introduced to support the installation. For the studio on level one, the floor was constructed on a new steel frame. The Mason UK team had to carefully coordinate the design of the floating floor, to ensure the spring locations lined up perfectly with the steel beams and compensate for the way the frame itself responded to vibration.
For this floor, and all other floors, a large number of recessed boxes were also installed to accept electrical floor boxes at a later date. These are essential to accommodate the gym equipment.
Mason UK assigned two weeks to carry out these works. Due to the prime location of the building and planning restrictions, delivery time was in short supply. All deliveries and works outside the building had to be completed between 8am and 1pm, or the local council would impose costly fines. Mason UK was able to complete all deliveries and concrete pours in this allotted time.
Additional contract
Mason UK was also appointed by Roskel Contracts, the dry lining contractor working on the building. This additional contract was to provide spring hangers and sway braces for the ceilings and walls of each studio and plant room, to complete the box-in-box constructions.
Due to the complex mechanical and electrical arrangement in the ceiling void, and the numerous structural steel beams, the hanger layout for each studio had to be carefully considered for each Studio. Mason UK provided springs of multiple stiffnesses, to be installed in specific locations to ensure consistent acoustic properties across each ceiling.
“As with many of the projects we work on, this project is a prime example of a building that wasn’t built for its new purpose,” explained Steve Hart, director of Mason UK. “We had to carefully consider every spring and jack used in the floating floors using data analysis. The main challenge was a common issue we face in our line of work — floating floors need to be heavy to retain physical stability, but not all structures can withstand this weight. We got the balance right, and we are confident this building is now fit for purpose.”
The careful consideration that went into this project ensures this building will last the test of time — and weight drops.
www.mason-uk.co.uk