www.industryemea.com
11
'22
Written on Modified on
BÜHLER DIE CASTING TAKES DIGITAL SERVICES TO THE NEXT LEVEL
Bühler’s Die Casting Dashboard and Downtime Analysis services provide customers with further benefits. They can better control every aspect of their operation, leveraging instant data to boost productivity, improve processes, and drive sustainability.
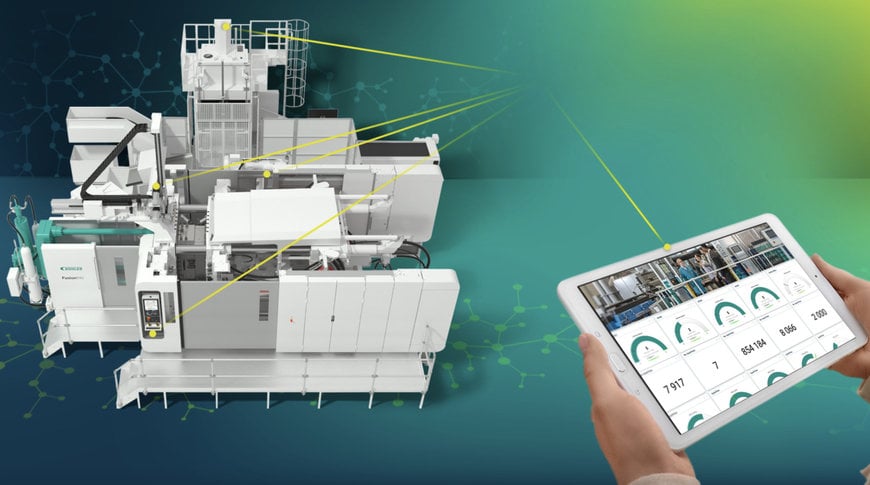
“The benefits of Industry 4.0, based on continuous, connected data, have long been talked about in die casting. Now, they are a reality for our customers,” says Cornel Mendler, Managing Director Bühler Die Casting. “Die casting is a complex manufacturing process, and we have been working hard to make sure the customer has the right information at the right time. Real-time data drives quality consistency, enables better management of energy consumption resources and overall costs, and boosts productivity.”
Bühlers digital services are available on all Bühler’s solutions: Carat, Bühler’s two-platen machine with locking forces of 10,500 to 92,000 kN, designed for die casting large and complex parts; Evolution, the proven die-casting solution for aluminum and magnesium parts, and Fusion, the next generation, three-platen die-casting platform, offering 3500 to 14,000 kN locking force.
Production activity at a glance
“We live in a world relying on interactions and cooperation. Challenges can’t be conquered alone. Thanks to these connected services, we can work with our customers to solve problems through remote support and together define a proper improvement plan,” says Oudi Zhao, Product Manager Bühler Die Casting.
With the Die Casting Dashboard, it is possible to look at individual die-casting cells in detail. Charts, curves, and Key Performance Indicators (KPIs) make it easy for the user to keep an eye on production, being able to better plan, manage and improve performance based on real data. The Die Casting Dashboard also enables the user to compare performance across die-casting machines and plants, so the production staff can quickly identify areas for improvement.
In addition, all information can be displayed centrally on any device, 24 hours, 7 days a week, giving managers comparisons between machines, shifts, die programs or facilities. This feature is powered by Bühler Insights, the central platform for connected products and services, optimizing plant’s efficiency and reducing maintenance times, energy consumption, and wastage.
Increasing operational effectiveness
Downtime Analysis is a comprehensive analysis tool of production events and provides root cause reporting from each die-casting cell. A few building blocks constitute this tool. At first glance, the cell performance can be interpreted via “uptime” and “downtime”. Additionally, the most critical downtime causes are ranked for frequency or duration. The maintenance experts and technologists can then analyze each category of technical issue and define proper counter measures. Regularly using Downtime Analysis can help customers to effectively increase uptime.
“By monitoring and analyzing real-time performance, and benchmarking across time periods, equipment and shifts, the Die Casting Dashboard and Downtime Analysis used together enable die casters to drive best practice and improve Overall Equipment Effectiveness (OEE),” says Cornel Mendler.
The Die Casting Dashboard and Downtime Analysis tools which are now available, guarantee a profitable, stable, and secure production. Framed by an individual TotalCare service agreement, the customer will have access to regular checks, updates, and full support of Bühler experts.
If you want to learn more about this and other Bühler Die Casting services, please visit Bühler’s booth 7-212 at the Euroguss 2022.
www.buhlergroup.com