www.industryemea.com
20
'22
Written on Modified on
High-voltage connectors from ODU – Treading the fine line between minimum installation space and maximum power transmission
Electronic devices will continue to become ever smaller and lighter in future. Accordingly, product developers are required to shrink the individual components to the same extent.
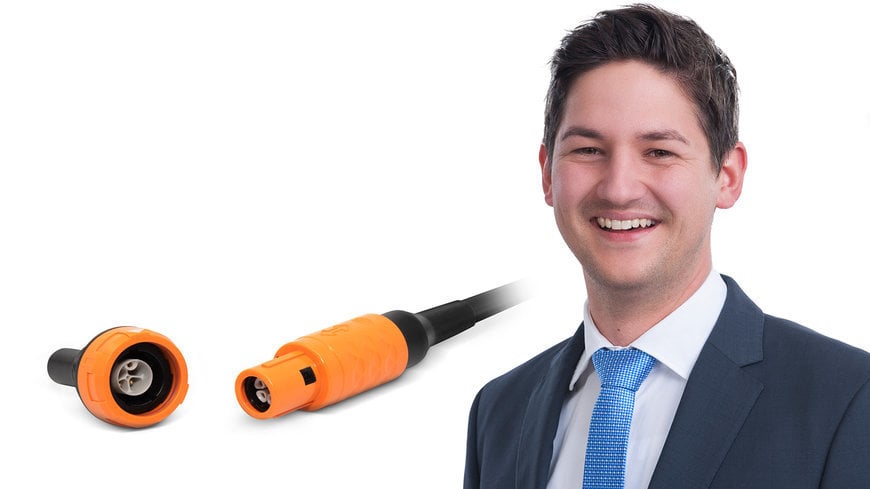
However, despite the fact that the components are shrinking, their electrical output will need to increase at a similar rate. This requires compliance with certain standards, a well thought-out design concept for all devices, and expertise in combining the smallest possible installation space with maximum power transmission – without compromising user safety.
An interview with Sebastian Dormeier (Product Manager Circular Connectors).
Are your customers already approaching you with these requirements?
Yes, this exact combination of minimum installation space and maximum power transmission is becoming increasingly important for our customers and is a must-have in most cases, regardless of the industry. I’ll gladly explain this issue using the example of one of the new products in our high-voltage range.
What kind of connectors are we talking about and what are ODU’s particular strengths?
In our plastic connector range, we have developed a new contact insert that is suitable for high voltages and ensures reliable transmission of up to 1,000 volts AC and 16 amps. All this in a connector with a diameter of 20 mm or less. In addition, we designed the contact pin layout to ensure that hot-plugging can generally be prevented in advance. We achieve this by means of lagging signal contacts, which detect the completely mated state and enable a compatible electronic system to do likewise. The transmission of current and voltage is interrupted immediately if a user attempts to plug or unplug the connector while it is under power.
This special safety aspect is very important, especially with higher voltages and currents, both for our customers and ultimately for the end users themselves. It also ensures the long-term functional and operational safety of our products. On request, we also offer this connector in orange to indicate the presence of high voltages.
You mentioned the topic of safety, which standards are particularly important in this area?
Our high-voltage connectors are designed in accordance with DIN EN IEC 60664-1. This involves insulation coordination for electrical equipment. In other words: the functional insulation of components. Since our connectors are also used in many different medical technology applications, we have also designed them in compliance with IEC 60601-1 to fully support our medical customers as well.
Which features of your connectors ensure compliance with IEC 60601-1?
To achieve the highest degree of protection for medical technology devices, we increased the clearance and creepage distances between the live contacts inside the connector and the contactable parts of the enclosure. We achieved this by inserting insulating domes around the contacts. The greater the clearance and creepage distances, the higher the protection levels. In our case, we attain the highest level, or 2 MOPP, which means “Two Means of Patient Protection” for medical devices operating on 230V AC mains.
Since our components comply with these two protection levels, and we have also selected matching cables for this purpose, the medical device manufacturers don’t need to worry about additional integration in the power supply unit. This saves them time, effort and, of course, money. This connector is used, for example, in the field of ablation catheters, where compliance with IEC 60601-1 must be ensured on the one hand, but higher currents may also flow for a few seconds.
Besides medical technology, for which other application areas were the new high-voltage inserts developed?
We have also developed our high-voltage connector for the automotive testing sector, among others, where higher voltages are typically applied. In this particular case, pollution degree 3 was also specified to meet the harsh requirements in workshops. For example, our connector is used for a battery tester in this field. In the industrial sector, too, we have developed reversed gender variants for LED video walls to ensure that the individual screens are supplied with power, for example at concerts.
Is the high-voltage connector the only one of its kind at ODU, or are there others?
In the field of circular connectors, we also offer some customized variants for higher currents and voltages for our ODU MINI-SNAP® series. The ODU-MAC® modules of the rectangular connector series offer solutions with up to 9.5kV in pollution degree 2 and standard solutions with 6.3 kV or 4 kV nominal voltage available at short notice. This can then be combined with other modules in a hybrid connector solution.
These are then connectors without switching capacity (COC) and the partial discharge voltages have been tested. In addition to the standard portfolios, we offer many customised connectors, optionally with a high-voltage cable as a complete cable assembly. Everything from a single source, always matched to minimum installation space, maximum power transmission and maximum safety.
www.odu-connectors.com