The EU Automation Five Ways to Minimize the Effects of Obsolete Parts on Production Lines
Parts auditing, risk assessment and partnering with trusted suppliers are crucial to avoiding unnecessary downtime.
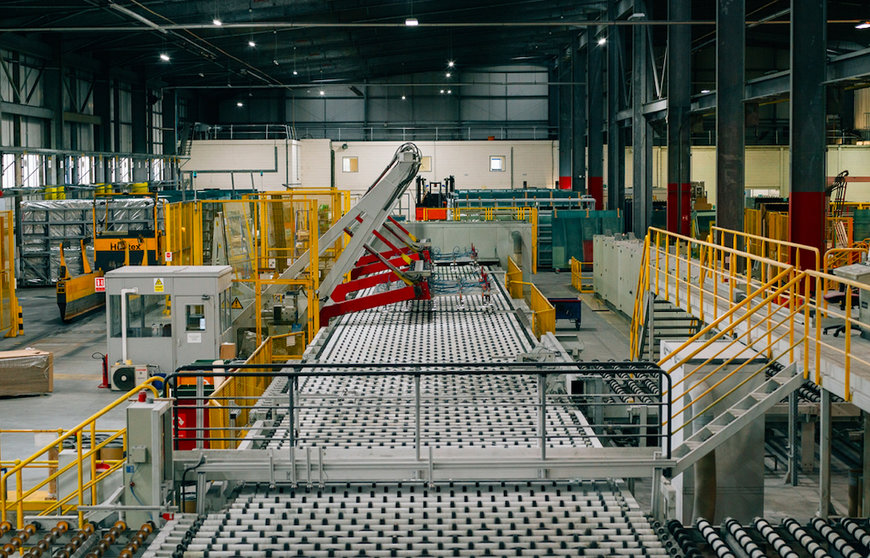
Any unexpected halt in production can be costly, quickly eating into the bottom line. For example, an average automotive manufacturer loses $22,000 per minute when a production line stops. Indeed, it is estimated that unplanned downtime costs manufacturers across all sectors up to $50 billion a year.
A significant cause of downtime is obsolete parts. A part becomes obsolete when it is no longer manufactured. This can happen for several reasons: technological evolution, market changes, environmental policies and planned obsolescence, to name but a few.
When a part breaks or starts to fail, it will need replacing. However, if the part is obsolete, it can be challenging to source original replacement components. If it is a particularly old part, the original manufacturer may no longer be in business.
Managing obsolescence can be challenging and time-consuming. For a maintenance engineer with other pressing responsibilities, it can easily fall down the list of priorities. So, EU Automation has compiled the following five-step guide for obsolescence management in industrial environments. It offers some simple actions that maintenance engineers can take to minimise the impact of parts obsolescence on production.
1. Action an initial system audit
To plan effectively, it is essential to be fully aware of the existing systems in the plant. An initial system audit will provide this information. Critical questions to ask include:
- How old is the machinery? If it is new, then it will be less likely to be obsolete soon, compared to a motor, for example, that has been in place and operating for 25 years.
- How long have the components used in the system been on the market? If the parts have been available for a long time, then there is a risk they will become obsolete soon.
- Are any components already outdated? Are there software upgrades available? Upgrading systems promptly as required will ensure that the parts remain current and up to date.
The audit results can be used to map out and make visible the life expectancy and maintenance interventions required, as well as highlighting components where alternative suppliers will be required in the short, medium and long term.
2. Perform a risk assessment
Using the audit results, the next step is to prioritise need. A risk assessment can identify the most critical applications in the system, as they will have the most significant impact in the event of failure.
Create a risk assessment form analysing the likelihood of parts breaking down and the effect this would have on the overall system. Factors to consider include:
- What is the component’s average lifetime?
- Does the system have moving parts, and how worn are they?
- What is the availability from suppliers?
- How quickly can a spare part be delivered?
- How long will it then take to fit, test and return the system to full production?
- Is the potential for part failure an acceptable risk, or is preventative maintenance the best option?
3. Develop a detailed parts list
Make a list of all the parts in the systems involved, beginning with the most critical in terms of risk of downtime. Put the obsolete parts first, as these will be the most challenging to source. This activity enables plans to be made for a quick replacement of these parts should failure occur.
Next, dig a bit deeper. Consider which parts are likely to become obsolete soon, so you are prepared for when these inevitably fail too. Think about purchasing extra spares of these parts to avoid having to undertake complete system re-designs.
4. Investigate alternative supply routes
By now, you know which of your systems are most at risk of parts obsolescence and which specific parts present the most immediate problems as regards repair or replacement. Now it is time to investigate what alternative supply routes might be available. Considerations at this stage would include:
- Is the OEM still in business and what support can they offer regarding obsolescence?
- Are alternative but equivalent quality parts available elsewhere?
- Are replacement parts available ‘off-the-shelf’ or do they require bespoke manufacture?
- If a different supplier is involved, do you need to put a service agreement in place?
- What other resources can be called on quickly to minimise downtime if a critical part breaks down?
5. Secure and simplify the supply chain
This is where working with trusted partners such as EU Automation can pay dividends. Partnering with expert industrial automation parts suppliers means maintenance engineers can be safe in the knowledge that when an obsolete part does break down, they can access replacement stock quickly to get production back up and running with minimal downtime.
Our specialists are contactable through our website, email, live chat or phone, and can offer ‘follow the sun’ support, with multiple locations and languages spoken. And we stock thousands of automation and control components from leading OEMs, all accessible from a single place. If it is not in stock or has become difficult to find, our team will scour the globe to locate the part you need. This service can be invaluable for busy maintenance engineers who lack time to ring around to find obsolete parts and compare prices and delivery times.
Review, fix, update, repeat
So, those are the five key recommendations. But it is important to remember that obsolescence management is a long-term investment requiring continuous monitoring and daily checks. There is no quick-fix solution, and it cannot be achieved effectively by simply spending one day every six months reviewing processes.
However, the process can be much easier with a well-kept maintenance database that is up to date. This approach will minimise the risk of unforeseen events, and future predictions can be made.
Conclusion
In short, the key to avoiding obsolete parts is understanding all aspects of the system and the risks involved in components becoming obsolete. Furthermore, early identification of obsolescence risk enables a broader range of options to be considered and reduces the actual cost of resolution.
Maintenance managers and engineers can keep their industrial processes running efficiently by implementing an obsolescence strategy and following a few simple steps. Maintaining good relationships with an automation parts supplier can help to protect industrial systems and goes a long way towards minimising costly downtime. It is vital to partner with a long-term, trusted, single-source partner who can get access to the right parts, at the right price, anywhere in the world. By following this formula, you can become a factory hero and keep your production line running.
For further reading on the topic, go to www.bookofobsolescencemanagement.com to download the ‘Book of Obsolescence Management’.
www.euautomation.com