www.industryemea.com
27
'23
Written on Modified on
Cultivation of biomass on an industrial scale
Festo presents the BionicCellFactory as a tool for the biological transformation towards a circular economy.
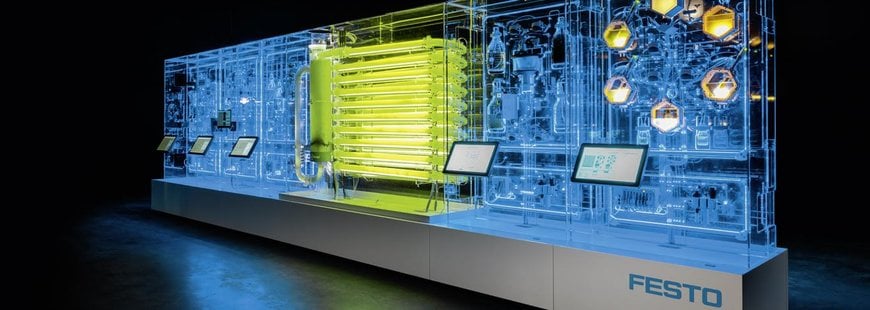
At the Hannover Messe 2023, Festo is presenting the next step on the road to the industrialisation of biological transformation: BionicCellFactory. With automation technology from Festo, biomass can be cultivated on a large scale in a highly efficient, resource-conserving way. Everything that we currently produce from crude oil creating immense CO2 emissions can also be obtained sustainably from algae. With the BionicCellFactory, Festo is demonstrating a holistic bioprocess – from the optimised cultivation of the algae with continuous monitoring and analysis through to harvesting and the further processing and refinement of the various components. The biomass obtained can be used in the chemical, food or pharmaceutical industries.
Climate and resource protection are two of the great challenges of our time. How can we extract CO2 from the atmosphere and actively contribute to climate protection? How can we reduce our material consumption, recycle more materials and at the same time access alternative raw materials? At Festo, we have been dealing with these questions for some time and are breaking new ground: ‘We are transfer our expertise of automation technology to biological processes. Here, too, nature is our great paragon. It teaches us about resource efficiency, because in nature there is no waste or wastage. We scale and accelerate solutions from the laboratory format and bring them to industrial application through the interplay of biological and technical processes,’ explains Dr Elias Knubben, Vice President Corporate Research and Innovation.
The cell as a factory
Living cells are the smallest factories in the world. Algae’s chloroplast cells photosynthesise to convert sunlight, carbon dioxide and water into oxygen and chemical energy sources – or valuable organic matter.
Optimised growth conditions thanks to automation
With our automation technology, biomass can be cultivated in a closed cycle in a highly efficient, resource-saving way and on a large scale. Everything that we currently produce from crude oil creating immense CO2 emissions can also be obtained sustainably from algae. They are small planet protectors because they absorb ten times more CO2 than land plants. This value can be increased by a factor of ten through automated cultivation in bioreactors. The biomass obtained can be used in the chemical, food or pharmaceutical industries.
Holistic process all the way up to harvesting and refinement
With the PhotoBionicCell project, Festo presented its first bioreactor for the automated cultivation of algae in 2022. This year, the interdisciplinary bionics team is going even further. With the BionicCellFactory, it is demonstrating a holistic bioprocess – from the optimised cultivation of the algae on a large scale with continuous monitoring and analysis through to harvesting and the further processing and refinement of the various components. In contrast to chemical processes, without high temperatures, high pressures and toxins.
Production systems of the future
As a model factory, the BionicCellFactory is the universal blueprint for holistic production systems of the future. With the help of the Festo automation technology, it can be scaled to any size. In order to meet future demand for renewable raw materials, bioreactors with a capacity of several thousand litres are needed. Expertise in process automation is required to ensure that the plants can reliably produce the desired quantities of biomass.
Biological transformation portfolio
Together with its customers, Festo develops intelligent control cabinet solutions for bioreactors and continues to expand its portfolio. The automation specialist ensures stable and precise process control with maximum productivity. This includes optimised fumigation and feeding strategies, control algorithms, soft sensors for real-time biomass determination, and system concepts for bio-based production processes.
Festo will also support plant operators with remote diagnostics, maintenance and control via the cloud. Robust value creation processes and easy operation of the system modules will be important if a large number of modular production units for the extraction of raw materials and carbon fixation are to be built and operated around the world in the future.
New job profiles for new technologies
However, highly qualified technical staff and biotechnologists are not available everywhere. To this end, Festo Didactic is already analysing the new knowledge requirements in order to define interdisciplinary links and establish innovative apprenticeships, degree programs and additional qualifications in the fields of biomechatronics, biointelligence and sustainability.
The BionicCellFactory is divided into five modules in which nature and technology coalesce in different ways. In doing so, the cell factory is a tool for the biological transformation moving towards an environmentally friendly circular economy.
Module 1: CO2 collection: binding CO2 from the air
Module 2: Analysis: monitoring cells using quantum sensors and AI
Module 3: Cultivation – controlled growth through automation
Module 4: Harvest: harvesting the algae using a centrifuge
Module 5: Enzymatic transformation: extraction and further processing of cell components
Control architecture: each module is controlled by a CPX-E controller from Festo. This means that the five process steps can be put into operation both in combination and separately and can be easily replaced in the event of production changes. Using dashboards on the respective control panel, experts can monitor and modify individual parameters of the process steps. Data exchange between the modules takes place via OPC UA and enables efficient control of the entire BionicCellFactory.
www.festo.com