www.industryemea.com
13
'23
Written on Modified on
EREMA is giving plastics a second life to reduce plastic waste
Recycling machines from EREMA return used plastic products to the production cycle, helping customers develop a sustainable circular economy and reduce plastic waste.
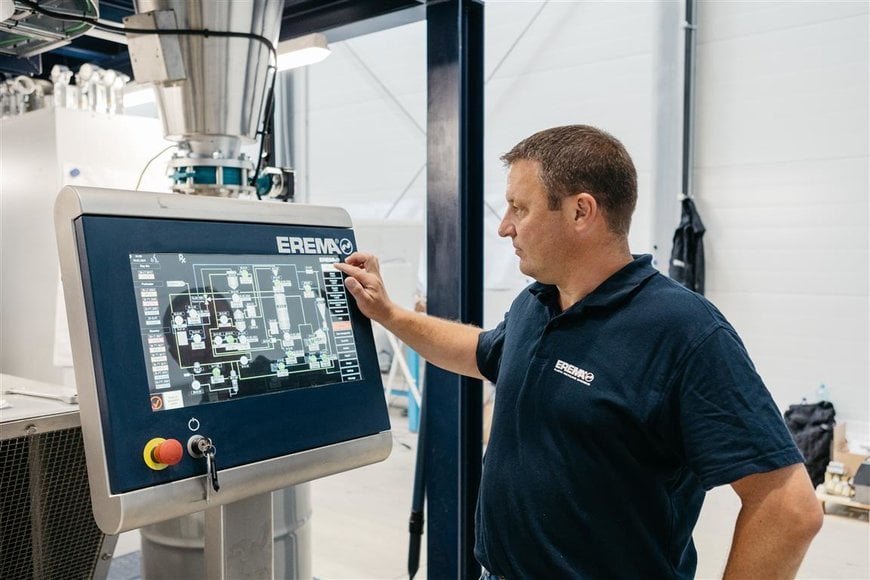
COPA-DATA’s zenon was deployed on the EREMA recycling machines to boost efficiency in engineering and operations through data visualisation and visual control. Here’s how both companies worked together.
Zero waste
Used plastic products should not end up in landfills or the oceans. Nor is thermal recycling, the downstream use of waste plastics as fuel in district heating power plants, an ideal solution. The goal must be a circular economy where used plastic products flow back into the production chain as secondary raw materials so that new products can be created.
The new products must have the same high quality as the original products from which they are made. Recycling only makes sense financially and environmentally if it saves energy, water, space, and cost. In short, recycling has to be resource efficient.
These are the objectives of EREMA Engineering Recycling Maschinen und Anlagen Ges.m.b.H. in Ansfelden, Austria. A pioneer in the industry when it was founded in 1983, EREMA is today the world leader in the development and building of plastics recycling systems for all thermoplastics, such as PE, PP, PET, PS, ABS, PA, PC, biopolymers, and compounds.
Making packaging from packaging
There are more than 6,500 EREMA systems in use around the world. EREMA customers produce more than 14 million tonnes of plastic pellets every year. Annually, they process 2.5 million tonnes of PET into food-grade rPET, which is then used to make beverage bottles and similar products. Customers value EREMA systems because of their high level of innovation, their durability and reliability, their unwavering suitability for food, their safety, and energy efficiency.
Complexity and scalability
The machines and equipment from EREMA have a modular structure so they can be combined into highly complex systems, as necessary. These range from pure material processing to turnkey solutions in which the melt is processed directly into the desired end products, such as bottles or films. EREMA uses programmable logic controllers (PLCs) from a leading European manufacturer to control the individual machines and subsystems.
"Due to their complexity, a higher-level solution is required for controlling, operating, and monitoring the entire machine. In order to map the various system complexities, the solution must be easy to operate and scalable without onerous engineering effort," says EREMA automation engineer Siegfried Blaslbauer.
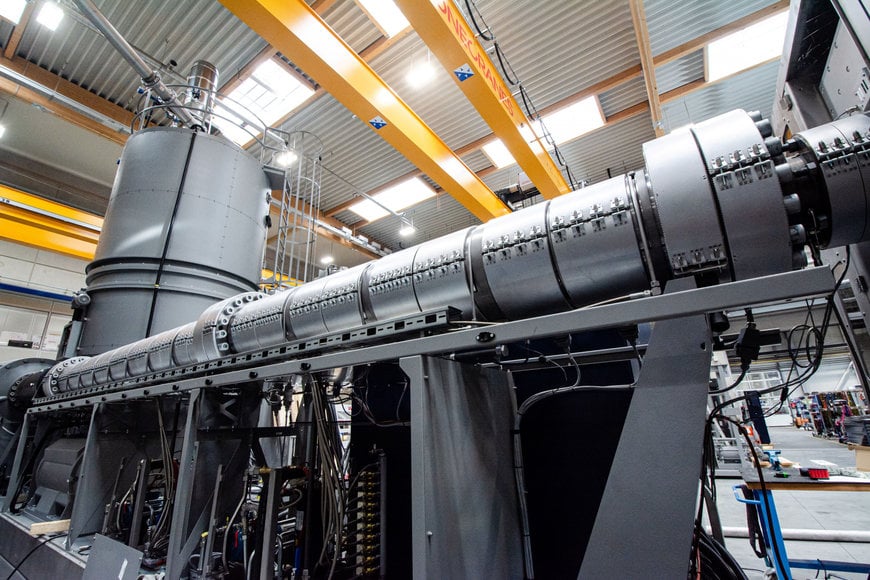
EREMA machinery in situ
Equipment visualization with zenon
EREMA began using zenon for machine visualization in 1999. At that time, zenon was not the standard solution but was offered as an option. At that time, Siegfried Blaslbauer had worked at the recycling machine manufacturer for more than a decade. He cites zenon's ability to archive production and operating data as one of the reasons for introducing the zenon software platform from COPA-DATA. Other SCADA systems could not offer the same scope, speed or quality at the time.
One system for every requirement
Thanks to zenon's ease of use, zenon very quickly became the standard for visualization on EREMA machines. Their functions have been expanded continuously. The EREMA automation engineers make use of the varied functionalities of the software platform, including batch tracking and energy monitoring.
EREMA's zenon applications have moved on from visualizing individual machines. Today, EREMA uses zenon to cover all of the visualization needs of its machines and systems. This includes comprehensive higher-level control of large, complex systems. zenon is also used to connect MES systems, for example, to integrate shift or maintenance plans.
The automation specialists at EREMA rely on zenon's automation in their engineering. They use Smart Objects found in zenon libraries for creating screens, functions, and combinations. They can be called up anywhere in a zenon project and thus reused as often as necessary. "Engineering with zenon doesn’t replace thinking, but automation with Smart Objects has saved us a lot of time with the current generation of machines," states Martin Kienbauer, head of Automation at EREMA.
Some 200 actuators and sensors are used in EREMA's latest machines, and their functions are controlled by the PLC. Automation specialists from EREMA have created a Smart Object for each of these functions.
“This ensures that the function inside the machine matches the behavior in the visualization, which enables us to exclude software incompatibilities as a potential source of an error. Our investment has been quickly repaid because zenon reduces the time and expense of testing and commissioning at site by 20 to 30 percent,” explains Martin Kienbauer.
More information on the zenon software can be found on the COPA-DATA website.
www.erema.com