Ion High-performance sensors are essential for occupational safety equipment
The following article explains how It is important to deploy reliable sensing technology to protect industrial health and safety from hazardous vapours.
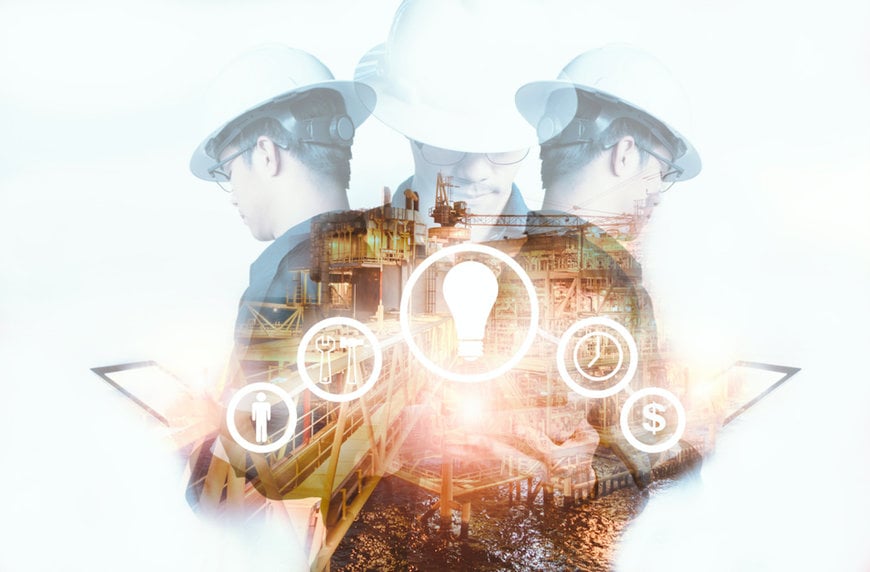
The designers and developers of gas detection instruments and systems perform a vital role in supporting organisations to fulfil their duty of care and avoid the disastrous effects of failing to protect workspaces from dangerous levels of toxic and explosive gases. Original equipment manufacturers (OEMs) help their customers to lower risk, and as such cannot utilise unproven or low-cost sensors that could increase risk. For this reason, ION Science’s mission is to provide premium quality, highly accurate sensors that are the most reliable in the world.
Risks from Volatile Organic Compounds (VOCs)
VOCs exist widely in almost every industry as key components of fuels, petrochemicals, solvents, paints, adhesives, cleaners etc. Most VOCs are flammable and potentially explosive, as well as being harmful to both health and the environment. VOCs are organic compounds that evaporate under normal conditions. Some are harmful to the skin or eyes, and can be absorbed, but their volatility means that VOCs can be inhaled, and may cause a wide variety of negative health effects ranging from minor irritation to cancer, and even death.
Generally speaking, high concentrations (% levels) are necessary for combustion or explosion risk; low concentrations (ppm) can represent a toxic risk from short-term exposure, and trace levels (ppb) can cause long-term toxic effects.
In addition to the potentially lethal effects of inadequate industrial health and safety, organisations which fail in their duty also risk huge financial losses from prosecutions, fines, and critical damage to their brands. Investments in health and safety monitoring and personal protective equipment, such as reliable gas detectors, are therefore negligible in comparison with the consequences of failure.
Workplace risk assessments should identify the presence of potential VOC sources and enable the implementation of appropriate measures to mitigate the risks. Personal, wearable VOC detectors help protect staff that have been identified as being at the greatest risk, and routine inspections with portable VOC detectors help to identify fugitive emissions. These are the unintended emissions that result from leaks or spills from equipment, tanks, pipes, seals, valves, etc. In addition, fixed VOC monitors continuously monitor workspaces to check that levels do not approach or exceed exposure limits; raising alarms if they do.
Some commonly used organic chemicals are known to cause cancer; these include methylene chloride (in paint strippers and paint sprays), and perchloroethylene (in dry cleaning fluids). In addition, benzene is a known human carcinogen, with sources including tobacco smoke, stored fuels and paints.
People at risk of benzene exposure include those working in oil refineries; chemical and petrochemical plants, including some offshore installations; coke works; foundries; and where petrol/gasoline or benzene is stored or distributed.
Benzene exposure occurs by inhalation; by absorption through skin; or by swallowing. The immediate effects of exposure to a high concentration can include tiredness, dizziness, headache and nausea. However, benzene can also cause unconsciousness and immediate risk to life at very high levels. As a carcinogen, long-term exposure to lower concentrations of benzene can result in bone marrow suppression and serious blood disorders, as well as leukaemia.
Why monitor?
Accurate, reliable measurements are necessary for the rapid detection of risks to plant and workforces. Monitoring also informs the development of mitigation measures, and allows operators to check the performance of such measures, and to demonstrate compliance with workplace exposure regulations.
Globally, health and safety regulations are relatively similar. In the UK, for example, under the Workplace (Health Safety and Welfare) Regulations 1992, employers have a legal duty to ensure, so far as is reasonably practicable, the health, safety, and welfare of employees. In addition, the Management of Health and Safety at Work Regulations 1999 require employers to assess and control risks to protect their employees. A key element of this is the requirement to comply with the COSHH (control of substances hazardous to health) Regulations. The UK’s Health & Safety Executive (HSE) says that exposure measurement is required:
- For COSHH assessment, to help select the right controls
- Where there is a serious risk to health from inhalation
- To check that exposure limits are not exceeded
- To check the performance of exposure controls
- To help select the right respiratory protection equipment
- To check exposure following a change in a process
- To show any need for health surveillance; or
- When an inspector issues an ‘Improvement Notice’ requiring monitoring
VOC Regulations
The minimum concentration of a combustible VOC necessary to support its combustion in air is defined as the Lower Explosive Limit (LEL). In the USA, OSHA advises: Atmospheres with a concentration of flammable vapours at or above 10 % of the LEL are considered hazardous when located in confined spaces. However, atmospheres with flammable vapours below 10 %t of the LEL are not necessarily safe. Such atmospheres are too lean to burn. Nevertheless, when a space contains or produces measurable flammable vapours below the 10 % LEL, it might indicate that flammable vapours are being released into the space and could present a fire or explosion hazard in time. Therefore, the cause of the vapours should be investigated and, if possible, eliminated prior to entry.
Importantly, toxic VOCs concentrations are orders of magnitude lower than explosive limits, so it is vitally important for detection equipment to offer a wide range with sufficient sensitivity to measure trace toxic gases.
The health effects of exposure to VOCs depend on the concentration, the length of exposure, and the VOCs present – because some VOCs are more toxic than others. Workplace exposure limits (WEL) therefore exist for each VOC with short-term exposure limits (STEL) typically applying to the maximum concentration over a 15-minute period, and time-weighted average levels (TWA) typically calculated over an 8-hour period.
Most countries set equal or similar WELs for each VOC, however, care should be taken to address any international differences. For example, in the USA and in most European countries, the 8-hour TWA limit for benzene is 1ppm, although lower levels have recently been proposed in Germany. Similarly, the American Conference of Governmental Industrial Hygienists has proposed a lowering of the benzene 15-minute STEL and TWA limits. Currently, the OSHA permissible exposure limit (PEL) is 1 ppm (8-hr TWA), and 5 ppm during any 15-minute work period. The NIOSH recommended airborne exposure limit (REL) is 0.1 ppm (10-hr TWA) and 1 ppm during any 15-minute work period.
Choosing the right VOC sensor technology
Gas detection equipment manufacturers have three main options for the measurement of VOCs. These are (1) electrochemical (EC) sensors, (2) metal oxide semiconductor (MOS) sensors and (3) photoionisation detection (PID) sensors.
EC sensors are low-cost, but they only respond to VOCs that are electroactive; they require electronic optimisation for target VOCs, have a slow response time (minutes) and are cross-sensitive to other gases commonly found in the workplace.
MOS sensors are also low-cost but suffer from baseline drift and humidity sensitivity. Their response is non-linear, and they also suffer from cross-sensitivity to other gases commonly found in the workplace.
PIDs are the most in-demand and appropriate sensors for the measurement of VOCs for health and safety applications. This is because of their fast response (1-3 secs), and because they are the most selective technique to VOCs. In addition, with a choice of PID lamps it is possible to optimise the sensor for different applications, and known response factors enable quantitative analysis of specific VOCs.
For most PID sensor manufacturers, sensitivity to contamination and humidity is a major challenge, but these issues have been resolved within ION’s MiniPID sensor range. This is one of the main reasons behind ION’s position as the largest PID sensor manufacturer in the world. All MiniPID sensors have a patented design with a third electrode that nullifies potential humidity interference, delivering a stable signal from 0 – 99% RH.
The sensitivity of PID sensors is extremely important in many applications; particularly where the sensors are deployed in the measurement of trace VOCs. Recognising the importance of this feature, ION’s MiniPID range includes the most sensitive PID in the world.
Reliability is a critically important feature of sensors that lower health and safety risks. Uniquely, ION’s MiniPIDs incorporate an ASIC chip, which continuously monitors lamp and sensor performance, providing fail-safe assurance of sensor performance. The ASIC also manages the sensor to give exceptional temperature stability from -40 to +65oC.
In contrast with other PID manufacturers, ION designs, develops and manufactures 10.0, 10.6 and 11.7 eV lamps. This is crucially important for OEMs because it means that their measurement capabilities are not restricted to compounds with an ionisation energy lower than 10.6 eV, for example. So, for example, where OEMs require sensors for monitoring gases such as chlorocarbons, unsaturated fluorocarbons, formaldehyde, ethylene and methanol; ION’s unique 11.7 eV gas sensor is the ideal solution. Equally, ION’s 10.0 eV sensor is ideal for toxic aromatic compounds such as benzene.
OEMs looking for a cost-effective, efficient opportunity to test and integrate ION’s MiniPID sensors into their application are able to utilise ION’s sensor development kit (SDK), which includes a sensor PCB, an integration PCB and a gas delivery hood.
Choosing the right particulate sensors
Dust and other forms of airborne particulates represent significant risks in the workplace; both as a combustion source and a breathing hazard. Consequently, the requirement for monitoring equipment is growing rapidly alongside tightening regulations. In 2021, for example, the WHO halved its yearly average guideline limit for PM2.5 from 10 to 5 µg/m3. In the UK, under the Environment Act 2021, a maximum annual mean concentration of 10 µg/m3 by 2040 has been set as the PM2.5 target. The EU Commission has proposed a reduction in the PM2.5 target to 10 µg/m3 by 2030, and the US EPA is currently considering recommendations to lower its target from 12 to between 8 and 10 µg/m3.
Responding to this growing demand, ION has added the NextPM sensor to its portfolio following recent independent testing by AQ-SPEC at South Coast AQMD in the USA. The NextPM sensors showed strong to very strong correlations for both PM1.0 and PM2.5 with reference instruments costing several hundred times the cost of the sensors.
Thanks to its patented airflow control technology, Next-PM ensures years of maintenance-free measurements, even in highly polluted environments. The sensor also incorporates patented technology to prevent humidity effects, so these sensors are ideal for inclusion in instruments and systems that monitor industrial processes or air quality; both indoors and outdoors, even in harsh conditions.
Conclusion
The cost of designing ION’s world-class VOC and particulate sensors into OEM instruments, processes and systems is negligible in comparison with the potential costs and risks incurred by not specifying the best available technology. At ION Science we wholeheartedly support this initiative, and believe that effective systems and risk reduction rely on accurate, reliable data.
www.ionscience.com