www.industryemea.com
08
'23
Written on Modified on
Bunting and Force Engineering Design Magnetic Rollercoaster Brake
Bunting and Force Engineering collaborated to design a magnetic brake for rollercoasters, using high-power, low-weight neodymium magnets to generate the braking force needed.
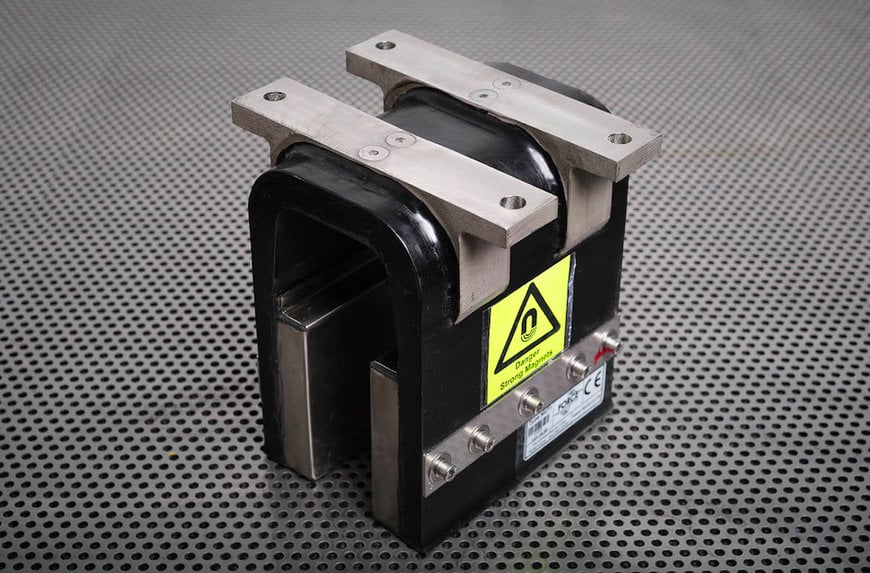
Bunting is one of the world’s leading designers and manufacturers of magnets, magnet assemblies and magnetising equipment. The Bunting European engineering and manufacturing facilities are in Berkhamsted and Redditch, both in the United Kingdom.
As a leading supplier and designer of magnets and magnetic assemblies, Bunting works with companies from a diverse range of industries. These include audio devices for medical applications, magnet assemblies for sensors, and industrial magnetisers for world-leading automotive companies. Many projects involve design collaboration.
Force Engineering is a company with a global scope, dedicated to the development, design and production of Linear Induction and Synchronous Motors and other electro-magnetic and permanent magnet solutions. Linear motors provide precise and accurate controlled acceleration and deceleration at exceptional rates with efficiency and economy in maintenance costs. Linear Motors are used in a vast array of diverse applications and industries, including rollercoasters. Force Engineering and Bunting had previously worked together on product design projects.
For this project, Force Engineering initially contacted Bunting’s Technical Product Manager, Matthew Swallow with the aim of developing a novel magnetic brake for their rollercoaster business. The design brief identified a number of key criteria, of which limiting weight was paramount. Rollercoaster track costs approximately £3,000 per meter due, in part, to the pylons and supporting structure. Subsequently, the weight determines the supporting structure design, with lighter systems lowering the overall cost.
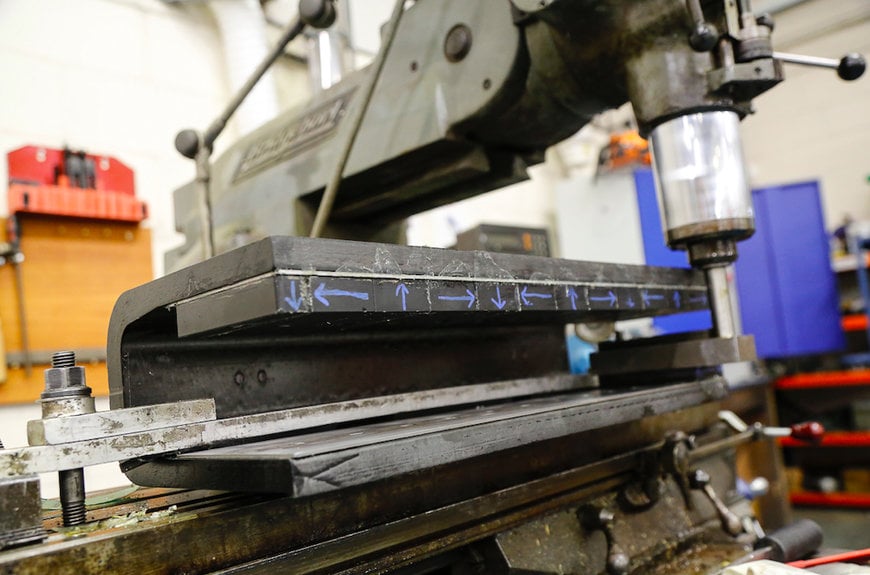
The Magnetic Rollercoaster Brake under construction
This also applies to permanent magnet wind turbines, where neodymium iron boron (NdFeB) permanent magnet motors are preferred to motors using ceramic ferrite magnets. Ceramic ferrite magnets are significantly cheaper but heavier, and a lighter weight motor means a lower cost support pylon with cost savings outweighing the additional magnet cost.
The design project took over two-years, with a number of permanent magnet arrangements considered. These included magnetic Halbach arrays, which are a great way of focusing the flux in a specific direction. However, Halbach arrays are difficult to build and need expert handling. Four to five segment Halbach arrays are the best at focusing the field, but, once again, more segments lead to more material and labour cost.
Using Finite Element Analysis (FEA), the design team determined the most cost-effective magnetic solution that generated the right amount of braking force. The eddy current brake relies on a massive permanent magnetic field between two permanent magnet arrays, with the attraction between these magnets being a key design criterion. Understanding the magnetic force through additional FEA was critical for determining the holding force needed to keep the magnets in place.
A Halbach array is a useful magnetic tool, but it causes adhesive bond lines to be put into a twisting peel effect, producing a form of ‘pull force’ that adhesives do not like. Many iterations of the design looked at bonding the magnets with different coatings to the light weight carbon fibre structure. However, despite the adhesives’ data sheet specifications stating suitability to surviving the environment, none were up to the task when tested in a real-world simulation.
The investigation of alternative methods of magnet retention led the design team to review manufacturing techniques used at one of Bunting’s sister companies in Redditch, UK. Bunting manufactures magnetic separators including hundreds of plate magnets. These are installed in chutes and over conveyors to capture and hold ferrous metal contamination found in foodstuffs and other dry granular materials.
Bunting’s Redditch engineers joined the design team. In collaboration with the Force Engineering team, Bunting adapted the eddy current brake magnet assembly to incorporate a more comprehensive twist-tolerant design which retained the magnets indefinitely. Magnetic braking systems such as this feature on many famous rollercoaster rides In the United Kingdom including Rita at Alton Towers and Stealth at Thorpe Park.
www.bunting-berkhamsted.com