www.industryemea.com
22
'23
Written on Modified on
High Intensity Magnetic Separation at XVIII ECerS
Bunting emphasizes the use of high-intensity magnetic separators to remove iron, iron-bearing, and paramagnetic minerals, reducing defect rates and improving surface brightness.
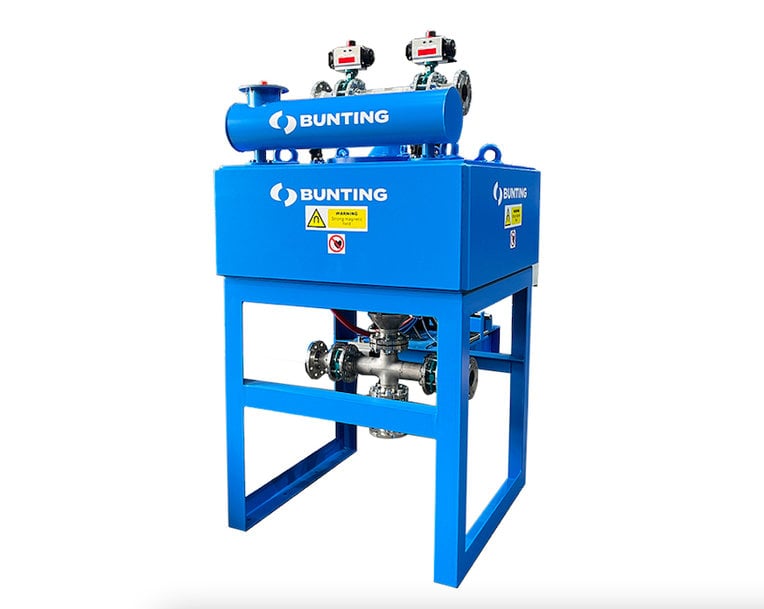
Bunting is one of the world’s leading designers and manufacturers of magnetic separators and metal detectors for the ceramics and mineral processing sectors. The Bunting European manufacturing facilities are in Redditch, just outside Birmingham, and Berkhamsted, both in the United Kingdom.
Materials used in the manufacture of ceramics, such as feldspar, silica sand, and clays, commonly include paramagnetic minerals and fine iron. If left in the raw material during the ceramic manufacturing process, the magnetic contamination causes defects and flaws in the body and on the surface of the finished ceramic product. Also, very fine iron contamination can affect the surface brightness, especially of white glazed products.
Traditionally, ceramic manufacturers have used both electromagnetic and permanent rare earth magnets to capture the magnetic contamination. This technology successfully removes a proportion of the contamination.
To maximise the removal of paramagnetic minerals and fine iron, an increasing number of ceramic producers are investing in high-intensity Electro Magnetic Filters. Electro Magnetic Filters produce a high-intensity magnetic field (up to 40,000 Gauss). Leading European ceramics producers use the technology to remove problematic magnetic particles from slips and glazes.
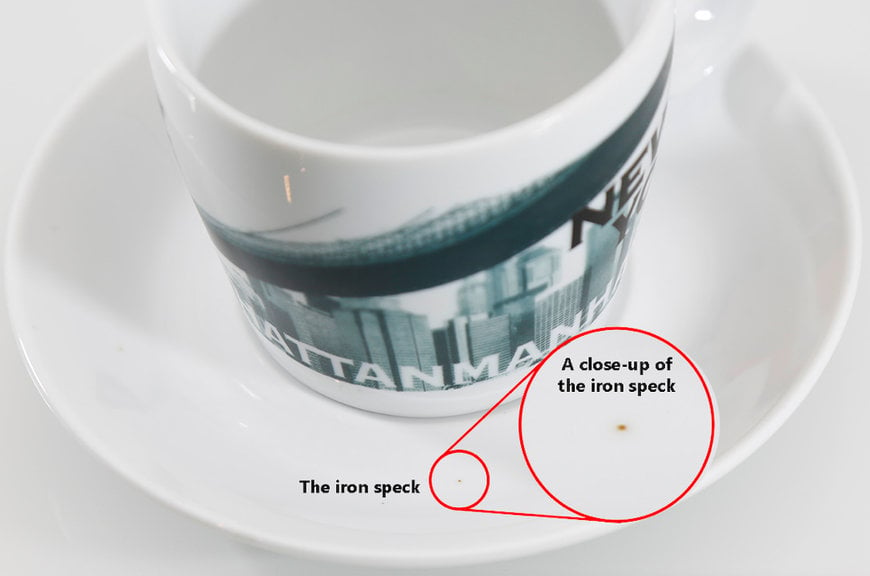
Electro Magnetic Filters consist of an electromagnetic coil positioned around a central hollow core containing a magnetic (400 series) stainless-steel matrix of various designs. The highly-efficient computer designed coil generates a high intensity magnetic field that becomes intensified on the points of the matrix creating the magnetic force needed to separate paramagnetic particles from the slurry.
The magnetic coil is either enclosed in a circular or rectangular steel casing designed to intensify the magnetic field into the hollow centre of the coil. Valves trees (for the product feed and exit as well as cleaning water and air) are mounted on the top and bottom to suit the application and installation. Removal of the captured magnetics inside an Electro Magnetic Filter is either undertaken manually or automatically. For automatic operations, the process is managed through a separate control.
Presently, many European ceramics producers are testing an industrial-scale Electro Magnetic Filter on site. The Electro Magnetic Filter test unit is installed into production lines to assess the performance over an extended period of time. This accurately demonstrates the abilities of the Electro Magnetic Filter and the reductions in magnetic particle related defects.
www.bunting-redditch.com