www.industryemea.com
03
'16
Written on Modified on
Electromechanical Actuators in the Automotive Industry
Roller screw actuators for weld gun applications
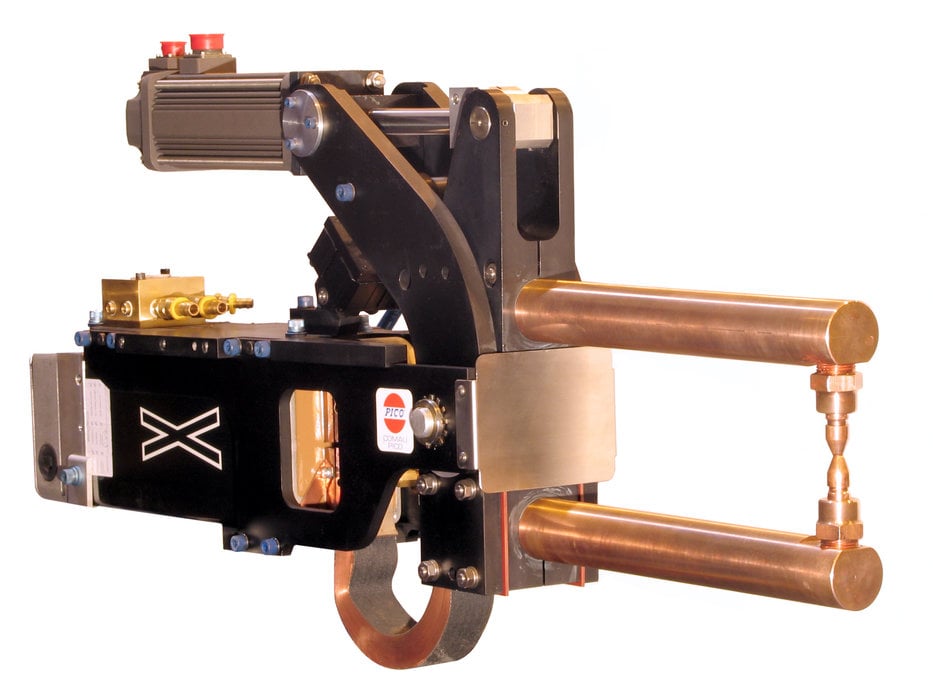
Linear actuation is a core technology for factory automation. Along with fluid power, (hydraulic and pneumatic), electromechanical actuators have become increasingly important in all common industries like packaging, food, energy, process control, construction, and the automotive industry. Manufacturing lines, using linear actuators, are an integral component of today’s industry. However, the air driven systems as well as oil driven systems are riddled with inefficiencies and are difficult to control. In these cases, electromechanical alternatives need to be seriously considered. Different actuator technologies should be explored based on energy efficiency, the way the system is controlled, life time expectation, and space limitations.
A comparison of the three actuator technologies (hydraulic, pneumatic, and electromechanical) reveals startling benefits of electromechanical solutions when compared to traditional fluid power. In the automotive industry today, robotic weld guns represent the most prevalent linear actuator application being converted from fluid power to electromechanical.
Robotic weld gun
Robots are used extensively in automotive production plants throughout the world. The primary application for robots is spot welding of stamped sheet metal parts to form the car chassis. Due to the high number of welds per car, required accuracy and consistency, and the repetitive nature of the work, electromechanical actuators are the best solution.The weld gun itself sits at the end of the robot arm and needs to reach specific positions of the parts of the car chassis.
Although the robots themselves have always been driven by electric servo motors, the weld gun actuators have traditionally been equipped with servo-pneumatic actuators driven by a pneumatic cylinder because of the low acquisition cost and overall simplicity.
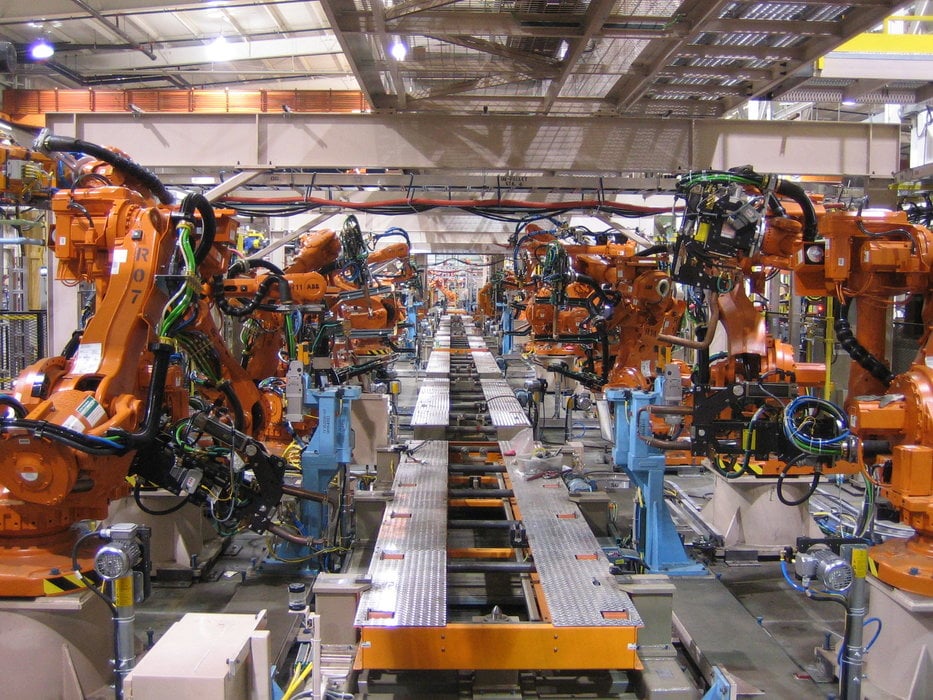
To meet ever-increasing production demands, automation engineers in the automotive industry have increasingly turned to electromechanical actuation solutions to improve their spot welding capability.
A typical alternative is the electromechanical actuator based on ball or roller screw technology.
Different approaches to electric linear actuation
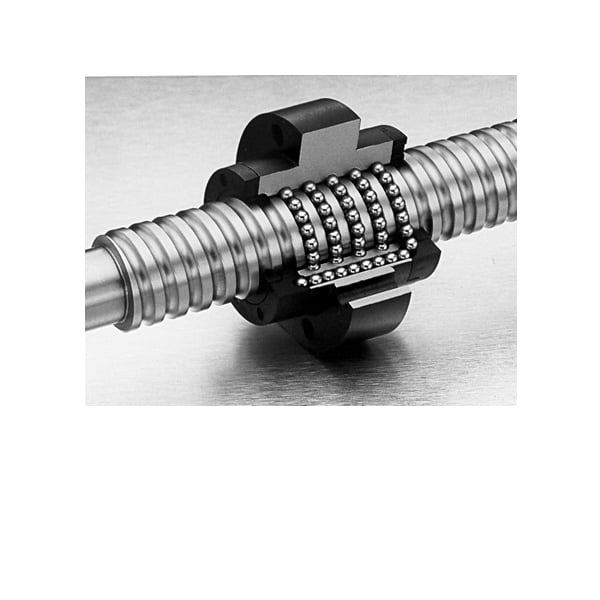
By far the most common electromechanical actuator found in heavy industries (automotive manufacturing) is a rotary servo motor coupled with a rotary-to-linear mechanical transmission such as a ball screw or roller screw.
Ball screws are relatively simple to manufacture, and with many manufacturers in the marketplace ball screws are an affordable alternative. Ball screws consist of a threaded rod (either ground or rolled) and a nut containing ball bearings. Like a nut on a bolt, rotating the nut relative to the rod will cause linear motion of the nut along the rod. When higher life time, higher speeds, and less noise are required, roller screws or roller screw actuators are the preferred choice. Roller screws are similar in principal to ball screws, with a nut running along a threaded rod. Unlike the balls in a ball screw, however, roller screw nuts utilize threaded rollers that are geared with respect to each other and the nut housing much like a planetary gearbox.
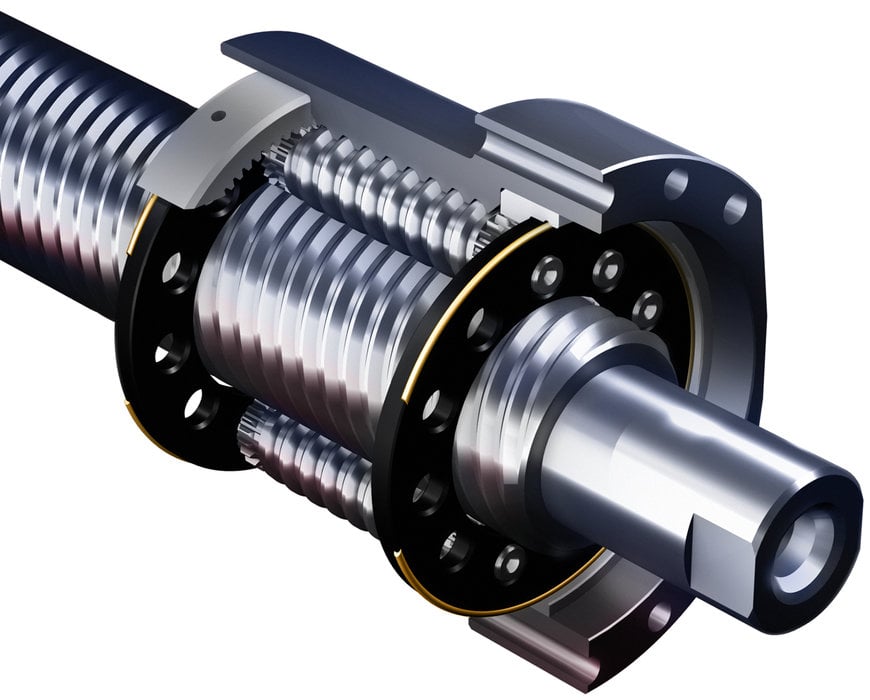
There are three advantages the roller screw has compared to the ball screw:
1. There are more contact points which means the friction force can be spread on a bigger surface. As a result, the friction is less and the life is greatly increased when compared to ball screws.
2. Balls are running in different directions, the rollers that connect the nut with the screw are synchronized to each other. This allows higher rotational and linear speeds.
3. In the ball screw, the balls need to follow a channel that is changing its direction, rollers simply circulate in a synchronized motion around the roller screw. This is why less vibration and noise are generated by a roller screw.
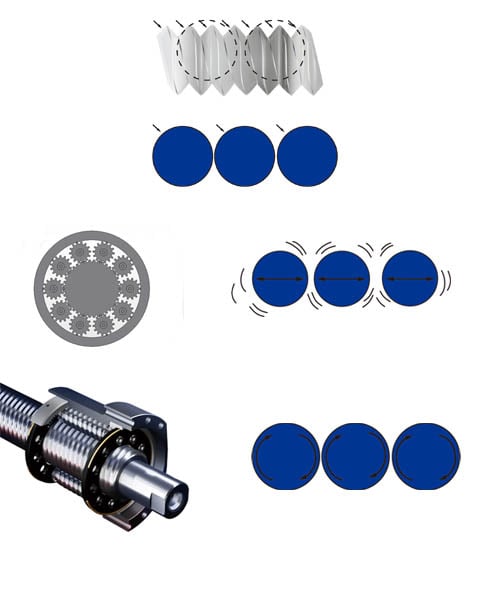
Because of their inherent design advantages, roller screws offer five to 15 times the life of a comparable ball screw. The estimated travel life comparison between a ball screw and a comparably sized roller screw for a given load is shown in the graph on the next page.
Most electromechanical actuators available today consist of a packaged screw mechanism with a separate electric motor mounted either in line with the screw via a flexible coupling or parallel to the screw via a belt and pulley or mechanical gears. As with ball screws, a packaged actuator with external motor is fairly simple to manufacture, and with many competitors in the market is also relatively affordable. However, because the motor is added to the actuator as a separate component, the overall package size is rather large and the weight is quite high. A bigger and heavier actuator requires a larger and more expensive robot. In addition, the combination of a bigger actuator with a larger robot increases overall system inertia resulting in longer cycle times and decreased productivity.
The next development step, is the integration of the motor and roller screw into one unit. The Exlar® GS roller screw actuator combines both, the mechanics of the screw and a servo motor, in one unit. To archive that, the traditional roller screw design is converted into an inverted design. The roller screw nut runs in a ground hollow shaft, that is used as the rotor of the servo motor with shaped neodymium iron boron magnets bonded on. Besides the obviously smaller package size, integration of the motor into the actuator requires fewer number of components leading to better reliability and significant weight savings. Directly coupling the motor to the actuator also eliminates backlash resulting in significantly higher dynamic response and better overall performance. The segmented lamination (T-Lam) stator offers a compact and efficient design with a 80% slot fill with minimized end-turns and a insulation class of 180(H).
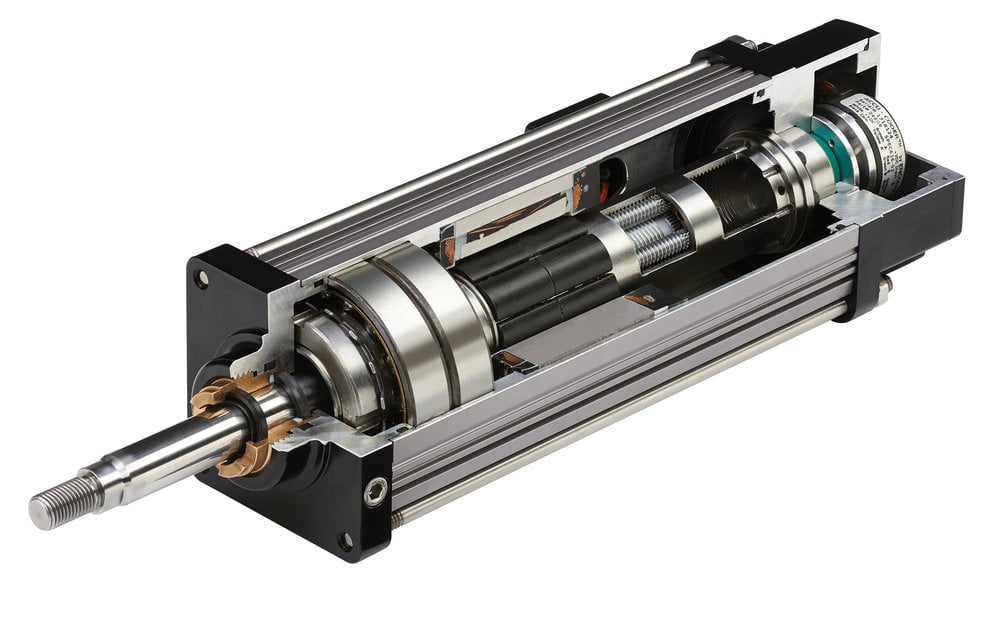
The Exlar GS version of a linear actuator does not separate between the mechanics of the screw and the motor.
The main advantages are:
1. The life of a roller screw
2. The precision of a servo driven motor
3. The compact design of an integrated solution with limited components
Life time expectations
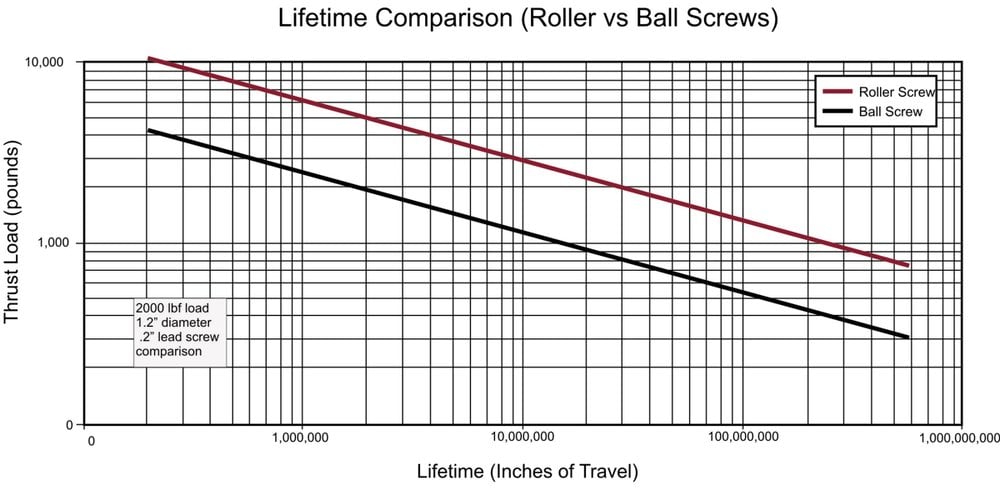
As you would expect, with their higher load capacities, roller screws deliver major advantages in working life. Usually measured in inches or meters of travel, the relative travel life for roller and ball screws are displayed in the graph to the left. In a 2000lbf / 8900N load application, you can predict that the roller screw will have an expected service life that is 15 times greater.
Force repeatability
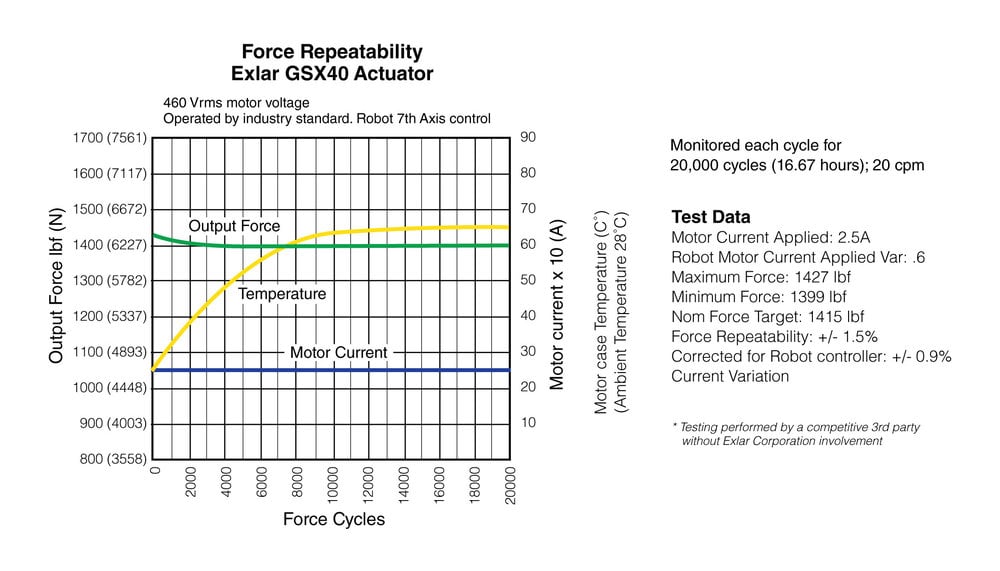
As mentioned previously, weld gun applications require high force repeatability throughout the entire production shift. Maintaining force repeatability can be particularly challenging during the warm-up period after a cold start of the system. As shown on the graph on the right, the force repeatability of an Exlar actuator GSX40 (typically used for weld guns) stays in a range of 0,75% or 50N of its nominal welding force at an ambient temperature of 40°C. This guaranties a constant reliable weld spot over the entire production cycle.
Energy savings
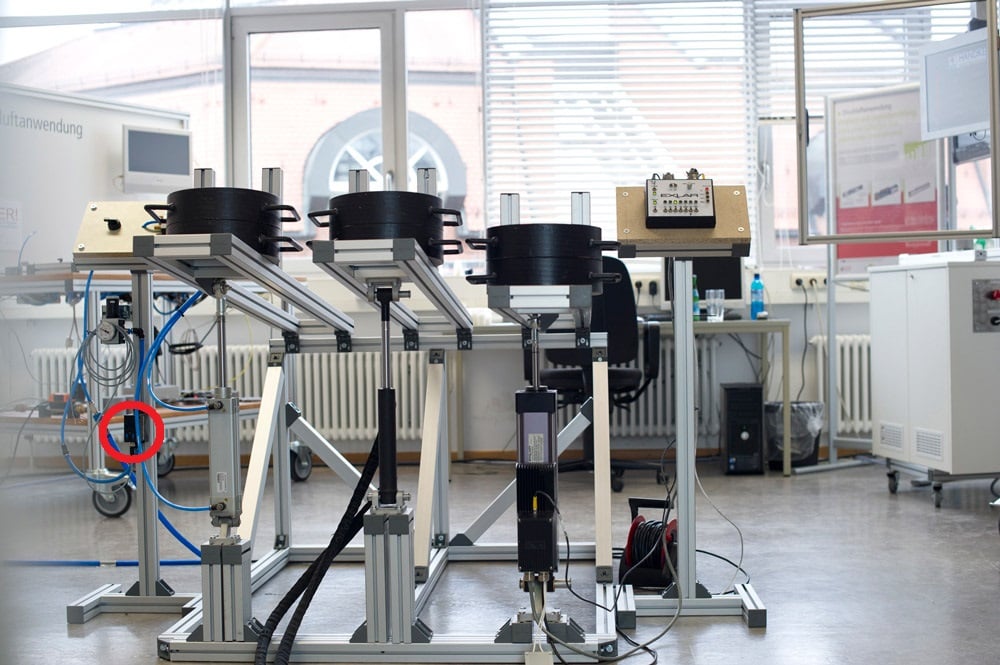
A 2011 study at the University of Kassel in Germany (chair of environmentally sound products and processes) compared the performance of an Exlar electromechanical actuator with comparably sized pneumatic and hydraulic alternatives. They found savings, up to 90%, possible when using electromechanical actuators versus fluid power. Operating under the same load and duty cycle conditions, the hydraulic actuator required 4.4 times more energy than the electromechanical actuator. The pneumatic cylinder required a staggering ten times more energy.
It should be noted, that only one study with specific test parameters and conditions was taken into consideration. However, fluid power systems with all their periphery like hoses, tubes, filters, valves, dryers, pumps on one side, and leaks in their network on the other side, have a much higher consumption of energy than electromechanical solutions.
Hydraulic and pneumatic systems do not completely lose their importance but, from an economic and energy stand point, electromechanical actuation offers many industrial areas a better alternative.
Electromechanical actuators for future weld gun applications
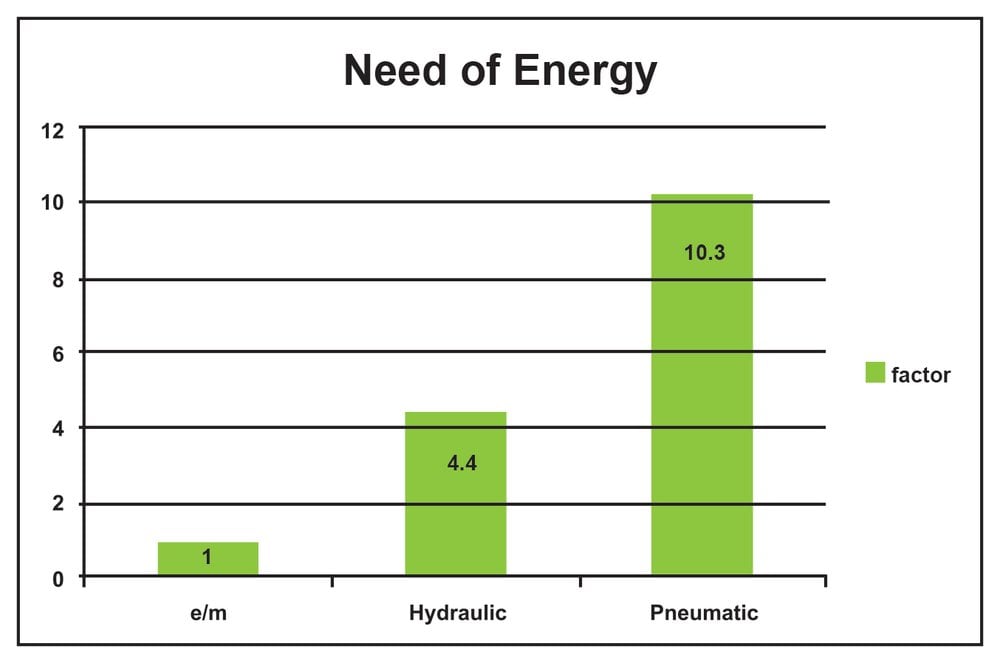
Worldwide there are still more servo-pneumatic driven weld guns in use than electromechanical alternatives. This will most likely change in the coming years because even conservative industries like the automotive industry are thinking about newer, better technologies. We have provided nearly 12,000 Exlar actuators for weld gun applications over the last decade. With their modular design, Exlar actuators offer feedback callouts for almost any servo drive on the market and has successful installations as a 7th axis for Kuka, Comau, ABB, Fanuc, Nachi, and Motoman robots.
Our Exlar actuators are the most compact actuators on the market with many optional features, like an integrated electric brake and integrated load cell to measure the weld force directly from the actuator.
Based on the product we offer and the changes being realized in the automotive market, Curtiss-Wright Corporation considers the automotive market as one of the most important growth markets for its Exlar brand of actuators in the coming years.