www.industryemea.com
21
'24
Written on Modified on
Automation solution from Bosch Rexroth industrializes deep discharge of vehicle batteries
The extraction of primary raw materials is not enough to cover the raw material requirements for the increasing number of electric vehicles.
www.boschrexroth.com
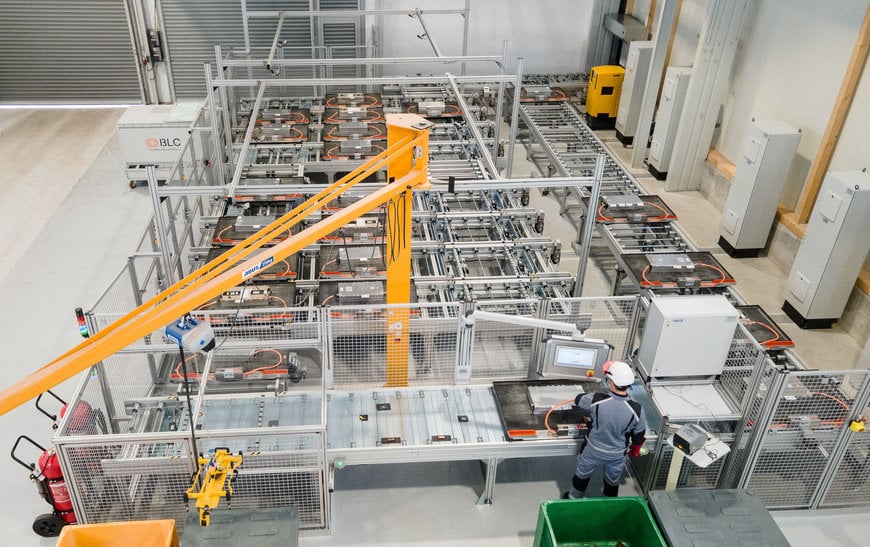
With growing regulatory pressure, the EU Battery Regulation sets specific targets for the recycling of used batteries. Battery recycling and the associated return of raw materials are becoming important building blocks for the development of a European circular economy. With its modular solution kit for the diagnosis, discharge and dismantling of used vehicle batteries, Bosch Rexroth enables the automation of these upstream process steps. The company supplied one of the first automation solution Europe to BLC - The Battery Lifecycle Company.
Rising global sales figures for electric vehicles are increasing the demand for vehicle batteries. The battery is one of the most cost- and resource-intensive components of a battery electric vehicle. As a result, the recycling of batteries is increasingly coming into focus, as up to 95 percent of the chemical elements can be reused and costs reduced.
Upstream processes for preparation and shredding have so far been labor-intensive. Only by automating these process steps is it possible to recycle batteries on an industrial scale. Bosch Rexroth is supplying BLC - The Battery Lifecycle Company, a joint venture between REMONDIS subsidiary TSR Automotive and Rhenus Automotive, with one of the first automated systems for discharging and dismantling battery modules in Europe. The patented solution for the critical step of deep discharging high-performance batteries shortens a process that previously took 24 hours up to less than 15 minutes.
"The automated discharge developed by Bosch Rexroth not only simplifies recycling, it also increases efficiency and safety. Modules can be deep discharged within a few minutes. This is an enormous gain in productivity. Risks such as short circuits and fires are minimized," summarizes Lukas Brandl, Managing Director at BLC - The Battery Lifecycle Company GmbH.
The TS 5 transfer system from Bosch Rexroth transports battery modules from different manufacturers, sizes and types between the diagnostic, discharging and dismantling stations. As a roller conveyor system, it flexibly meets the requirements of recycling plants and is specially designed for transporting heavy loads. After contacting, a modular solution from the automation kit ctrlX AUTOMATION with the control platform ctrlX CORE and the drive system ctrlX DRIVE discharges the battery cells in the discharge station. The drive system absorbs the discharge energy and feeds it back either into an intermediate circuit or the power grid via a DC/DC converter and a grid inverter. The discharging station thus reduces the power requirement of the entire system.
"Thanks to the Bosch Rexroth solution, we are ideally equipped to recover valuable resources and minimize the ecological footprint in the industry. We want to recycle up to 15,000 tons of battery material a year at the Magdeburg location," explains Brandl.
Bosch Rexroth offers the EV Battery Recycling Suite solution kit for the industrial diagnosis, discharging and dismantling of used EV batteries to both plant operators and system integrators. Its modular design enables economical scaling to higher quantities and adaptation to future challenges in battery recycling. Bosch Rexroth relies on open standards throughout for communication and programming. This makes the solution very easy to integrate into the IT structures of different applications.
Rising global sales figures for electric vehicles are increasing the demand for vehicle batteries. The battery is one of the most cost- and resource-intensive components of a battery electric vehicle. As a result, the recycling of batteries is increasingly coming into focus, as up to 95 percent of the chemical elements can be reused and costs reduced.
Upstream processes for preparation and shredding have so far been labor-intensive. Only by automating these process steps is it possible to recycle batteries on an industrial scale. Bosch Rexroth is supplying BLC - The Battery Lifecycle Company, a joint venture between REMONDIS subsidiary TSR Automotive and Rhenus Automotive, with one of the first automated systems for discharging and dismantling battery modules in Europe. The patented solution for the critical step of deep discharging high-performance batteries shortens a process that previously took 24 hours up to less than 15 minutes.
"The automated discharge developed by Bosch Rexroth not only simplifies recycling, it also increases efficiency and safety. Modules can be deep discharged within a few minutes. This is an enormous gain in productivity. Risks such as short circuits and fires are minimized," summarizes Lukas Brandl, Managing Director at BLC - The Battery Lifecycle Company GmbH.
The TS 5 transfer system from Bosch Rexroth transports battery modules from different manufacturers, sizes and types between the diagnostic, discharging and dismantling stations. As a roller conveyor system, it flexibly meets the requirements of recycling plants and is specially designed for transporting heavy loads. After contacting, a modular solution from the automation kit ctrlX AUTOMATION with the control platform ctrlX CORE and the drive system ctrlX DRIVE discharges the battery cells in the discharge station. The drive system absorbs the discharge energy and feeds it back either into an intermediate circuit or the power grid via a DC/DC converter and a grid inverter. The discharging station thus reduces the power requirement of the entire system.
"Thanks to the Bosch Rexroth solution, we are ideally equipped to recover valuable resources and minimize the ecological footprint in the industry. We want to recycle up to 15,000 tons of battery material a year at the Magdeburg location," explains Brandl.
Bosch Rexroth offers the EV Battery Recycling Suite solution kit for the industrial diagnosis, discharging and dismantling of used EV batteries to both plant operators and system integrators. Its modular design enables economical scaling to higher quantities and adaptation to future challenges in battery recycling. Bosch Rexroth relies on open standards throughout for communication and programming. This makes the solution very easy to integrate into the IT structures of different applications.
www.boschrexroth.com