www.industryemea.com
02
'24
Written on Modified on
Bosch Rexroth: Full speed ahead
Hägglunds hydraulic motor from Bosch Rexroth improves performance and safety in roll mills at Freudenberg Sealing Technologies.
www.boschrexroth.com
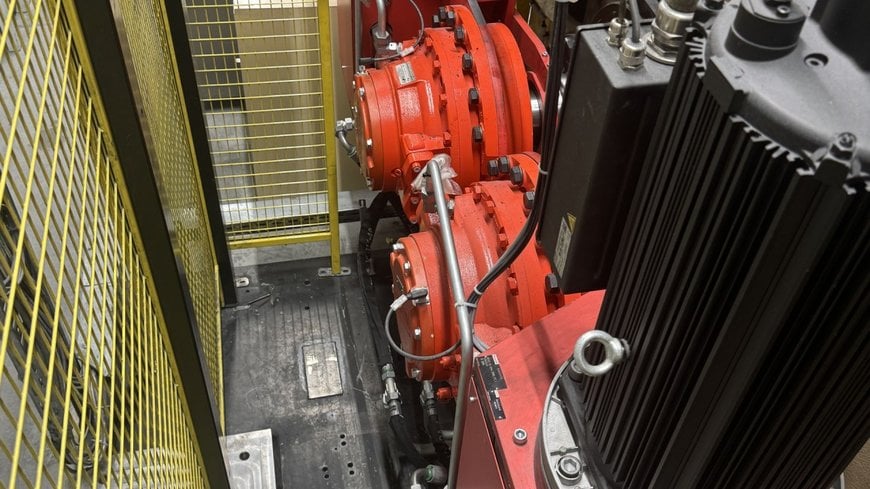
The mixing and processing of raw materials for natural and synthetic rubber requires powerful drives. But energy efficiency and safety are also decisive criteria for the drive technology used in roll mills. At its Berlin location, Freudenberg Sealing Technologies has retrofitted a roll mill’s electromechanical drive with a speed-controlled direct drive from Bosch Rexroth with Hägglunds hydraulic motors. In a comparative analysis of both drive solutions, Hägglunds hydraulic motor impresses on all three aspects.
In the mixing mills at Freudenberg Sealing Technologies, the rubber bales prepared in internal mixers are mixed by repeated retraction, slowly cooled, and drawn off as a blank for subsequent vulcanization. According to Marek Semrau, Senior Global Process Engineer at Freudenberg Sealing Technologies, the required performance characteristics are actually a strong argument for hydrostatic direct drives. However, due to the increased requirements for energy efficiency, roll mills have also been equipped with electromechanical drives in recent years. Freudenberg compared both solutions in practice as part of the conversion of such a drive solution, which has been in operation for five years, to a Hägglunds hydraulic motor by system integrator MaTech – Maschinen und Technik GmbH. The hydrostatic concept was convincing: The company will equip five more roll mills with Hägglunds compact drives from Bosch Rexroth.
The new, speed-controlled compact drive with a continuously variable hydrostatic transmission system is available in six output classes from 15 to 120 kW. Depending on the application, a robust Hägglunds radial piston motor from the Compact CA or Quantum QMX series is used. The hydraulic motor is operated in a closed loop by a variable-speed drive comprising a water-cooled servo motor and axial piston pump. “Such hydrostatic transmissions systems with a variable gear ratio are powerful, quick to control, and low maintenance,” says Jörg Schlegel, Managing Director at MaTech. “At the same time, however, we will also achieve greater energy efficiency.” Comparative measurements at Freudenberg Sealing Technologies show that the solution with hydraulic motor performs at least equally as well as, sometimes even somewhat better than the electromechanical drive, depending on the type of roll mill.
The measurements at Freudenberg also show that the direct drive solution achieves a braking angle of 3.5°, which is significantly shorter than the electromechanical drive’s. This makes retraction into the rollers rotating in opposite directions technically impossible. Bosch Rexroth implemented this using a redundant quick-stop through the electrical resistance in the frequency converter and a mechanical brake in the servo motor.
Another advantage is the hydrostatic solution’s small footprint: It needs about 40 percent less installation space than the electromechanical version. The total weight of the hydrostatic solution is just 13 percent of the electromechanical version, 780 instead of over 6,000 kg per drive. In addition, a mechanical transmission system has to be replaced at least once during the normal service life of 20 to 30 years for roll mills. This is not the case with the hydromechanical drive solution. To increase availability even more, Freudenberg Sealing Technologies monitors important parameters such as oil temperature and filter condition via the drive control or uses the Hägglunds CMp data-based analysis service for predictive maintenance.
In the mixing mills at Freudenberg Sealing Technologies, the rubber bales prepared in internal mixers are mixed by repeated retraction, slowly cooled, and drawn off as a blank for subsequent vulcanization. According to Marek Semrau, Senior Global Process Engineer at Freudenberg Sealing Technologies, the required performance characteristics are actually a strong argument for hydrostatic direct drives. However, due to the increased requirements for energy efficiency, roll mills have also been equipped with electromechanical drives in recent years. Freudenberg compared both solutions in practice as part of the conversion of such a drive solution, which has been in operation for five years, to a Hägglunds hydraulic motor by system integrator MaTech – Maschinen und Technik GmbH. The hydrostatic concept was convincing: The company will equip five more roll mills with Hägglunds compact drives from Bosch Rexroth.
The new, speed-controlled compact drive with a continuously variable hydrostatic transmission system is available in six output classes from 15 to 120 kW. Depending on the application, a robust Hägglunds radial piston motor from the Compact CA or Quantum QMX series is used. The hydraulic motor is operated in a closed loop by a variable-speed drive comprising a water-cooled servo motor and axial piston pump. “Such hydrostatic transmissions systems with a variable gear ratio are powerful, quick to control, and low maintenance,” says Jörg Schlegel, Managing Director at MaTech. “At the same time, however, we will also achieve greater energy efficiency.” Comparative measurements at Freudenberg Sealing Technologies show that the solution with hydraulic motor performs at least equally as well as, sometimes even somewhat better than the electromechanical drive, depending on the type of roll mill.
The measurements at Freudenberg also show that the direct drive solution achieves a braking angle of 3.5°, which is significantly shorter than the electromechanical drive’s. This makes retraction into the rollers rotating in opposite directions technically impossible. Bosch Rexroth implemented this using a redundant quick-stop through the electrical resistance in the frequency converter and a mechanical brake in the servo motor.
Another advantage is the hydrostatic solution’s small footprint: It needs about 40 percent less installation space than the electromechanical version. The total weight of the hydrostatic solution is just 13 percent of the electromechanical version, 780 instead of over 6,000 kg per drive. In addition, a mechanical transmission system has to be replaced at least once during the normal service life of 20 to 30 years for roll mills. This is not the case with the hydromechanical drive solution. To increase availability even more, Freudenberg Sealing Technologies monitors important parameters such as oil temperature and filter condition via the drive control or uses the Hägglunds CMp data-based analysis service for predictive maintenance.
www.boschrexroth.com