www.industryemea.com
09
'24
Written on Modified on
ARCELORMITTAL COMMENCES WORLD-FIRST TRIAL OF NEW TECHNOLOGY TO RECYCLE CO2 EMISSIONS FROM STEEL PRODUCTION
ArcelorMittal Gent is hosting the first industrial trial of D-CRBN’s technology.
corporate.arcelormittal.com
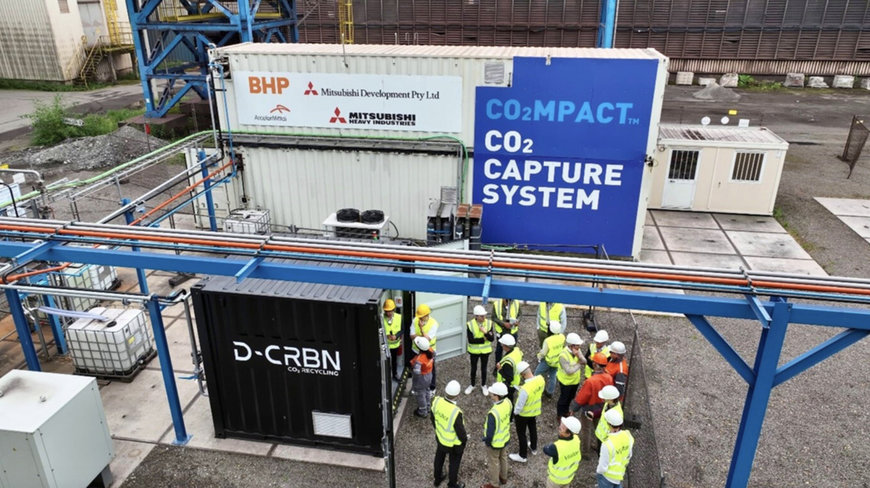
ArcelorMittal and Mitsubishi Heavy Industries, Ltd. (MHI) are working with a climate tech company, D-CRBN, to trial a new technology to convert carbon dioxide (CO2) captured at ArcelorMittal’s plant in Gent, Belgium into carbon monoxide which can be used in steel and chemical production.
This is the first industrial testing of D-CRBN’s plasma technology, making ArcelorMittal Gent the first steel plant in the world to trial the process, which has been designed to reduce CO2 emissions.
This new trial expands the current multi-year carbon capture pilot taking place at the site to test the feasibility of full-scale deployment of MHI's carbon capture technology (Advanced KM CDR Process™).
D-CRBN, an Antwerp-based company, has developed a technology that uses plasma to convert carbon dioxide into carbon monoxide. Using renewable electricity, the plasma is used to break the carbon-oxygen bond, thereby converting CO2 into carbon monoxide. The carbon monoxide can be used as a reductant in the steelmaking process – replacing part of the coke or metallurgical coal used in the blast furnace – or as a basic ingredient in Gent’s Steelanol plant, for chemicals or alternative fuel production.
The D-CRBN process requires high-purity CO2, which can be provided by MHI’s carbon capture unit, currently being used to capture blast furnace off-gases, and off-gases from the hot strip mill reheating furnace, in Gent.
A pipeline between MHI’s carbon capture unit and D-CRBN’s unit was connected on July 1st, to test the feasibility of using the CO2 captured by the MHI technology as a feedstock for D-CRBN. The industrial pilot is an important stage of testing D-CRBN’s technology, to make sure that any impurities that accompany the CO2 produced during steelmaking do not have a detrimental effect on the process and product gas.
ArcelorMittal is pursuing a number of decarbonisation routes in order to achieve its climate targets, which include a 35% reduction in CO2 emissions from ArcelorMittal Europe, by 2030. One of these routes is Smart Carbon steelmaking, which uses circular carbon in the blast furnace, carbon capture and storage (CCS) or utilization (CCU).
www.arcelormittal.com