www.industryemea.com
27
'24
Written on Modified on
Vattenfall Six years of research paves the way for fossil-free iron and steel production on an industrial scale
The report shows that direct reduced iron produced with the HYBRIT process has superior characteristics compared to iron produced with fossil fuels.
group.vattenfall.com
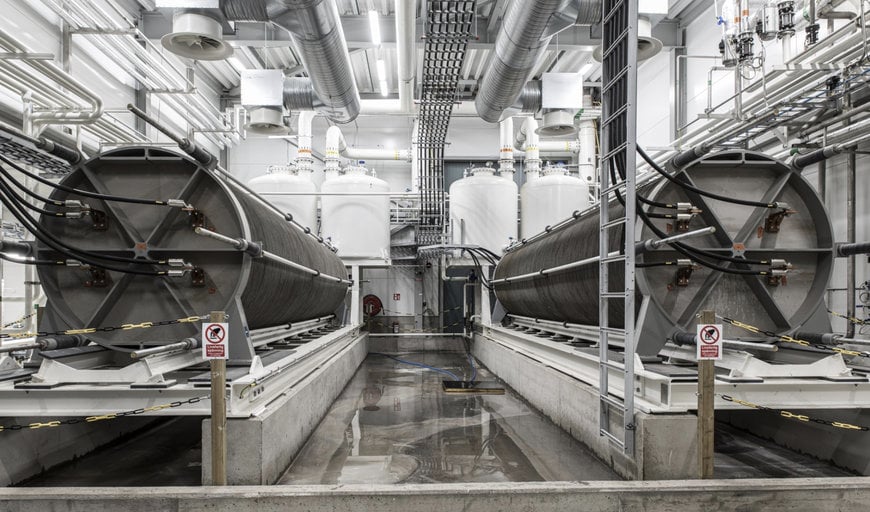
The HYBRIT initiative is a collaboration between the steel company SSAB, the mining company LKAB and the energy company Vattenfall that was launched to fundamentally change the iron and steel industry. The initiative aims to virtually eliminate carbon dioxide emissions in the steel industry by replacing coal and coke in the production of iron with fossil-free hydrogen and electricity. The transition from coal and blast furnace-based steelmaking to HYBRIT technology and the melting of iron in electric arc furnaces is expected to reduce Sweden's total carbon dioxide emissions by more than 10 percent.
The project is the first in the world to demonstrate that the fossil-free value chain - from iron ore to steel - works on a semi-industrial scale. So far, more than 5,000 tonnes of hydrogen-reduced iron have been produced at HYBRIT's pilot plant in Luleå. Customers such as Volvo Group, Epiroc, Peab and many more are already using the fossil-free steel in vehicles, heavy machinery, buildings and consumer products, and interest in the technology is high.
Results from six years of research prove HYBRIT's fossil-free process
The research results now presented in a final report to the Swedish Energy Agency span from 2018 to 2024, with a focus on scaling up technical solutions from the laboratory to industrial scale, developing an industrial process practice and achieving an integrated value chain for hydrogen-based iron and steelmaking.
Examples of results from the pilot phase are: the development of a new hydrogen-based technology for efficient fossil-free iron and steel production with 0.0 tonnes of CO2 emissions per tonne of steel, the development of a new fossil-free iron product (sponge iron) that has significantly better properties than iron reduced with fossil gases such as natural gas, the successful long-term operation of alkaline electrolysers for the production and storage of hydrogen, and the development of an efficient process practice for melting fossil-free sponge iron into crude steel in an electric arc furnace.
“The focus of HYBRIT's technical development has been to build up expertise and create technical conditions for the implementation of a fossil-free process in a full-scale production. We are very pleased that we as a team have been able to deliver successful results that have met or exceeded the set project goals. The knowledge and experience we have developed during the project will now be focused on continuing the process development, primarily to support the owners’ industrialisation projects,” says Ulf Spolander, General Manager of Hybrit Development AB.
The HYBRIT project moving into the next phase
The results from the pilot phase pave the way for implementing the HYBRIT process on an industrial scale. Hybrit Development AB will continue to conduct research and development to support the industrialisation of the technology together with the owner companies, including delivering solutions to LKAB's planned demonstration plant in Gällivare. The pilot project for storing fossil-free hydrogen in Svartöberget in Luleå will continue until 2026.
“It has been a groundbreaking journey in a short period of time. The results from the pilot phase show that the process works and that we are ready for the next stage, where the demonstration plant that LKAB plans to build in Gällivare will be the first step towards industrial production of sponge iron. Our high-quality iron ore combined with good access to fossil-free energy provides unique conditions for establishing a competitive value chain for future fossil-free iron and steel production,” says Jenny Greberg, Vice President Technology at LKAB and board member of Hybrit Development AB.
“It is very gratifying to see the positive results of our targeted collaboration, partnership is a recipe for success. The next step is to scale up to an industrial scale where fossil-free electricity and hydrogen enables the transition to a future where it is possible for everyone to transport, produce and live fossil-free,” says Andreas Regnell, Head of Strategic Development at Vattenfall and board member of Hybrit Development AB.
The HYBRIT project has been awarded funding by the EU Innovation Fund and by Industriklivet. It is also part of the European IPCEI project Hy2Use (Hydrogen), which involves a total of 35 projects from 12 countries to support rapid transition and increase the competitiveness of the European industrial sector.
HYBRIT – extract of research results 2018–2024
- Development of a new hydrogen-based technology that enables efficient fossil-free iron and steel production with 0.0* tonnes of CO2 emissions per tonne of steel (scope 1 and 2).
- Development of a new iron product, sponge iron, which has significantly better properties than iron reduced with fossil gases such as natural gas. HYBRIT's iron product is carbon-free and has a high metalization degree (98-99%); it is more resistant to mechanical pressure, drops and abrasion than comparable industrial references and has stable chemical properties. All in all, this means advantages in transport, storage and melting.
- CO2 emission evaluations for hydrogen reduction compared to fossil gas reduction. HYBRIT's process converts iron ore pellets into iron (sponge iron) using only fossil-free hydrogen, with water as the only by-product. This differs from conventional direct reduction technologies that rely on natural gas, which emits carbon dioxide. Direct reduction with hydrogen and melting in an electric arc furnace produces 42 kg of biogenic CO2 per tonne of directly reduced iron, compared to 383 kg of fossil CO2 per tonne in a conventional natural gas process where the heating of the reduction gas is excluded from the comparison.
- Development of a new fossil-free and competitive industrial process where 175 process modes have been tested to identify the most favourable way to produce iron with hydrogen.
- Successful long-term operation of alkaline electrolysers for hydrogen production and storage. The electrolysers are used to split water into hydrogen and oxygen using fossil-free electricity. The hydrogen is then used to remove the oxygen from the iron ore pellets. Tests using stored hydrogen in real time against the electricity market show that the variable cost of hydrogen production can be reduced by up to 40 percent.
- Development of an efficient process practice for melting fossil-free sponge iron into crude steel in an electric arc furnace, carried out in collaboration with the Swerim research institute. The steel is produced by melting the fossil-free sponge iron with fossil-free electricity together with minimal additions of biocarbon, oxygen and slag formers. The experimental results show that the fossil-free melting practice developed produces a steel of the same high quality as today's fossil ore-based steel.
*The process produces small emissions of carbon dioxide due to the consumption of graphite electrodes and the addition of slag formers in the electric arc furnace. These emissions are less than 0.05 tonnes CO2e/tonne of steel, rounded to 0.0 tonnes CO2e/tonne of steel. Typical value for ore-based steelmaking with blast furnace technology is 2.2 tonnes CO2e/tonne steel.
www.group.vattenfall.com
www.group.vattenfall.com