RAMPF Presents Comprehensive Composite Portfolio at JEC World
The international RAMPF Group is presenting high-performance tooling boards, Close Contour Castings, and liquid resin systems together with engineered composite manufacturing solutions at JEC World from March 4 to 6 in Paris – Hall 5 / Booth 5G117.
www.rampf-group.com
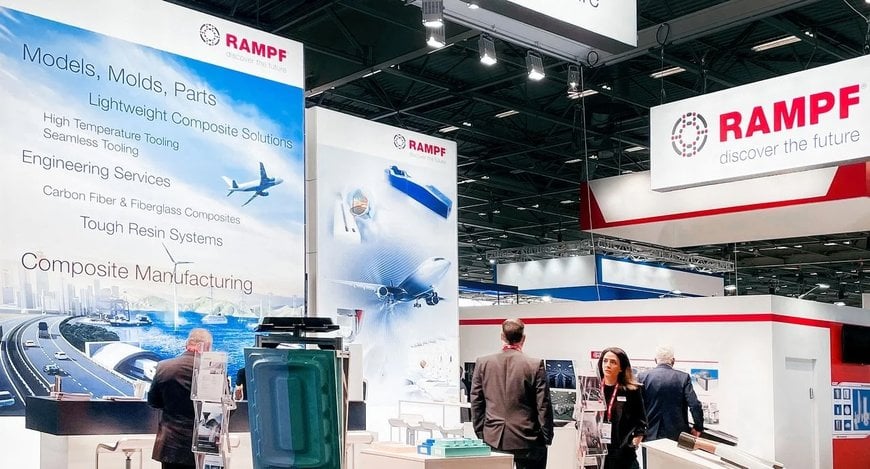
RAKU® TOOL liquid resin systems by RAMPF Group, Inc.
High-performance structural resins developed by RAMPF’s US subsidiary enable low-temperature processing, eliminating the need for costly equipment. This innovation significantly reduces both the cost and lead time for prototyping and early builds, effectively mitigating financial and scheduling risks in development projects. The material processing characteristics also allow for scalability, enabling high-rate manufacturing. Additionally, the resins are fully compatible with RAMPF’s tooling board portfolio and can be formulated to meet various FST requirements, including FAR 23.1193, FAR 25.853, and FAR 25.855.
RAKU® TOOL tooling boards and Close Contour Castings by RAMPF Advanced Polymers
RAKU® TOOL tooling boards based on epoxy exhibit outstanding mechanical properties, finest surface structures, and high dimensional stability. The boards are easy and quick to machine and compatible with all industry-standard prepregs, release agents, and paints.
JEC 2025 product highlight: RAKU® TOOL WB-0890, specially developed for the composites industry. Its exceptionally fine surface structure minimizes finishing effort and reduces the consumption of sealing systems. Additionally, the high-quality surface can be seamlessly transferred from the master model to the prepreg mold, eliminating the need for re-sanding and significantly extending the mold’s service life.
RAKU® TOOL Close Contour Castings made from polyurethane are delivered as a ready-to-machine monolithic casting, free of bonding lines and closely approximating the final part contour. This significantly reduces both milling time and material waste.
JEC 2025 product highlight: RAKU® TOOL CC-6503 Close Contour Casting features a dense structure, a fine, homogeneous surface, and excellent milling properties. The Close Contour Casting demonstrates exceptional dimensional stability, thanks to minimal residual stresses achieved through RAMPF's specially developed casting process.
Sustainable tooling solutions– RAMPF Advanced Polymers is a pioneer in the chemical recycling of polyurethane. The raw materials obtained with the company’s groundbreaking technologies are used in both customers' and RAMPF’s own products:
- RAKU® TOOL boards contain up to 30% raw materials from chemical recycling.
- Up to 50% of production residues are recycled via RAMPF’s innovative closed-loop process.
- Using RAKU® TOOL board material reduces CO2 by over 90% compared to aluminum.
In addition to its commitment to recycling, RAMPF Advanced Polymers has implemented further sustainable initiatives, including the use of sustainable packaging, the integration of solar and geothermal energy, and the installation of electric vehicle charging stations at its facilities.
RAKU® TOOL liquid resin systems by RAMPF Group, Inc.
High-performance structural resins developed by RAMPF’s US subsidiary enable low-temperature processing, eliminating the need for costly equipment. This innovation significantly reduces both the cost and lead time for prototyping and early builds, effectively mitigating financial and scheduling risks in development projects. The material processing characteristics also allow for scalability, enabling high-rate manufacturing. Additionally, the resins are fully compatible with RAMPF’s tooling board portfolio and can be formulated to meet various FST requirements, including FAR 23.1193, FAR 25.853, and FAR 25.855.
RAMPF’s structural resin portfolio encompasses three distinct product variants:
- High Performance: RAKU® EI-2510 resin infusion system for high performance composite parts with excellent fracture toughness, very good flow, gel time 110 minutes at 60°C, and temperature resistance up to 209°C.
- Advanced Performance: RAKU® EI-2511 infusion system for aircraft composites, meeting interior, cargo, and firewall requirements; features high wet Tg, very good flow, gel time 130 minutes at 60°C, temperature resistance up to 155°C, and flame retardant properties.
- Standard: RAKU® EI-2518 infusion system for FST aerospace and automotive applications with a temperature resistance up to 145°C, low smoke density, and flame retardant properties.
Engineered composite manufacturing solutions by RAMPF Composite Solutions
RAMPF Composite Solutions designs and manufactures some of the world’s most advanced lightweight composite products for industries such as aerospace, defense, industrial, medical, high-end consumer, and green transportation. The full potential of composite technology is leveraged for both low-volume production, early product development, and series production through the combination of:
- Low-cost tooling and fixtures with outstanding mechanical properties
- High-performance structural resins for effective and fast Infusion
- Structural optimization via Tailored Fiber Placement (TFP) technology for maximum speed and accuracy
- Low-cost component production using Vacuum Assisted Resin Transfer Molding (VARTM)
The company's innovative, quick-turn solutions encompass material qualification, integrated quality assurance, and automated processes for manufacturing components and subsystems. Prototypes are produced within weeks of the design stage, achieving up to 30 percent cost savings compared to traditional prepreg solutions.
These benefits are particularly significant for components with high structural and geometric complexity, such as undercuts, compound curvatures, and pockets, as well as functional complexity, including EMI shielding, static discharge, impact resistance, and flammability compliance.
www.rampf-group.com