www.industryemea.com
26
'21
Written on Modified on
Decentral automation of hygienic processes up to field level. Control head with IO-Link for intelligent communication
Thanks to the new IO-Link communication interface, the universal valve control head Type 8681 from Bürkert Fluid Control Systems ensures cost-effective data transfer for Industry 4.0 applications in the processing sector. Operating data and diagnostic data are now always available at control level and enable simple start-up, online parameterisation and preventive maintenance.
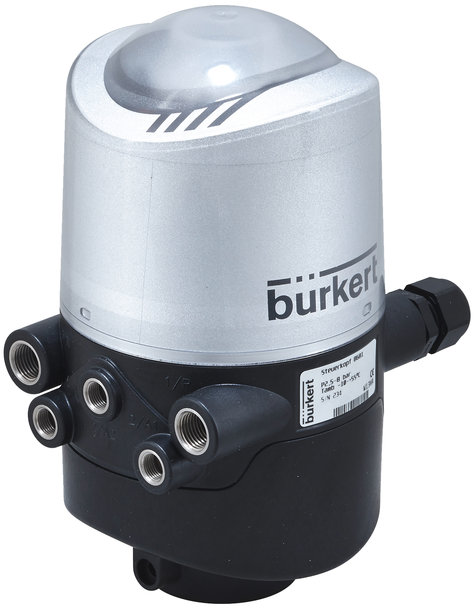
Control heads now assume complete control of pneumatic valves, including feedback and diagnostic functions, for decentral automation concepts. They are used, for example, in the pharmaceutical, beverage and food industries, as well as in biotechnology. In order to meet requirements in the future, Bürkert Fluid Control Systems has now upgraded its proven, intelligent control head Type 8681 with an IO-Link interface (Image). The control head is equipped with a universal actuator adapter. As such, the most hygienic process valves available on the market can be connected to the control level via IO-Link and Industrial Ethernet or fieldbus systems.
Easy start-up and parameterisation
Through the use of standard connection technology, the field devices can be integrated into the controller and started up with little wiring effort. Also re-parameterisation in case of device exchange, e.g. during maintenance, is quick and easy, since the device configuration is stored centrally and can be retrieved automatically. Process valves that are used to control process and auxiliary media, e.g. for cleaning-in-place (CIP), can be automated and operated effectively and efficiently.
Diagnostic data for greater process reliability
The IO-Link communication interface opens up many new opportunities for the proven control heads to make processes even more reliable. In addition to process data, e.g. the set-point position, additional device data and diagnostic information, such as status messages or the number of switching cycles, can be exchanged digitally between the controller and the shutoff valves from the process area via IO-Link Master. This enables preventive maintenance and increases system availability.