www.industryemea.com
30
'23
Written on Modified on
Understanding the thermal parameters of coreless DC motors
Article by Manoj Pujari, Portescap engineer, discusses the importance of thermal parameters for DC motor selection.
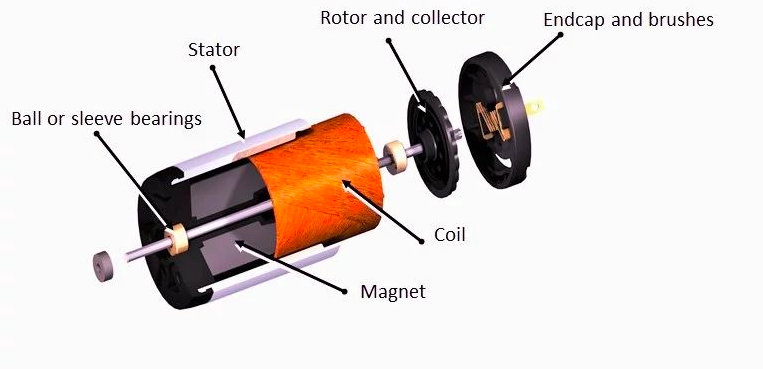
A motor’s dissipated heat energy is calculated as the difference between the electrical input power, and the mechanical output. The dynamics of this system are based on thermal resistance, involving thermal conductivity and the ability to dissipate the generated heat. This is balanced by thermal capacitance, relating to the material’s heat absorption properties.
While a motor’s mechanical components, like brushes, magnets, and ball bearings have thermal considerations of their own, the coil and stator play a significant role in determining thermal design. Responsible for generating the electromagnetic field that turns the rotor, the coil creates significant heat at current values exceeding thermal limit.
Coil & stator
The coreless coil is typically made of copper, and the number of turns determines the resulting magnetic field strength. When supplied with current, the coil generates heat due to electrical resistance, which must be dissipated to prevent overheating. Some of this heat will be taken up by the thermal capacitance of the coil. Heat will also be dissipated to the stator through the air gap that lies in between, which also offers thermal resistance. The stator that surrounds the motor guides the magnetic field generated by the coil and dissipates the heat to the environment.
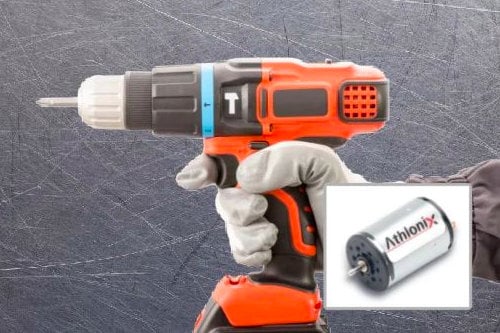
Coreless DC motors ensure reliable, efficient operation of battery-operated power tools
Thermal model and motor selection
To establish a thermal model for motor design and selection, thermal resistance combines the cumulative effects of the different modes of heat transfer via conduction, convection, and radiation that take place during motor operation. The classic thermal model for the DC coreless motor includes the thermal resistance between the coil and stator, and the thermal resistance between the stator and ambient condition. The higher the thermal resistance, the slower the heat transfer, and this rate is usually estimated experimentally. Thermal capacitance is established by multiplying the mass of the material by its specific heat capacity. The higher the thermal capacitance, the greater the heat that can be stored within the material.
Equilibrium or imbalance
When selecting a motor to ensure optimal thermal conditions, a steady state is the desired objective, as long as the input power or current is constant. After the initial transient period of heating of the motor, a stable temperature is reached, where heat generated is equal to that dissipated. Alternatively, a transient state refers to a thermal imbalance where the temperature inside the motor is changing over time.
To achieve a temperature balance, it’s important to understand the motor’s thermal time constant, the factor that determines how quickly a steady state is reached. The thermal time constant also measures the rate at which the motor can respond to thermal changes.
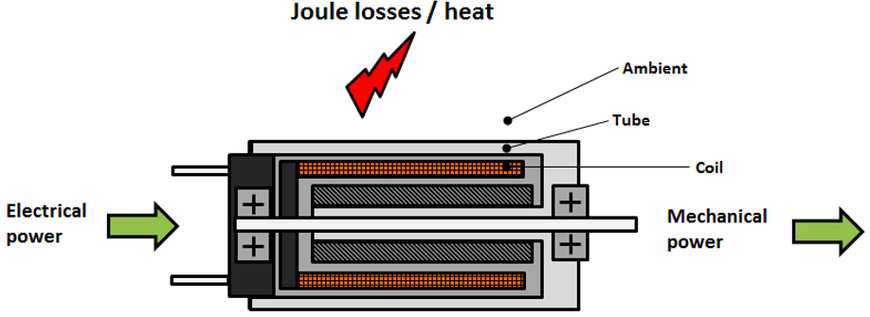
Heat dissipation in a coreless DC motor
Limits and efficiency
To avoid damage to the motor, it’s crucial that the thermal limit isn’t exceeded. The thermal limit refers to the coil, and typically ranges between 100 and 125°C, and places a limitation on the maximum continuous current draw. For continuous application, motor selection should ensure that generated torque keeps within 80% of its maximum continuous level in order to maintain a margin of safety on the thermal limit. Pulse duty applications, however, can exceed this level for short periods.
Defining thermal efficiency, the motor regulation parameter (R/k2) shows the capability of converting the electrical input to mechanical power, and also helps define heat losses. Higher thermal efficiency is critical for applications such as battery-operated devices, which can impact footprint size and weight, as well as required heat dissipation techniques.
Selection of a coreless DC motor’s wider thermal requirements is also dependent on the mechanical assembly, as well as the motor housing, overall motor size, and the integration of cooling technologies. While optimising thermal performance can be a complex task, Portescap’s engineering team works alongside OEM designers to ensure development of the right motion solution to achieve the desired operational and commercial requirements.
www.portescap.com