www.industryemea.com
20
'23
Written on Modified on
Staying ahead of the motor efficiency game
By Marek Lukaszczyk, European and Middle East marketing manager at WEG, highlights the importance of motor efficiency in 2023 and how manufacturers can stay ahead of the curve.
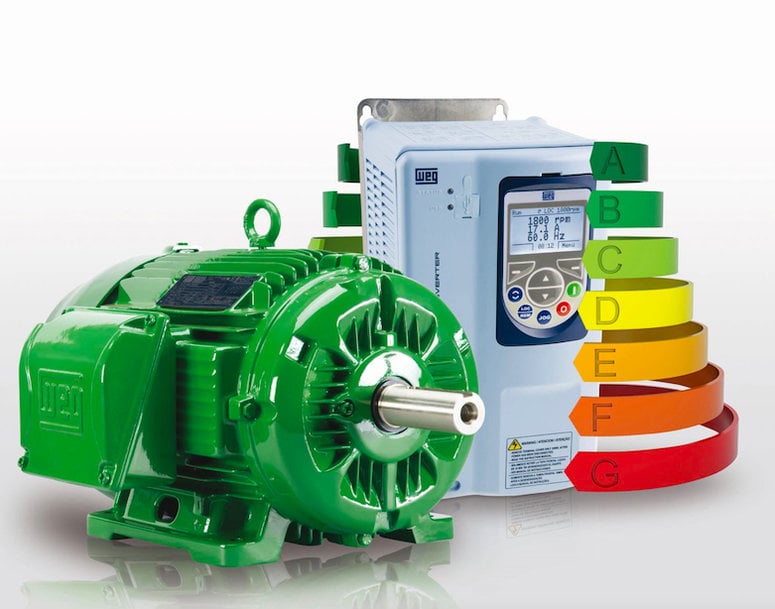
According to the International Energy Agency (IEA), the industrial sector accounted for 37 per cent of total global final energy use in 2022, compared with 33 per cent in 2000. With all eyes on efficiency, manufacturers must ensure that they comply with a new phase of EU eco-design legislation, introduced on July 1, 2023.
Energy efficiency in manufacturing and other industrial facilities starts with choice of equipment. While improving efficiency should be a facility-wide strategy, having an asset-level understanding of energy consumption allows businesses and operators to identify inefficiencies at the more granular level and make the necessary changes.
Currently, around 8 billion electric motors are currently used in the EU, consuming almost half of the electricity that Europe produces. Their prominence means that manufacturing and other industrial facilities can make significant energy savings by ensuring their electric motors make the grade.
A shift in the rules
Previously, efficiency standards for motors and variable speed drives (VSDs) in Europe were set out in EU 2019/1781, which, in July 2021, repealed and replaced the existing regulation on eco-design for electric motors (EC) No 640/2009. In so doing, it brought reductions in energy consumption, while maintaining required safety standards. At the time, EU 2019/1781 expanded the regulation to cover single-speed, three-phase 50 Hz or 60/60 Hz induction motors with two to six poles, a rated output of 0.75 to 375 kW and a rated voltage of up to 1,000 V.
On July 1, 2023, this legislation entered a new phase and efficiency rules now apply to single-phase motors rated 0.12 kW and above. Before they can be used in any machinery or industrial facility, these single-phase motors must meet IE2 levels. The other big change for manufacturers is that they will need to purchase IE4-rated motors if they require an output of between 75 and 200 kW.
Therefore, at a time when energy costs and sustainability dominate the industrial agenda, the next phase of EU 2019/1781 will push the boundaries of what was already a significant shift in the EU’s efficiency drive. Regardless of whether the manufacturer is operating in the EU, UK or elsewhere, if they are using a motor or variable speed drive (VSD) that falls under the scope of the new phase of regulations, compliance must be demonstrated.
The value of an upgrade
Many motors used in manufacturing, oil and gas and other industrial settings are low efficiency, which can have a negative impact on asset costs and productivity. Energy consumption accounts of 96 per cent of the total lifecycle cost of an electric motor, so it pays to opt for a premium efficiency product.
With age comes risk. Many older motors have at some point been rewound because of copper coil failure, but this process can reduce motor performance efficiency. Therefore, at the very least, manufacturers should complete a cost benefit analysis prior to rewinding to determine if purchasing a higher efficiency motor is more economically beneficial. Although exact benefits will vary depending on the application, selecting high efficiency motors will often result in a good return on investment.
Motor sizing
While the legislation requires manufacturers to use compliant motors, there are ways to improve efficiency beyond upgrading. For example, an electric motor must be properly dimensioned according to its real load if it’s to deliver maximum return. An oversized motor, with the actual load being less than 50 per cent of the rated load, will have a lower efficiency and power factor values than one that is sized appropriately.
When retrofitting any motor, sizing and efficiency should both be considered. Depending on the sector, there might be additional considerations. For example, explosion proof ATEX motors in oil and gas applications may face design constraints like deration for VSD operation or a reduced starting current. This could lead to the motor needing a larger frame size, as well as other considerations.
Digitalisation and condition monitoring
Harnessing the latest technology for asset monitoring can allow manufacturers to understand the operational status of their electric motors, as well as other equipment such as VSDs, soft starters and gearboxes. There is an increasingly wide range of Internet of Things (IoT) fleet management solutions available, which manufacturers can deploy.
Platforms such as WEG’s Motion Fleet Management (MFM) complements conventional asset monitoring by providing real time insights into the performance of motors and drives from anywhere in the world. These include built-in predictive maintenance analytics that can help identify future problems, preventing shutdowns and flagging issues, such as overheating, that could result in a motor running inefficiently.
Manufacturing and many other industries must make sure they are compliant with the latest changes in EU eco-design legislation. However, efficiency means more than just upgrading. The new motor must be sized correctly for the application, and, by integrating smart asset monitoring technology, they can be confident that any inefficacies will be flagged early.
Visit the WEG website to find out how you can improve electric motor efficiency.
www.weg.com